Does a windmilling propeller create more drag than a stopped propeller in an engine out scenario?Why is *vertical* autorotation in a helicopter not recommended?Why does this calculation show Gustave Whitehead's propellers were more than 100% efficient?About how much drag does a non-operating engine create?why are airplane propellers always undersized?Is there any legitimate reason for adding momentary power when descending at idle with full carburettor heat on?Guidelines for using a constant speed/adjustable pitch propellerWould an aircraft with no ailerons, no elevators and no rudders be safely flyable?How did the controls work for variable-pitch props?Is 1 propeller always more efficient than 2?Does RPM refer to the speed of the engine or the speed of the propeller?Difference between constant speed and variable pitch propellers?
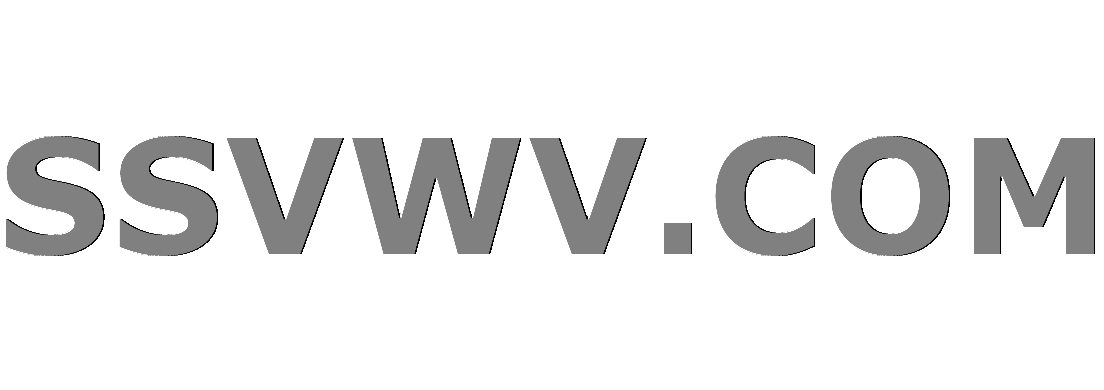
Multi tool use
Why is Colorado so different politically from nearby states?
Why does my electric oven present the option of 40A and 50A breakers?
How can a single Member of the House block a Congressional bill?
Is having a hidden directory under /etc safe?
Is there a rule that prohibits us from using 2 possessives in a row?
If Sweden was to magically float away, at what altitude would it be visible from the southern hemisphere?
What if you don't bring your credit card or debit for incidentals?
Select row of data if next row contains zero
Why were the Night's Watch required to be celibate?
Why don't I have ground wiring on any of my outlets?
The qvolume of an integer
How can I offer a test ride while selling a bike?
Why use water tanks from a retired Space Shuttle?
How does increase in volume change the speed of reaction in production of NO2?
Why would Lupin kill Pettigrew?
Is it possible to kill all life on Earth?
Do adult Russians normally hand-write Cyrillic as cursive or as block letters?
Can I ask a publisher for a paper that I need for reviewing
Looking for an old image of designing a cpu with plan laid out / being edited on a literal floor
What does War Machine's "Canopy! Canopy!" line mean in "Avengers: Endgame"?
Can you please explain this joke: "I'm going bananas is what I tell my bananas before I leave the house"?
Different PCB color ( is it different material? )
What is a simple, physical situation where complex numbers emerge naturally?
Scala list with same adjacent values
Does a windmilling propeller create more drag than a stopped propeller in an engine out scenario?
Why is *vertical* autorotation in a helicopter not recommended?Why does this calculation show Gustave Whitehead's propellers were more than 100% efficient?About how much drag does a non-operating engine create?why are airplane propellers always undersized?Is there any legitimate reason for adding momentary power when descending at idle with full carburettor heat on?Guidelines for using a constant speed/adjustable pitch propellerWould an aircraft with no ailerons, no elevators and no rudders be safely flyable?How did the controls work for variable-pitch props?Is 1 propeller always more efficient than 2?Does RPM refer to the speed of the engine or the speed of the propeller?Difference between constant speed and variable pitch propellers?
$begingroup$
For this question lets assume that we are talking about a fixed pitch propeller and not a variable pitch propeller. I do understand that variable pitch props should be feathered during an engine failure.
The main rationale for this question is this statement that I found in a pilot forum:
I've been doing some research on something I hard from my old chief CFI a couple years back, but I'm not finding much on it. He is the only person I've heard this from, and any CFI, DPE, ect. I've talked about this to since have not heard of it. That being that when you have an engine failure more than several thousand ft. with a non-full-feathering prop, that you should pitch up and decrease airspeed, sometimes to an intentional stall, to stop the rotation of the prop/engine. (Of course, only after you have attempted to restart.) The reason being that you will see a greater gain in glide distance by reducing the drag created by forcing thee air to turn over the engine. He claimed that while you would most likely be off of Vl/d for a short amount of time, thus not gliding in the most efficient manner, that is outweighed by the decrease in drag. (As I said, do this only with several thousand feet and plenty of time.) He claimed that in the case of something such as a 172, doing this procedure at, say 10,000ft, you would gain several more miles of glide distance.
So what I am asking for is if indeed a windmilling prop has more drag than a stopped prop and if so would it be beneficial to follow the advice in the pilot forum?
aerodynamics propeller engine-failure
$endgroup$
|
show 9 more comments
$begingroup$
For this question lets assume that we are talking about a fixed pitch propeller and not a variable pitch propeller. I do understand that variable pitch props should be feathered during an engine failure.
The main rationale for this question is this statement that I found in a pilot forum:
I've been doing some research on something I hard from my old chief CFI a couple years back, but I'm not finding much on it. He is the only person I've heard this from, and any CFI, DPE, ect. I've talked about this to since have not heard of it. That being that when you have an engine failure more than several thousand ft. with a non-full-feathering prop, that you should pitch up and decrease airspeed, sometimes to an intentional stall, to stop the rotation of the prop/engine. (Of course, only after you have attempted to restart.) The reason being that you will see a greater gain in glide distance by reducing the drag created by forcing thee air to turn over the engine. He claimed that while you would most likely be off of Vl/d for a short amount of time, thus not gliding in the most efficient manner, that is outweighed by the decrease in drag. (As I said, do this only with several thousand feet and plenty of time.) He claimed that in the case of something such as a 172, doing this procedure at, say 10,000ft, you would gain several more miles of glide distance.
So what I am asking for is if indeed a windmilling prop has more drag than a stopped prop and if so would it be beneficial to follow the advice in the pilot forum?
aerodynamics propeller engine-failure
$endgroup$
2
$begingroup$
I would be surprised if something like a 172 would windmill the prop at all, especially where the air is thinner at 10,000 feet. A lot of times engine failure means the engine locks up. Fuel starvation (more common) can let the prop spin, but there is a lot of force needed to spin a prop. I think a spinning prop is a lot more common on aircraft that don't have direct drive, like a turbo prop than it is for direct driven propellers.
$endgroup$
– Ron Beyer
May 16 at 20:25
1
$begingroup$
There are some situations such as model airplanes/ sailplanes with brushless electric motors where the answer is not cut-and-dried and depends on many variables.
$endgroup$
– quiet flyer
May 16 at 21:51
4
$begingroup$
Yes a Cessna 172 can definitely keep the prop windmilling. You have to slow to near stall speed to stop it. After that you can speed up and it won't windmill till you get going rather fast. I'm sure the drag is less with the prop stopped in that case.
$endgroup$
– quiet flyer
May 16 at 21:52
1
$begingroup$
Air density probably doesn't matter, if we are talking about the tendency of the prop to windmill at any given IAS.
$endgroup$
– quiet flyer
May 16 at 21:54
1
$begingroup$
Windmilling propeller can even have less drag: peter2000.co.uk/aviation/misc/prop.pdf
$endgroup$
– Erbureth
May 17 at 14:53
|
show 9 more comments
$begingroup$
For this question lets assume that we are talking about a fixed pitch propeller and not a variable pitch propeller. I do understand that variable pitch props should be feathered during an engine failure.
The main rationale for this question is this statement that I found in a pilot forum:
I've been doing some research on something I hard from my old chief CFI a couple years back, but I'm not finding much on it. He is the only person I've heard this from, and any CFI, DPE, ect. I've talked about this to since have not heard of it. That being that when you have an engine failure more than several thousand ft. with a non-full-feathering prop, that you should pitch up and decrease airspeed, sometimes to an intentional stall, to stop the rotation of the prop/engine. (Of course, only after you have attempted to restart.) The reason being that you will see a greater gain in glide distance by reducing the drag created by forcing thee air to turn over the engine. He claimed that while you would most likely be off of Vl/d for a short amount of time, thus not gliding in the most efficient manner, that is outweighed by the decrease in drag. (As I said, do this only with several thousand feet and plenty of time.) He claimed that in the case of something such as a 172, doing this procedure at, say 10,000ft, you would gain several more miles of glide distance.
So what I am asking for is if indeed a windmilling prop has more drag than a stopped prop and if so would it be beneficial to follow the advice in the pilot forum?
aerodynamics propeller engine-failure
$endgroup$
For this question lets assume that we are talking about a fixed pitch propeller and not a variable pitch propeller. I do understand that variable pitch props should be feathered during an engine failure.
The main rationale for this question is this statement that I found in a pilot forum:
I've been doing some research on something I hard from my old chief CFI a couple years back, but I'm not finding much on it. He is the only person I've heard this from, and any CFI, DPE, ect. I've talked about this to since have not heard of it. That being that when you have an engine failure more than several thousand ft. with a non-full-feathering prop, that you should pitch up and decrease airspeed, sometimes to an intentional stall, to stop the rotation of the prop/engine. (Of course, only after you have attempted to restart.) The reason being that you will see a greater gain in glide distance by reducing the drag created by forcing thee air to turn over the engine. He claimed that while you would most likely be off of Vl/d for a short amount of time, thus not gliding in the most efficient manner, that is outweighed by the decrease in drag. (As I said, do this only with several thousand feet and plenty of time.) He claimed that in the case of something such as a 172, doing this procedure at, say 10,000ft, you would gain several more miles of glide distance.
So what I am asking for is if indeed a windmilling prop has more drag than a stopped prop and if so would it be beneficial to follow the advice in the pilot forum?
aerodynamics propeller engine-failure
aerodynamics propeller engine-failure
edited May 18 at 2:09
Pondlife
53k10146303
53k10146303
asked May 16 at 20:14
DLHDLH
3,0661034
3,0661034
2
$begingroup$
I would be surprised if something like a 172 would windmill the prop at all, especially where the air is thinner at 10,000 feet. A lot of times engine failure means the engine locks up. Fuel starvation (more common) can let the prop spin, but there is a lot of force needed to spin a prop. I think a spinning prop is a lot more common on aircraft that don't have direct drive, like a turbo prop than it is for direct driven propellers.
$endgroup$
– Ron Beyer
May 16 at 20:25
1
$begingroup$
There are some situations such as model airplanes/ sailplanes with brushless electric motors where the answer is not cut-and-dried and depends on many variables.
$endgroup$
– quiet flyer
May 16 at 21:51
4
$begingroup$
Yes a Cessna 172 can definitely keep the prop windmilling. You have to slow to near stall speed to stop it. After that you can speed up and it won't windmill till you get going rather fast. I'm sure the drag is less with the prop stopped in that case.
$endgroup$
– quiet flyer
May 16 at 21:52
1
$begingroup$
Air density probably doesn't matter, if we are talking about the tendency of the prop to windmill at any given IAS.
$endgroup$
– quiet flyer
May 16 at 21:54
1
$begingroup$
Windmilling propeller can even have less drag: peter2000.co.uk/aviation/misc/prop.pdf
$endgroup$
– Erbureth
May 17 at 14:53
|
show 9 more comments
2
$begingroup$
I would be surprised if something like a 172 would windmill the prop at all, especially where the air is thinner at 10,000 feet. A lot of times engine failure means the engine locks up. Fuel starvation (more common) can let the prop spin, but there is a lot of force needed to spin a prop. I think a spinning prop is a lot more common on aircraft that don't have direct drive, like a turbo prop than it is for direct driven propellers.
$endgroup$
– Ron Beyer
May 16 at 20:25
1
$begingroup$
There are some situations such as model airplanes/ sailplanes with brushless electric motors where the answer is not cut-and-dried and depends on many variables.
$endgroup$
– quiet flyer
May 16 at 21:51
4
$begingroup$
Yes a Cessna 172 can definitely keep the prop windmilling. You have to slow to near stall speed to stop it. After that you can speed up and it won't windmill till you get going rather fast. I'm sure the drag is less with the prop stopped in that case.
$endgroup$
– quiet flyer
May 16 at 21:52
1
$begingroup$
Air density probably doesn't matter, if we are talking about the tendency of the prop to windmill at any given IAS.
$endgroup$
– quiet flyer
May 16 at 21:54
1
$begingroup$
Windmilling propeller can even have less drag: peter2000.co.uk/aviation/misc/prop.pdf
$endgroup$
– Erbureth
May 17 at 14:53
2
2
$begingroup$
I would be surprised if something like a 172 would windmill the prop at all, especially where the air is thinner at 10,000 feet. A lot of times engine failure means the engine locks up. Fuel starvation (more common) can let the prop spin, but there is a lot of force needed to spin a prop. I think a spinning prop is a lot more common on aircraft that don't have direct drive, like a turbo prop than it is for direct driven propellers.
$endgroup$
– Ron Beyer
May 16 at 20:25
$begingroup$
I would be surprised if something like a 172 would windmill the prop at all, especially where the air is thinner at 10,000 feet. A lot of times engine failure means the engine locks up. Fuel starvation (more common) can let the prop spin, but there is a lot of force needed to spin a prop. I think a spinning prop is a lot more common on aircraft that don't have direct drive, like a turbo prop than it is for direct driven propellers.
$endgroup$
– Ron Beyer
May 16 at 20:25
1
1
$begingroup$
There are some situations such as model airplanes/ sailplanes with brushless electric motors where the answer is not cut-and-dried and depends on many variables.
$endgroup$
– quiet flyer
May 16 at 21:51
$begingroup$
There are some situations such as model airplanes/ sailplanes with brushless electric motors where the answer is not cut-and-dried and depends on many variables.
$endgroup$
– quiet flyer
May 16 at 21:51
4
4
$begingroup$
Yes a Cessna 172 can definitely keep the prop windmilling. You have to slow to near stall speed to stop it. After that you can speed up and it won't windmill till you get going rather fast. I'm sure the drag is less with the prop stopped in that case.
$endgroup$
– quiet flyer
May 16 at 21:52
$begingroup$
Yes a Cessna 172 can definitely keep the prop windmilling. You have to slow to near stall speed to stop it. After that you can speed up and it won't windmill till you get going rather fast. I'm sure the drag is less with the prop stopped in that case.
$endgroup$
– quiet flyer
May 16 at 21:52
1
1
$begingroup$
Air density probably doesn't matter, if we are talking about the tendency of the prop to windmill at any given IAS.
$endgroup$
– quiet flyer
May 16 at 21:54
$begingroup$
Air density probably doesn't matter, if we are talking about the tendency of the prop to windmill at any given IAS.
$endgroup$
– quiet flyer
May 16 at 21:54
1
1
$begingroup$
Windmilling propeller can even have less drag: peter2000.co.uk/aviation/misc/prop.pdf
$endgroup$
– Erbureth
May 17 at 14:53
$begingroup$
Windmilling propeller can even have less drag: peter2000.co.uk/aviation/misc/prop.pdf
$endgroup$
– Erbureth
May 17 at 14:53
|
show 9 more comments
8 Answers
8
active
oldest
votes
$begingroup$
I would not follow the advice in the forum. While the reasoning that a windmilling prop does create more drag is sound, I have seen no empirical evidence that says how much it actually translates to in Feet Per Minute. The only studies I have seen have been inconclusive on the subject, and say there's a number of factors that you can't really control in that situation. The prop isn't that big compared to the airplane itself, so if a spinning one has 30% more drag (just a guess, as I said I've seen no actual numbers) it isn't going to make you plummet out of the sky.
What I would recommend is following the engine failure procedure in the POH of your particular aircraft. The advice to slow the airplane to try and get the prop to stop has a number of flaws:
- Distraction from critical tasks: Slowing the airplane until the prop stops is taking your focus away from finding a field to land in, ensuring your passengers are briefed and strapped in, making a mayday call and attempting to restart the engine. You'll be busy enough!
- Low airspeed danger: Slowing enough to stop the prop may require a very low airspeed, and you could have a stall/spin excursion, which is far more dangerous than a glide landing
- Drag curve: flying very slow to get the prop to stop will put you below best glide speed, which is where you get your best glide ratio. Below best glide speed you start to develop a high rate of descent, so by the time you get the prop stopped you have lost hundreds of extra feet. You could lose more altitude than you would potentially save, and waste valuable time doing it
- The chances are good that you couldn't change the prop behavior anyway: if your crankshaft has broken the prop's going to spin no matter what you do, if you've thrown a rod it's going to stop and you couldn't get it to windmill if you flew at mach 1
Doing some math puts this into perspective. Say an airplane's engine-out rate of descent with a spinning prop is 1000, and with a still prop it's 900 fpm. In a glide from 3000ft that buys you an extra 20 seconds, but it probably takes a lot more than 20 seconds to slow enough to stop the prop and then regain a stable airspeed.
Flying very slow to stop the prop is a potentially dangerous distraction, just set best glide speed and if the prop stops its a bonus.
$endgroup$
3
$begingroup$
"flying very slow to get the prop to stop will put you below best glide speed, which is where you get your best glide ratio. Below best glide speed you start to develop a high rate of descent" This is wrong. Minimum sink glide is normally significantly slower than best glide (by 20 knots or so). If you slow to stop the prop, you'll lose less altitude doing it, not more, unless you slow so much you stall. Obviously, don't stall.
$endgroup$
– fluffysheap
May 17 at 14:32
$begingroup$
I believe the answer also concern the glide distance you can get, not just rate of descend.
$endgroup$
– vasin1987
May 21 at 21:13
add a comment |
$begingroup$
The answer: it depends. Generally, a stopped propeller will be stalled, and so creating little drag. A windmilling propeller, conversely, usually will not be stalled, will be extracting energy from the airstream, and using that to turn the engine (which typically takes a moderate amount of energy), which will increase sink rate.
However, should you stop the propeller? That's a much harder question. Relevant questions are: how slow must you go to stop the propeller? Can you stop the propeller? If it requires dropping below minimum sink speed for an extended period, it is probably a bad idea, as sink increases rapidly with decreasing speed (you're on "the backside of the power curve" any time you're flying below minimum sink speed).
On some antique aircraft, it is or was reputed to be a requirement in some clubs that pilots be able to stop the engine and prop and restart the engine in flight before being granted pilot privileges for, say, the club Tiger Moth (these are generally hand-started). It is widely claimed that stopping the prop does extend the glide noticeably. The Tiger Moth also has a large, slow-turning wooden prop, and a fairly low stall speed.
As for whether I would try this in an emergency? Almost certainly not; if it's the POH, then sure... but I've never seen it in the POH of any single engine aircraft I've ever flown. And if I'm flying engine out, I've probably got worse things to worry about (unless I'm flying my more-usual gliders).
$endgroup$
$begingroup$
Welcome to Aviation.SE! A good first post. If you haven’t already done so, I’d recommend checking out the help center and taking our tour so you can see how the site works.
$endgroup$
– Notts90
May 17 at 9:17
add a comment |
$begingroup$
A windmilling propeller creates much more drag, by an order of magnitude at least. The obvious example is an autogyro or helicopter in autorotation, which drops like a stone if the rotor stopped.
Drag is a function of blade area for a stopped rotor and a function of disc area for a windmilling one. The difference is most pronounced for large rotors with few blades and almost nonexistent for turbofans. This answer gives some numbers:
If we compute the lift component per area of a vertically autorotating rotor, it is comparable to a coefficient of 1.1 to 1.2 referenced to the rotor area. According to this source, a flat plate has a drag coefficient of 1.28 and a parachute has one of 1.4. So in vertical descent, the auto-rotating rotor is almost as good as a parachute of the same area.
If you are high enough when the engine stops, it's a good idea to slow down a little so that the propeller stops windmilling. Once it has stopped, you can accelerate back to normal. The propeller will usually not start windmilling again, as it's drag, and thus available power, is now much lower.
$endgroup$
1
$begingroup$
Last time I looked at a propeller driven aircraft, the prop wasn't pointing vertically upwards. Also your assertion the windmill makes no difference to the drag of turbofans is plain wrong - a fan that is not freely windmilling has MUCH more drag, as has been demonstrated in real life when engine damage in flight locks up the rotors.
$endgroup$
– alephzero
May 16 at 22:51
3
$begingroup$
A helicopter in a vertical descent under autorotation is not much different from a propeller aircraft in horizontal flight with one engine inoperative. The rotor faces into the direction of travel and crates 'windmill drag'. The only difference is that the helicopter pilot tries to maximize drag in order to save his life. - @alephzero
$endgroup$
– Rainer P.
May 16 at 23:11
1
$begingroup$
An autogyro is a good analogy but I'm not sure the results are the same. The reason wind-milling blades cause more drag is because they're going faster. An autogyro has huge blades and very little other drag. An aircraft has much smaller blades and lots of induced drag from the wing. So while the drag from the prop may be an order of magnitude higher, the total drag will not be.
$endgroup$
– Robin Bennett
May 17 at 9:36
3
$begingroup$
-1: the claim of an order of magnitude difference, and the claim that drag is a function of the swept area for a windmilling prop, both sound extremely dubious (at least to me). I'd remove the downvote and stand corrected if some evidence or citations to back up the claims can be provided.
$endgroup$
– TypeIA
May 17 at 9:45
1
$begingroup$
@TypeIA The claim is correct. A quantification for helicopters in this answer
$endgroup$
– Koyovis
May 18 at 2:19
|
show 2 more comments
$begingroup$
The drag is significantly more for a windmilling propeller.
Both aerodynamic drag and energy lost in the engine contribute. I estimate you will sink at least 200 FPM faster if you let the prop windmill.
For aerodynamic drag, it's impossible to convert this into a feet per minute estimate because it varies so much with the design of the propeller and the overall drag of the airplane. But you can see here:
Aerodynamics for Naval Aviators, 1965
(page 149 in the page numbers, or 167 in the PDF) that the drag can increase significantly.
A typical fixed-pitch prop has a pitch of around 15 degrees (more details at bottom). A constant-speed prop which has lost oil pressure, and is not automatically feathering, is probably more like 5 degrees. (Feathering props are used on multi-engine planes to reduce drag if one engine fails. Non-feathering props are used on single-engine planes so if the pitch control fails but the engine still works, you don't lose all your power). Overall, the actual propeller parasitic (simple aerodynamic) drag increases by up to a factor of 3. Not orders of magnitude, but it's significant. Since there's no way for me to estimate how much of the total drag is due to the propeller, all I can say is that this is probably noticeable. However, if you have a cruise prop, or an adjustable prop set to high pitch, it's possible that it works out close to even, as above 22 degrees, the windmilling prop actually has less drag.
But then there's the extra factor of the drag created by the engine, which is probably much more significant. It's possible to come up with a reasonable ballpark figure. Estimation and highschool physics are required.
An airplane without power loses potential energy, in the form of altitude, to drag. Since the airplane's speed doesn't change, its kinetic energy doesn't either and only potential energy need be considered. We calculate how quickly energy is drained out of the airplane by the spinning engine.
Work is the amount of energy that is transferred from one place to another, and power is the amount of work over time. The formula for work (in a rotational system, such as an engine) is torque * theta, where theta is the total angular distance rotated. Power (watts) is expressed in joules per second, although here I'll figure power in joules/minute because our other time units are also in minutes. The joule, of course, is the unit of both work and energy.
Assume an airplane weighing 1000kg flying at 1500 meters AGL. Its potential energy is:
1000 kg * 1500 meters * 9.8 (gravity) = 14,700,000 J (14.7 mJ)
Assuming a propeller windmilling at 200 RPM, the angular velocity is:
2pi radians / revolution * 200 revolutions / minute = ~1260 radians / minute
I estimate the torque, given in newton-meters, is somewhere between 50 and 500 Nm, tending toward the high side. 50 is from my personal experience turning a propeller at slow speeds by hand, it's about that much force; but in the air I think this is extremely optimistic. 500 is a higher estimate, justified as follows.
Single-engine planes such as the Cessna 172 frequently have a 180HP engine. The propeller normally has enough air-grabbing ability to transfer that 180HP into the air at engine redline of ~2700 RPM.
Converting HP to joules / minute (1 watt = 1 joule/second):
180 HP * (746 watts / HP) * (60 seconds / minute) = 8057 kJ / minute
Assuming the propeller efficiency is relatively constant with RPM, you can convert propeller power delivery capability linearly with RPM:
8057 kJ / minute * (200 RPM / 2700 RPM) = 596 kJ / minute
So the propeller should be able to transfer about 600 kJ / minute back into the engine. This is in the ballpark of my estimate of 500. However, as not all the normal engine power goes into the propeller (due to mechanical losses and engine powered accessories) the estimate of 500 seems to be pretty close, and I'm sticking with it for sake of simpler math. This estimate is pretty seat of the pants - lots of error sources, like variations in propeller efficiency with RPM and being driven in reverse - are ignored. But if the propeller is less efficient, it dissipates more power - so even my high estimate might be too low.
Back to the engine failure. The power dissipated by the engine is therefore:
1260 * (50 to 500 or you pick) = 63 kJ to 630 kJ per minute
A Cessna 152 has a sink rate of 725 fpm when flying at best glide with stopped propeller (best glide speeds are normally specified with stopped prop); The Cessna 172 is closer to the mass I am using, and has similar glide performance, so I'll just use that same number. This is an estimated calculation, anyway. At 725 fpm descent rate (221 meters per minute) it normally takes 6.78 minutes to bleed off that 1500 meters of altitude you started with. Dividing potential energy by time:
14,700,000 / 6.78 = 2.168 MJ/min energy loss
At the low estimate (probably reasonable only for an engine that suffered total compression loss but no other damage), losing an additional 63 kJ/min only increases your sink rate by
(2.168 + .063) / 2.168 = 1.029
about 3%, or from 725 fpm to 746 fpm. You might not even notice this on the instruments, although if you snag on a power line at the last second as a result, you'll certainly notice that. However, at the high estimate, losing an additional 630 kJ/min would increase your sink rate by:
(2.168 + .630) / 2.168 = 1.29
29%, or from 725 fpm to 935 fpm. That's very significant. And this does not even include the extra aerodynamic drag from the spinning prop. It is only due to the energy lost in the engine.
So, in conclusion: If power fails, stop the prop.
There is, however, one final point. If you lost power because of a mechanical failure, it's very possible that the propeller will stop all on its own due to whatever damage caused the power loss. However, running out of fuel is the most common cause of in-flight power loss. If you run out of fuel, the prop will probably keep spinning unless you stop it yourself.
- Pitch angle in degrees is different from the way pitch is normally described, which is measured in inches, where something like 76"x60" would be typical. You can calculate pitch angle based on the propeller measurements in inches using the formula for helix angle. If you do, remember propeller pitch is specified at 75% of the diameter of the blade, rather than 100% as in the math textbooks).
$endgroup$
$begingroup$
Good work. A glider burns altitude as fuel to create kinetic energy. The wing uses this to more efficiently create lift. From a given altitude and mass, wing efficiency and drag determine how far you glide. The engine being turned does not affect the glide, the drag from the prop does. Not much difference there (the spinning one may even have a little less). But any loss in wing efficiency from prop turbulence will directly translate into loss of glide distance.
$endgroup$
– Robert DiGiovanni
May 17 at 22:15
add a comment |
$begingroup$
This paper provided by Erbureth provides empirical evidence to answer the question. The short answer is that sometimes a stopped propeller provided less drag and sometimes a windmilling one provided less drag. This actually makes a lot of sense to me as the drag should be related to the location of the stagnation pressure line on the prop.
A few observations from other answers:
- One of the things I always hear when this question is asked is that a rotating propeller turns into a disk and has more area. This is clearly wrong as the area of a propeller blade is always the same whether it is rotating or not.
- When a prop is feathered the prop stops windmilling and the drag is considerably less. This create the perception that the stopped propeller has much less drag but in reality it is due to the fact that the feathered prop has much less form drag. The fact that the prop is stopped is not the main reason.
$endgroup$
$begingroup$
It's worth noting that paper is on model airplanes and their wind tunnel tests are significantly below the normal flight speed. It's findings may still hold true, but I'd say to take it with a grain of salt.
$endgroup$
– TemporalWolf
May 17 at 17:26
$begingroup$
Work = force x distance, and a spinning prop goes much farther, so to speak, then a non-rotating one for the same velocity of aircraft. So while the blade area is the same, the spinning makes a big difference in the physics of the problem.
$endgroup$
– MikeY
May 18 at 12:22
$begingroup$
The clue is in the paper: they let the spinning prop freewheel without any resistance. An autorotating helicopter is still providing lift, and chopping away to push that air down.
$endgroup$
– Koyovis
May 21 at 8:09
$begingroup$
In other words: torque is the differentiator. Rotation * torque = energy extracted. No torque, no energy required.
$endgroup$
– Koyovis
May 26 at 20:03
add a comment |
$begingroup$
The argument that the windmilling prop is slowing the plane down by extracting energy to turn a dead engine ignores the fact that a frozen prop tries to turn the whole plane. The control inputs to keep the plane level are probably very close, and the turning airfoil may actually be slightly less draggy, so what is going on here?
It is well known that props are airfoils, and turbulence created by one blade affects the other.
In the windmilling case, the turbulence created by the propellor has a greater affect on that other airfoil, the wing.
This is mostly likely the major factor in loss of gliding distance. Important to realize the air that the plane is gliding through has no kinetic energy to extract, it's all in the kinetic and potential energy of the plane. But the windmilling prop does lower the efficiency of the wing in using the planes energy by creating more turbulence.
$endgroup$
1
$begingroup$
First sentence: it tries but doesn't succeed, so it's not doing any work on the plane.
$endgroup$
– hobbs
May 18 at 1:57
$begingroup$
It (unmoving) produces drag, a force on the plane. So does the moving one. WRT forces affecting the glide, that is what matters. Turning the engine is work by definition (net movement of engine from force) but the movement of the engine does not affect glide. The turbulence created by the rotating prop (which we COULD say is energy extracted from the glide forces) does.
$endgroup$
– Robert DiGiovanni
May 18 at 3:42
add a comment |
$begingroup$
I have tested this multiple times in a C152. Starting at 10,000 feet and cutting off the fuel to the engine -applying nose up to hold altitude as long as possible (thereby slowing my forward speed) until stopping the propeller. Then gliding with the propeller stopped for quite a distance, passing over multiple airports in the process. A windmilling propeller left me short by a significant distance.
I know I was weird in my younger days, but I was flying!
$endgroup$
$begingroup$
It is not completely clear to me which method the answerer is saying allowed the longer glide. This answer could benefit greatly from a little re-wording. I am reading it to say that the prop stopped resulted in the poorer glide ratio but I'm not sure that's what the answerer really meant to say.
$endgroup$
– quiet flyer
May 25 at 6:34
add a comment |
$begingroup$
A windmilling prop is allowing the slipstream to push it around. A stopped one is fighting the slipstream - pushing/deflecting it into a spiral. The reaction from that is what tries to turn the plane, as Robert DiGiovanni says. And it is doing work, because it's applying a force to the air, which moves as a result of it.
So I'd expect less drag from windmilling. Its like freewheeling on a bike versus having a locked-up wheel.
I'm assuming same AoA in both cases, i.e that stopped does not imply feathered. Some people appear to have assumed the opposite, to which I'm curious: how would you feather a fixed pitch prop, which is what is stated in OP.
$endgroup$
$begingroup$
Have removed the -1.
$endgroup$
– Koyovis
May 21 at 3:28
add a comment |
Your Answer
StackExchange.ready(function()
var channelOptions =
tags: "".split(" "),
id: "528"
;
initTagRenderer("".split(" "), "".split(" "), channelOptions);
StackExchange.using("externalEditor", function()
// Have to fire editor after snippets, if snippets enabled
if (StackExchange.settings.snippets.snippetsEnabled)
StackExchange.using("snippets", function()
createEditor();
);
else
createEditor();
);
function createEditor()
StackExchange.prepareEditor(
heartbeatType: 'answer',
autoActivateHeartbeat: false,
convertImagesToLinks: false,
noModals: true,
showLowRepImageUploadWarning: true,
reputationToPostImages: null,
bindNavPrevention: true,
postfix: "",
imageUploader:
brandingHtml: "Powered by u003ca class="icon-imgur-white" href="https://imgur.com/"u003eu003c/au003e",
contentPolicyHtml: "User contributions licensed under u003ca href="https://creativecommons.org/licenses/by-sa/3.0/"u003ecc by-sa 3.0 with attribution requiredu003c/au003e u003ca href="https://stackoverflow.com/legal/content-policy"u003e(content policy)u003c/au003e",
allowUrls: true
,
noCode: true, onDemand: true,
discardSelector: ".discard-answer"
,immediatelyShowMarkdownHelp:true
);
);
Sign up or log in
StackExchange.ready(function ()
StackExchange.helpers.onClickDraftSave('#login-link');
);
Sign up using Google
Sign up using Facebook
Sign up using Email and Password
Post as a guest
Required, but never shown
StackExchange.ready(
function ()
StackExchange.openid.initPostLogin('.new-post-login', 'https%3a%2f%2faviation.stackexchange.com%2fquestions%2f64394%2fdoes-a-windmilling-propeller-create-more-drag-than-a-stopped-propeller-in-an-eng%23new-answer', 'question_page');
);
Post as a guest
Required, but never shown
8 Answers
8
active
oldest
votes
8 Answers
8
active
oldest
votes
active
oldest
votes
active
oldest
votes
$begingroup$
I would not follow the advice in the forum. While the reasoning that a windmilling prop does create more drag is sound, I have seen no empirical evidence that says how much it actually translates to in Feet Per Minute. The only studies I have seen have been inconclusive on the subject, and say there's a number of factors that you can't really control in that situation. The prop isn't that big compared to the airplane itself, so if a spinning one has 30% more drag (just a guess, as I said I've seen no actual numbers) it isn't going to make you plummet out of the sky.
What I would recommend is following the engine failure procedure in the POH of your particular aircraft. The advice to slow the airplane to try and get the prop to stop has a number of flaws:
- Distraction from critical tasks: Slowing the airplane until the prop stops is taking your focus away from finding a field to land in, ensuring your passengers are briefed and strapped in, making a mayday call and attempting to restart the engine. You'll be busy enough!
- Low airspeed danger: Slowing enough to stop the prop may require a very low airspeed, and you could have a stall/spin excursion, which is far more dangerous than a glide landing
- Drag curve: flying very slow to get the prop to stop will put you below best glide speed, which is where you get your best glide ratio. Below best glide speed you start to develop a high rate of descent, so by the time you get the prop stopped you have lost hundreds of extra feet. You could lose more altitude than you would potentially save, and waste valuable time doing it
- The chances are good that you couldn't change the prop behavior anyway: if your crankshaft has broken the prop's going to spin no matter what you do, if you've thrown a rod it's going to stop and you couldn't get it to windmill if you flew at mach 1
Doing some math puts this into perspective. Say an airplane's engine-out rate of descent with a spinning prop is 1000, and with a still prop it's 900 fpm. In a glide from 3000ft that buys you an extra 20 seconds, but it probably takes a lot more than 20 seconds to slow enough to stop the prop and then regain a stable airspeed.
Flying very slow to stop the prop is a potentially dangerous distraction, just set best glide speed and if the prop stops its a bonus.
$endgroup$
3
$begingroup$
"flying very slow to get the prop to stop will put you below best glide speed, which is where you get your best glide ratio. Below best glide speed you start to develop a high rate of descent" This is wrong. Minimum sink glide is normally significantly slower than best glide (by 20 knots or so). If you slow to stop the prop, you'll lose less altitude doing it, not more, unless you slow so much you stall. Obviously, don't stall.
$endgroup$
– fluffysheap
May 17 at 14:32
$begingroup$
I believe the answer also concern the glide distance you can get, not just rate of descend.
$endgroup$
– vasin1987
May 21 at 21:13
add a comment |
$begingroup$
I would not follow the advice in the forum. While the reasoning that a windmilling prop does create more drag is sound, I have seen no empirical evidence that says how much it actually translates to in Feet Per Minute. The only studies I have seen have been inconclusive on the subject, and say there's a number of factors that you can't really control in that situation. The prop isn't that big compared to the airplane itself, so if a spinning one has 30% more drag (just a guess, as I said I've seen no actual numbers) it isn't going to make you plummet out of the sky.
What I would recommend is following the engine failure procedure in the POH of your particular aircraft. The advice to slow the airplane to try and get the prop to stop has a number of flaws:
- Distraction from critical tasks: Slowing the airplane until the prop stops is taking your focus away from finding a field to land in, ensuring your passengers are briefed and strapped in, making a mayday call and attempting to restart the engine. You'll be busy enough!
- Low airspeed danger: Slowing enough to stop the prop may require a very low airspeed, and you could have a stall/spin excursion, which is far more dangerous than a glide landing
- Drag curve: flying very slow to get the prop to stop will put you below best glide speed, which is where you get your best glide ratio. Below best glide speed you start to develop a high rate of descent, so by the time you get the prop stopped you have lost hundreds of extra feet. You could lose more altitude than you would potentially save, and waste valuable time doing it
- The chances are good that you couldn't change the prop behavior anyway: if your crankshaft has broken the prop's going to spin no matter what you do, if you've thrown a rod it's going to stop and you couldn't get it to windmill if you flew at mach 1
Doing some math puts this into perspective. Say an airplane's engine-out rate of descent with a spinning prop is 1000, and with a still prop it's 900 fpm. In a glide from 3000ft that buys you an extra 20 seconds, but it probably takes a lot more than 20 seconds to slow enough to stop the prop and then regain a stable airspeed.
Flying very slow to stop the prop is a potentially dangerous distraction, just set best glide speed and if the prop stops its a bonus.
$endgroup$
3
$begingroup$
"flying very slow to get the prop to stop will put you below best glide speed, which is where you get your best glide ratio. Below best glide speed you start to develop a high rate of descent" This is wrong. Minimum sink glide is normally significantly slower than best glide (by 20 knots or so). If you slow to stop the prop, you'll lose less altitude doing it, not more, unless you slow so much you stall. Obviously, don't stall.
$endgroup$
– fluffysheap
May 17 at 14:32
$begingroup$
I believe the answer also concern the glide distance you can get, not just rate of descend.
$endgroup$
– vasin1987
May 21 at 21:13
add a comment |
$begingroup$
I would not follow the advice in the forum. While the reasoning that a windmilling prop does create more drag is sound, I have seen no empirical evidence that says how much it actually translates to in Feet Per Minute. The only studies I have seen have been inconclusive on the subject, and say there's a number of factors that you can't really control in that situation. The prop isn't that big compared to the airplane itself, so if a spinning one has 30% more drag (just a guess, as I said I've seen no actual numbers) it isn't going to make you plummet out of the sky.
What I would recommend is following the engine failure procedure in the POH of your particular aircraft. The advice to slow the airplane to try and get the prop to stop has a number of flaws:
- Distraction from critical tasks: Slowing the airplane until the prop stops is taking your focus away from finding a field to land in, ensuring your passengers are briefed and strapped in, making a mayday call and attempting to restart the engine. You'll be busy enough!
- Low airspeed danger: Slowing enough to stop the prop may require a very low airspeed, and you could have a stall/spin excursion, which is far more dangerous than a glide landing
- Drag curve: flying very slow to get the prop to stop will put you below best glide speed, which is where you get your best glide ratio. Below best glide speed you start to develop a high rate of descent, so by the time you get the prop stopped you have lost hundreds of extra feet. You could lose more altitude than you would potentially save, and waste valuable time doing it
- The chances are good that you couldn't change the prop behavior anyway: if your crankshaft has broken the prop's going to spin no matter what you do, if you've thrown a rod it's going to stop and you couldn't get it to windmill if you flew at mach 1
Doing some math puts this into perspective. Say an airplane's engine-out rate of descent with a spinning prop is 1000, and with a still prop it's 900 fpm. In a glide from 3000ft that buys you an extra 20 seconds, but it probably takes a lot more than 20 seconds to slow enough to stop the prop and then regain a stable airspeed.
Flying very slow to stop the prop is a potentially dangerous distraction, just set best glide speed and if the prop stops its a bonus.
$endgroup$
I would not follow the advice in the forum. While the reasoning that a windmilling prop does create more drag is sound, I have seen no empirical evidence that says how much it actually translates to in Feet Per Minute. The only studies I have seen have been inconclusive on the subject, and say there's a number of factors that you can't really control in that situation. The prop isn't that big compared to the airplane itself, so if a spinning one has 30% more drag (just a guess, as I said I've seen no actual numbers) it isn't going to make you plummet out of the sky.
What I would recommend is following the engine failure procedure in the POH of your particular aircraft. The advice to slow the airplane to try and get the prop to stop has a number of flaws:
- Distraction from critical tasks: Slowing the airplane until the prop stops is taking your focus away from finding a field to land in, ensuring your passengers are briefed and strapped in, making a mayday call and attempting to restart the engine. You'll be busy enough!
- Low airspeed danger: Slowing enough to stop the prop may require a very low airspeed, and you could have a stall/spin excursion, which is far more dangerous than a glide landing
- Drag curve: flying very slow to get the prop to stop will put you below best glide speed, which is where you get your best glide ratio. Below best glide speed you start to develop a high rate of descent, so by the time you get the prop stopped you have lost hundreds of extra feet. You could lose more altitude than you would potentially save, and waste valuable time doing it
- The chances are good that you couldn't change the prop behavior anyway: if your crankshaft has broken the prop's going to spin no matter what you do, if you've thrown a rod it's going to stop and you couldn't get it to windmill if you flew at mach 1
Doing some math puts this into perspective. Say an airplane's engine-out rate of descent with a spinning prop is 1000, and with a still prop it's 900 fpm. In a glide from 3000ft that buys you an extra 20 seconds, but it probably takes a lot more than 20 seconds to slow enough to stop the prop and then regain a stable airspeed.
Flying very slow to stop the prop is a potentially dangerous distraction, just set best glide speed and if the prop stops its a bonus.
edited May 17 at 8:56
answered May 16 at 21:04
GdDGdD
33.9k393142
33.9k393142
3
$begingroup$
"flying very slow to get the prop to stop will put you below best glide speed, which is where you get your best glide ratio. Below best glide speed you start to develop a high rate of descent" This is wrong. Minimum sink glide is normally significantly slower than best glide (by 20 knots or so). If you slow to stop the prop, you'll lose less altitude doing it, not more, unless you slow so much you stall. Obviously, don't stall.
$endgroup$
– fluffysheap
May 17 at 14:32
$begingroup$
I believe the answer also concern the glide distance you can get, not just rate of descend.
$endgroup$
– vasin1987
May 21 at 21:13
add a comment |
3
$begingroup$
"flying very slow to get the prop to stop will put you below best glide speed, which is where you get your best glide ratio. Below best glide speed you start to develop a high rate of descent" This is wrong. Minimum sink glide is normally significantly slower than best glide (by 20 knots or so). If you slow to stop the prop, you'll lose less altitude doing it, not more, unless you slow so much you stall. Obviously, don't stall.
$endgroup$
– fluffysheap
May 17 at 14:32
$begingroup$
I believe the answer also concern the glide distance you can get, not just rate of descend.
$endgroup$
– vasin1987
May 21 at 21:13
3
3
$begingroup$
"flying very slow to get the prop to stop will put you below best glide speed, which is where you get your best glide ratio. Below best glide speed you start to develop a high rate of descent" This is wrong. Minimum sink glide is normally significantly slower than best glide (by 20 knots or so). If you slow to stop the prop, you'll lose less altitude doing it, not more, unless you slow so much you stall. Obviously, don't stall.
$endgroup$
– fluffysheap
May 17 at 14:32
$begingroup$
"flying very slow to get the prop to stop will put you below best glide speed, which is where you get your best glide ratio. Below best glide speed you start to develop a high rate of descent" This is wrong. Minimum sink glide is normally significantly slower than best glide (by 20 knots or so). If you slow to stop the prop, you'll lose less altitude doing it, not more, unless you slow so much you stall. Obviously, don't stall.
$endgroup$
– fluffysheap
May 17 at 14:32
$begingroup$
I believe the answer also concern the glide distance you can get, not just rate of descend.
$endgroup$
– vasin1987
May 21 at 21:13
$begingroup$
I believe the answer also concern the glide distance you can get, not just rate of descend.
$endgroup$
– vasin1987
May 21 at 21:13
add a comment |
$begingroup$
The answer: it depends. Generally, a stopped propeller will be stalled, and so creating little drag. A windmilling propeller, conversely, usually will not be stalled, will be extracting energy from the airstream, and using that to turn the engine (which typically takes a moderate amount of energy), which will increase sink rate.
However, should you stop the propeller? That's a much harder question. Relevant questions are: how slow must you go to stop the propeller? Can you stop the propeller? If it requires dropping below minimum sink speed for an extended period, it is probably a bad idea, as sink increases rapidly with decreasing speed (you're on "the backside of the power curve" any time you're flying below minimum sink speed).
On some antique aircraft, it is or was reputed to be a requirement in some clubs that pilots be able to stop the engine and prop and restart the engine in flight before being granted pilot privileges for, say, the club Tiger Moth (these are generally hand-started). It is widely claimed that stopping the prop does extend the glide noticeably. The Tiger Moth also has a large, slow-turning wooden prop, and a fairly low stall speed.
As for whether I would try this in an emergency? Almost certainly not; if it's the POH, then sure... but I've never seen it in the POH of any single engine aircraft I've ever flown. And if I'm flying engine out, I've probably got worse things to worry about (unless I'm flying my more-usual gliders).
$endgroup$
$begingroup$
Welcome to Aviation.SE! A good first post. If you haven’t already done so, I’d recommend checking out the help center and taking our tour so you can see how the site works.
$endgroup$
– Notts90
May 17 at 9:17
add a comment |
$begingroup$
The answer: it depends. Generally, a stopped propeller will be stalled, and so creating little drag. A windmilling propeller, conversely, usually will not be stalled, will be extracting energy from the airstream, and using that to turn the engine (which typically takes a moderate amount of energy), which will increase sink rate.
However, should you stop the propeller? That's a much harder question. Relevant questions are: how slow must you go to stop the propeller? Can you stop the propeller? If it requires dropping below minimum sink speed for an extended period, it is probably a bad idea, as sink increases rapidly with decreasing speed (you're on "the backside of the power curve" any time you're flying below minimum sink speed).
On some antique aircraft, it is or was reputed to be a requirement in some clubs that pilots be able to stop the engine and prop and restart the engine in flight before being granted pilot privileges for, say, the club Tiger Moth (these are generally hand-started). It is widely claimed that stopping the prop does extend the glide noticeably. The Tiger Moth also has a large, slow-turning wooden prop, and a fairly low stall speed.
As for whether I would try this in an emergency? Almost certainly not; if it's the POH, then sure... but I've never seen it in the POH of any single engine aircraft I've ever flown. And if I'm flying engine out, I've probably got worse things to worry about (unless I'm flying my more-usual gliders).
$endgroup$
$begingroup$
Welcome to Aviation.SE! A good first post. If you haven’t already done so, I’d recommend checking out the help center and taking our tour so you can see how the site works.
$endgroup$
– Notts90
May 17 at 9:17
add a comment |
$begingroup$
The answer: it depends. Generally, a stopped propeller will be stalled, and so creating little drag. A windmilling propeller, conversely, usually will not be stalled, will be extracting energy from the airstream, and using that to turn the engine (which typically takes a moderate amount of energy), which will increase sink rate.
However, should you stop the propeller? That's a much harder question. Relevant questions are: how slow must you go to stop the propeller? Can you stop the propeller? If it requires dropping below minimum sink speed for an extended period, it is probably a bad idea, as sink increases rapidly with decreasing speed (you're on "the backside of the power curve" any time you're flying below minimum sink speed).
On some antique aircraft, it is or was reputed to be a requirement in some clubs that pilots be able to stop the engine and prop and restart the engine in flight before being granted pilot privileges for, say, the club Tiger Moth (these are generally hand-started). It is widely claimed that stopping the prop does extend the glide noticeably. The Tiger Moth also has a large, slow-turning wooden prop, and a fairly low stall speed.
As for whether I would try this in an emergency? Almost certainly not; if it's the POH, then sure... but I've never seen it in the POH of any single engine aircraft I've ever flown. And if I'm flying engine out, I've probably got worse things to worry about (unless I'm flying my more-usual gliders).
$endgroup$
The answer: it depends. Generally, a stopped propeller will be stalled, and so creating little drag. A windmilling propeller, conversely, usually will not be stalled, will be extracting energy from the airstream, and using that to turn the engine (which typically takes a moderate amount of energy), which will increase sink rate.
However, should you stop the propeller? That's a much harder question. Relevant questions are: how slow must you go to stop the propeller? Can you stop the propeller? If it requires dropping below minimum sink speed for an extended period, it is probably a bad idea, as sink increases rapidly with decreasing speed (you're on "the backside of the power curve" any time you're flying below minimum sink speed).
On some antique aircraft, it is or was reputed to be a requirement in some clubs that pilots be able to stop the engine and prop and restart the engine in flight before being granted pilot privileges for, say, the club Tiger Moth (these are generally hand-started). It is widely claimed that stopping the prop does extend the glide noticeably. The Tiger Moth also has a large, slow-turning wooden prop, and a fairly low stall speed.
As for whether I would try this in an emergency? Almost certainly not; if it's the POH, then sure... but I've never seen it in the POH of any single engine aircraft I've ever flown. And if I'm flying engine out, I've probably got worse things to worry about (unless I'm flying my more-usual gliders).
answered May 17 at 4:11
eyesoarseyesoars
1612
1612
$begingroup$
Welcome to Aviation.SE! A good first post. If you haven’t already done so, I’d recommend checking out the help center and taking our tour so you can see how the site works.
$endgroup$
– Notts90
May 17 at 9:17
add a comment |
$begingroup$
Welcome to Aviation.SE! A good first post. If you haven’t already done so, I’d recommend checking out the help center and taking our tour so you can see how the site works.
$endgroup$
– Notts90
May 17 at 9:17
$begingroup$
Welcome to Aviation.SE! A good first post. If you haven’t already done so, I’d recommend checking out the help center and taking our tour so you can see how the site works.
$endgroup$
– Notts90
May 17 at 9:17
$begingroup$
Welcome to Aviation.SE! A good first post. If you haven’t already done so, I’d recommend checking out the help center and taking our tour so you can see how the site works.
$endgroup$
– Notts90
May 17 at 9:17
add a comment |
$begingroup$
A windmilling propeller creates much more drag, by an order of magnitude at least. The obvious example is an autogyro or helicopter in autorotation, which drops like a stone if the rotor stopped.
Drag is a function of blade area for a stopped rotor and a function of disc area for a windmilling one. The difference is most pronounced for large rotors with few blades and almost nonexistent for turbofans. This answer gives some numbers:
If we compute the lift component per area of a vertically autorotating rotor, it is comparable to a coefficient of 1.1 to 1.2 referenced to the rotor area. According to this source, a flat plate has a drag coefficient of 1.28 and a parachute has one of 1.4. So in vertical descent, the auto-rotating rotor is almost as good as a parachute of the same area.
If you are high enough when the engine stops, it's a good idea to slow down a little so that the propeller stops windmilling. Once it has stopped, you can accelerate back to normal. The propeller will usually not start windmilling again, as it's drag, and thus available power, is now much lower.
$endgroup$
1
$begingroup$
Last time I looked at a propeller driven aircraft, the prop wasn't pointing vertically upwards. Also your assertion the windmill makes no difference to the drag of turbofans is plain wrong - a fan that is not freely windmilling has MUCH more drag, as has been demonstrated in real life when engine damage in flight locks up the rotors.
$endgroup$
– alephzero
May 16 at 22:51
3
$begingroup$
A helicopter in a vertical descent under autorotation is not much different from a propeller aircraft in horizontal flight with one engine inoperative. The rotor faces into the direction of travel and crates 'windmill drag'. The only difference is that the helicopter pilot tries to maximize drag in order to save his life. - @alephzero
$endgroup$
– Rainer P.
May 16 at 23:11
1
$begingroup$
An autogyro is a good analogy but I'm not sure the results are the same. The reason wind-milling blades cause more drag is because they're going faster. An autogyro has huge blades and very little other drag. An aircraft has much smaller blades and lots of induced drag from the wing. So while the drag from the prop may be an order of magnitude higher, the total drag will not be.
$endgroup$
– Robin Bennett
May 17 at 9:36
3
$begingroup$
-1: the claim of an order of magnitude difference, and the claim that drag is a function of the swept area for a windmilling prop, both sound extremely dubious (at least to me). I'd remove the downvote and stand corrected if some evidence or citations to back up the claims can be provided.
$endgroup$
– TypeIA
May 17 at 9:45
1
$begingroup$
@TypeIA The claim is correct. A quantification for helicopters in this answer
$endgroup$
– Koyovis
May 18 at 2:19
|
show 2 more comments
$begingroup$
A windmilling propeller creates much more drag, by an order of magnitude at least. The obvious example is an autogyro or helicopter in autorotation, which drops like a stone if the rotor stopped.
Drag is a function of blade area for a stopped rotor and a function of disc area for a windmilling one. The difference is most pronounced for large rotors with few blades and almost nonexistent for turbofans. This answer gives some numbers:
If we compute the lift component per area of a vertically autorotating rotor, it is comparable to a coefficient of 1.1 to 1.2 referenced to the rotor area. According to this source, a flat plate has a drag coefficient of 1.28 and a parachute has one of 1.4. So in vertical descent, the auto-rotating rotor is almost as good as a parachute of the same area.
If you are high enough when the engine stops, it's a good idea to slow down a little so that the propeller stops windmilling. Once it has stopped, you can accelerate back to normal. The propeller will usually not start windmilling again, as it's drag, and thus available power, is now much lower.
$endgroup$
1
$begingroup$
Last time I looked at a propeller driven aircraft, the prop wasn't pointing vertically upwards. Also your assertion the windmill makes no difference to the drag of turbofans is plain wrong - a fan that is not freely windmilling has MUCH more drag, as has been demonstrated in real life when engine damage in flight locks up the rotors.
$endgroup$
– alephzero
May 16 at 22:51
3
$begingroup$
A helicopter in a vertical descent under autorotation is not much different from a propeller aircraft in horizontal flight with one engine inoperative. The rotor faces into the direction of travel and crates 'windmill drag'. The only difference is that the helicopter pilot tries to maximize drag in order to save his life. - @alephzero
$endgroup$
– Rainer P.
May 16 at 23:11
1
$begingroup$
An autogyro is a good analogy but I'm not sure the results are the same. The reason wind-milling blades cause more drag is because they're going faster. An autogyro has huge blades and very little other drag. An aircraft has much smaller blades and lots of induced drag from the wing. So while the drag from the prop may be an order of magnitude higher, the total drag will not be.
$endgroup$
– Robin Bennett
May 17 at 9:36
3
$begingroup$
-1: the claim of an order of magnitude difference, and the claim that drag is a function of the swept area for a windmilling prop, both sound extremely dubious (at least to me). I'd remove the downvote and stand corrected if some evidence or citations to back up the claims can be provided.
$endgroup$
– TypeIA
May 17 at 9:45
1
$begingroup$
@TypeIA The claim is correct. A quantification for helicopters in this answer
$endgroup$
– Koyovis
May 18 at 2:19
|
show 2 more comments
$begingroup$
A windmilling propeller creates much more drag, by an order of magnitude at least. The obvious example is an autogyro or helicopter in autorotation, which drops like a stone if the rotor stopped.
Drag is a function of blade area for a stopped rotor and a function of disc area for a windmilling one. The difference is most pronounced for large rotors with few blades and almost nonexistent for turbofans. This answer gives some numbers:
If we compute the lift component per area of a vertically autorotating rotor, it is comparable to a coefficient of 1.1 to 1.2 referenced to the rotor area. According to this source, a flat plate has a drag coefficient of 1.28 and a parachute has one of 1.4. So in vertical descent, the auto-rotating rotor is almost as good as a parachute of the same area.
If you are high enough when the engine stops, it's a good idea to slow down a little so that the propeller stops windmilling. Once it has stopped, you can accelerate back to normal. The propeller will usually not start windmilling again, as it's drag, and thus available power, is now much lower.
$endgroup$
A windmilling propeller creates much more drag, by an order of magnitude at least. The obvious example is an autogyro or helicopter in autorotation, which drops like a stone if the rotor stopped.
Drag is a function of blade area for a stopped rotor and a function of disc area for a windmilling one. The difference is most pronounced for large rotors with few blades and almost nonexistent for turbofans. This answer gives some numbers:
If we compute the lift component per area of a vertically autorotating rotor, it is comparable to a coefficient of 1.1 to 1.2 referenced to the rotor area. According to this source, a flat plate has a drag coefficient of 1.28 and a parachute has one of 1.4. So in vertical descent, the auto-rotating rotor is almost as good as a parachute of the same area.
If you are high enough when the engine stops, it's a good idea to slow down a little so that the propeller stops windmilling. Once it has stopped, you can accelerate back to normal. The propeller will usually not start windmilling again, as it's drag, and thus available power, is now much lower.
edited May 18 at 10:22
answered May 16 at 20:58
Rainer P.Rainer P.
1,14039
1,14039
1
$begingroup$
Last time I looked at a propeller driven aircraft, the prop wasn't pointing vertically upwards. Also your assertion the windmill makes no difference to the drag of turbofans is plain wrong - a fan that is not freely windmilling has MUCH more drag, as has been demonstrated in real life when engine damage in flight locks up the rotors.
$endgroup$
– alephzero
May 16 at 22:51
3
$begingroup$
A helicopter in a vertical descent under autorotation is not much different from a propeller aircraft in horizontal flight with one engine inoperative. The rotor faces into the direction of travel and crates 'windmill drag'. The only difference is that the helicopter pilot tries to maximize drag in order to save his life. - @alephzero
$endgroup$
– Rainer P.
May 16 at 23:11
1
$begingroup$
An autogyro is a good analogy but I'm not sure the results are the same. The reason wind-milling blades cause more drag is because they're going faster. An autogyro has huge blades and very little other drag. An aircraft has much smaller blades and lots of induced drag from the wing. So while the drag from the prop may be an order of magnitude higher, the total drag will not be.
$endgroup$
– Robin Bennett
May 17 at 9:36
3
$begingroup$
-1: the claim of an order of magnitude difference, and the claim that drag is a function of the swept area for a windmilling prop, both sound extremely dubious (at least to me). I'd remove the downvote and stand corrected if some evidence or citations to back up the claims can be provided.
$endgroup$
– TypeIA
May 17 at 9:45
1
$begingroup$
@TypeIA The claim is correct. A quantification for helicopters in this answer
$endgroup$
– Koyovis
May 18 at 2:19
|
show 2 more comments
1
$begingroup$
Last time I looked at a propeller driven aircraft, the prop wasn't pointing vertically upwards. Also your assertion the windmill makes no difference to the drag of turbofans is plain wrong - a fan that is not freely windmilling has MUCH more drag, as has been demonstrated in real life when engine damage in flight locks up the rotors.
$endgroup$
– alephzero
May 16 at 22:51
3
$begingroup$
A helicopter in a vertical descent under autorotation is not much different from a propeller aircraft in horizontal flight with one engine inoperative. The rotor faces into the direction of travel and crates 'windmill drag'. The only difference is that the helicopter pilot tries to maximize drag in order to save his life. - @alephzero
$endgroup$
– Rainer P.
May 16 at 23:11
1
$begingroup$
An autogyro is a good analogy but I'm not sure the results are the same. The reason wind-milling blades cause more drag is because they're going faster. An autogyro has huge blades and very little other drag. An aircraft has much smaller blades and lots of induced drag from the wing. So while the drag from the prop may be an order of magnitude higher, the total drag will not be.
$endgroup$
– Robin Bennett
May 17 at 9:36
3
$begingroup$
-1: the claim of an order of magnitude difference, and the claim that drag is a function of the swept area for a windmilling prop, both sound extremely dubious (at least to me). I'd remove the downvote and stand corrected if some evidence or citations to back up the claims can be provided.
$endgroup$
– TypeIA
May 17 at 9:45
1
$begingroup$
@TypeIA The claim is correct. A quantification for helicopters in this answer
$endgroup$
– Koyovis
May 18 at 2:19
1
1
$begingroup$
Last time I looked at a propeller driven aircraft, the prop wasn't pointing vertically upwards. Also your assertion the windmill makes no difference to the drag of turbofans is plain wrong - a fan that is not freely windmilling has MUCH more drag, as has been demonstrated in real life when engine damage in flight locks up the rotors.
$endgroup$
– alephzero
May 16 at 22:51
$begingroup$
Last time I looked at a propeller driven aircraft, the prop wasn't pointing vertically upwards. Also your assertion the windmill makes no difference to the drag of turbofans is plain wrong - a fan that is not freely windmilling has MUCH more drag, as has been demonstrated in real life when engine damage in flight locks up the rotors.
$endgroup$
– alephzero
May 16 at 22:51
3
3
$begingroup$
A helicopter in a vertical descent under autorotation is not much different from a propeller aircraft in horizontal flight with one engine inoperative. The rotor faces into the direction of travel and crates 'windmill drag'. The only difference is that the helicopter pilot tries to maximize drag in order to save his life. - @alephzero
$endgroup$
– Rainer P.
May 16 at 23:11
$begingroup$
A helicopter in a vertical descent under autorotation is not much different from a propeller aircraft in horizontal flight with one engine inoperative. The rotor faces into the direction of travel and crates 'windmill drag'. The only difference is that the helicopter pilot tries to maximize drag in order to save his life. - @alephzero
$endgroup$
– Rainer P.
May 16 at 23:11
1
1
$begingroup$
An autogyro is a good analogy but I'm not sure the results are the same. The reason wind-milling blades cause more drag is because they're going faster. An autogyro has huge blades and very little other drag. An aircraft has much smaller blades and lots of induced drag from the wing. So while the drag from the prop may be an order of magnitude higher, the total drag will not be.
$endgroup$
– Robin Bennett
May 17 at 9:36
$begingroup$
An autogyro is a good analogy but I'm not sure the results are the same. The reason wind-milling blades cause more drag is because they're going faster. An autogyro has huge blades and very little other drag. An aircraft has much smaller blades and lots of induced drag from the wing. So while the drag from the prop may be an order of magnitude higher, the total drag will not be.
$endgroup$
– Robin Bennett
May 17 at 9:36
3
3
$begingroup$
-1: the claim of an order of magnitude difference, and the claim that drag is a function of the swept area for a windmilling prop, both sound extremely dubious (at least to me). I'd remove the downvote and stand corrected if some evidence or citations to back up the claims can be provided.
$endgroup$
– TypeIA
May 17 at 9:45
$begingroup$
-1: the claim of an order of magnitude difference, and the claim that drag is a function of the swept area for a windmilling prop, both sound extremely dubious (at least to me). I'd remove the downvote and stand corrected if some evidence or citations to back up the claims can be provided.
$endgroup$
– TypeIA
May 17 at 9:45
1
1
$begingroup$
@TypeIA The claim is correct. A quantification for helicopters in this answer
$endgroup$
– Koyovis
May 18 at 2:19
$begingroup$
@TypeIA The claim is correct. A quantification for helicopters in this answer
$endgroup$
– Koyovis
May 18 at 2:19
|
show 2 more comments
$begingroup$
The drag is significantly more for a windmilling propeller.
Both aerodynamic drag and energy lost in the engine contribute. I estimate you will sink at least 200 FPM faster if you let the prop windmill.
For aerodynamic drag, it's impossible to convert this into a feet per minute estimate because it varies so much with the design of the propeller and the overall drag of the airplane. But you can see here:
Aerodynamics for Naval Aviators, 1965
(page 149 in the page numbers, or 167 in the PDF) that the drag can increase significantly.
A typical fixed-pitch prop has a pitch of around 15 degrees (more details at bottom). A constant-speed prop which has lost oil pressure, and is not automatically feathering, is probably more like 5 degrees. (Feathering props are used on multi-engine planes to reduce drag if one engine fails. Non-feathering props are used on single-engine planes so if the pitch control fails but the engine still works, you don't lose all your power). Overall, the actual propeller parasitic (simple aerodynamic) drag increases by up to a factor of 3. Not orders of magnitude, but it's significant. Since there's no way for me to estimate how much of the total drag is due to the propeller, all I can say is that this is probably noticeable. However, if you have a cruise prop, or an adjustable prop set to high pitch, it's possible that it works out close to even, as above 22 degrees, the windmilling prop actually has less drag.
But then there's the extra factor of the drag created by the engine, which is probably much more significant. It's possible to come up with a reasonable ballpark figure. Estimation and highschool physics are required.
An airplane without power loses potential energy, in the form of altitude, to drag. Since the airplane's speed doesn't change, its kinetic energy doesn't either and only potential energy need be considered. We calculate how quickly energy is drained out of the airplane by the spinning engine.
Work is the amount of energy that is transferred from one place to another, and power is the amount of work over time. The formula for work (in a rotational system, such as an engine) is torque * theta, where theta is the total angular distance rotated. Power (watts) is expressed in joules per second, although here I'll figure power in joules/minute because our other time units are also in minutes. The joule, of course, is the unit of both work and energy.
Assume an airplane weighing 1000kg flying at 1500 meters AGL. Its potential energy is:
1000 kg * 1500 meters * 9.8 (gravity) = 14,700,000 J (14.7 mJ)
Assuming a propeller windmilling at 200 RPM, the angular velocity is:
2pi radians / revolution * 200 revolutions / minute = ~1260 radians / minute
I estimate the torque, given in newton-meters, is somewhere between 50 and 500 Nm, tending toward the high side. 50 is from my personal experience turning a propeller at slow speeds by hand, it's about that much force; but in the air I think this is extremely optimistic. 500 is a higher estimate, justified as follows.
Single-engine planes such as the Cessna 172 frequently have a 180HP engine. The propeller normally has enough air-grabbing ability to transfer that 180HP into the air at engine redline of ~2700 RPM.
Converting HP to joules / minute (1 watt = 1 joule/second):
180 HP * (746 watts / HP) * (60 seconds / minute) = 8057 kJ / minute
Assuming the propeller efficiency is relatively constant with RPM, you can convert propeller power delivery capability linearly with RPM:
8057 kJ / minute * (200 RPM / 2700 RPM) = 596 kJ / minute
So the propeller should be able to transfer about 600 kJ / minute back into the engine. This is in the ballpark of my estimate of 500. However, as not all the normal engine power goes into the propeller (due to mechanical losses and engine powered accessories) the estimate of 500 seems to be pretty close, and I'm sticking with it for sake of simpler math. This estimate is pretty seat of the pants - lots of error sources, like variations in propeller efficiency with RPM and being driven in reverse - are ignored. But if the propeller is less efficient, it dissipates more power - so even my high estimate might be too low.
Back to the engine failure. The power dissipated by the engine is therefore:
1260 * (50 to 500 or you pick) = 63 kJ to 630 kJ per minute
A Cessna 152 has a sink rate of 725 fpm when flying at best glide with stopped propeller (best glide speeds are normally specified with stopped prop); The Cessna 172 is closer to the mass I am using, and has similar glide performance, so I'll just use that same number. This is an estimated calculation, anyway. At 725 fpm descent rate (221 meters per minute) it normally takes 6.78 minutes to bleed off that 1500 meters of altitude you started with. Dividing potential energy by time:
14,700,000 / 6.78 = 2.168 MJ/min energy loss
At the low estimate (probably reasonable only for an engine that suffered total compression loss but no other damage), losing an additional 63 kJ/min only increases your sink rate by
(2.168 + .063) / 2.168 = 1.029
about 3%, or from 725 fpm to 746 fpm. You might not even notice this on the instruments, although if you snag on a power line at the last second as a result, you'll certainly notice that. However, at the high estimate, losing an additional 630 kJ/min would increase your sink rate by:
(2.168 + .630) / 2.168 = 1.29
29%, or from 725 fpm to 935 fpm. That's very significant. And this does not even include the extra aerodynamic drag from the spinning prop. It is only due to the energy lost in the engine.
So, in conclusion: If power fails, stop the prop.
There is, however, one final point. If you lost power because of a mechanical failure, it's very possible that the propeller will stop all on its own due to whatever damage caused the power loss. However, running out of fuel is the most common cause of in-flight power loss. If you run out of fuel, the prop will probably keep spinning unless you stop it yourself.
- Pitch angle in degrees is different from the way pitch is normally described, which is measured in inches, where something like 76"x60" would be typical. You can calculate pitch angle based on the propeller measurements in inches using the formula for helix angle. If you do, remember propeller pitch is specified at 75% of the diameter of the blade, rather than 100% as in the math textbooks).
$endgroup$
$begingroup$
Good work. A glider burns altitude as fuel to create kinetic energy. The wing uses this to more efficiently create lift. From a given altitude and mass, wing efficiency and drag determine how far you glide. The engine being turned does not affect the glide, the drag from the prop does. Not much difference there (the spinning one may even have a little less). But any loss in wing efficiency from prop turbulence will directly translate into loss of glide distance.
$endgroup$
– Robert DiGiovanni
May 17 at 22:15
add a comment |
$begingroup$
The drag is significantly more for a windmilling propeller.
Both aerodynamic drag and energy lost in the engine contribute. I estimate you will sink at least 200 FPM faster if you let the prop windmill.
For aerodynamic drag, it's impossible to convert this into a feet per minute estimate because it varies so much with the design of the propeller and the overall drag of the airplane. But you can see here:
Aerodynamics for Naval Aviators, 1965
(page 149 in the page numbers, or 167 in the PDF) that the drag can increase significantly.
A typical fixed-pitch prop has a pitch of around 15 degrees (more details at bottom). A constant-speed prop which has lost oil pressure, and is not automatically feathering, is probably more like 5 degrees. (Feathering props are used on multi-engine planes to reduce drag if one engine fails. Non-feathering props are used on single-engine planes so if the pitch control fails but the engine still works, you don't lose all your power). Overall, the actual propeller parasitic (simple aerodynamic) drag increases by up to a factor of 3. Not orders of magnitude, but it's significant. Since there's no way for me to estimate how much of the total drag is due to the propeller, all I can say is that this is probably noticeable. However, if you have a cruise prop, or an adjustable prop set to high pitch, it's possible that it works out close to even, as above 22 degrees, the windmilling prop actually has less drag.
But then there's the extra factor of the drag created by the engine, which is probably much more significant. It's possible to come up with a reasonable ballpark figure. Estimation and highschool physics are required.
An airplane without power loses potential energy, in the form of altitude, to drag. Since the airplane's speed doesn't change, its kinetic energy doesn't either and only potential energy need be considered. We calculate how quickly energy is drained out of the airplane by the spinning engine.
Work is the amount of energy that is transferred from one place to another, and power is the amount of work over time. The formula for work (in a rotational system, such as an engine) is torque * theta, where theta is the total angular distance rotated. Power (watts) is expressed in joules per second, although here I'll figure power in joules/minute because our other time units are also in minutes. The joule, of course, is the unit of both work and energy.
Assume an airplane weighing 1000kg flying at 1500 meters AGL. Its potential energy is:
1000 kg * 1500 meters * 9.8 (gravity) = 14,700,000 J (14.7 mJ)
Assuming a propeller windmilling at 200 RPM, the angular velocity is:
2pi radians / revolution * 200 revolutions / minute = ~1260 radians / minute
I estimate the torque, given in newton-meters, is somewhere between 50 and 500 Nm, tending toward the high side. 50 is from my personal experience turning a propeller at slow speeds by hand, it's about that much force; but in the air I think this is extremely optimistic. 500 is a higher estimate, justified as follows.
Single-engine planes such as the Cessna 172 frequently have a 180HP engine. The propeller normally has enough air-grabbing ability to transfer that 180HP into the air at engine redline of ~2700 RPM.
Converting HP to joules / minute (1 watt = 1 joule/second):
180 HP * (746 watts / HP) * (60 seconds / minute) = 8057 kJ / minute
Assuming the propeller efficiency is relatively constant with RPM, you can convert propeller power delivery capability linearly with RPM:
8057 kJ / minute * (200 RPM / 2700 RPM) = 596 kJ / minute
So the propeller should be able to transfer about 600 kJ / minute back into the engine. This is in the ballpark of my estimate of 500. However, as not all the normal engine power goes into the propeller (due to mechanical losses and engine powered accessories) the estimate of 500 seems to be pretty close, and I'm sticking with it for sake of simpler math. This estimate is pretty seat of the pants - lots of error sources, like variations in propeller efficiency with RPM and being driven in reverse - are ignored. But if the propeller is less efficient, it dissipates more power - so even my high estimate might be too low.
Back to the engine failure. The power dissipated by the engine is therefore:
1260 * (50 to 500 or you pick) = 63 kJ to 630 kJ per minute
A Cessna 152 has a sink rate of 725 fpm when flying at best glide with stopped propeller (best glide speeds are normally specified with stopped prop); The Cessna 172 is closer to the mass I am using, and has similar glide performance, so I'll just use that same number. This is an estimated calculation, anyway. At 725 fpm descent rate (221 meters per minute) it normally takes 6.78 minutes to bleed off that 1500 meters of altitude you started with. Dividing potential energy by time:
14,700,000 / 6.78 = 2.168 MJ/min energy loss
At the low estimate (probably reasonable only for an engine that suffered total compression loss but no other damage), losing an additional 63 kJ/min only increases your sink rate by
(2.168 + .063) / 2.168 = 1.029
about 3%, or from 725 fpm to 746 fpm. You might not even notice this on the instruments, although if you snag on a power line at the last second as a result, you'll certainly notice that. However, at the high estimate, losing an additional 630 kJ/min would increase your sink rate by:
(2.168 + .630) / 2.168 = 1.29
29%, or from 725 fpm to 935 fpm. That's very significant. And this does not even include the extra aerodynamic drag from the spinning prop. It is only due to the energy lost in the engine.
So, in conclusion: If power fails, stop the prop.
There is, however, one final point. If you lost power because of a mechanical failure, it's very possible that the propeller will stop all on its own due to whatever damage caused the power loss. However, running out of fuel is the most common cause of in-flight power loss. If you run out of fuel, the prop will probably keep spinning unless you stop it yourself.
- Pitch angle in degrees is different from the way pitch is normally described, which is measured in inches, where something like 76"x60" would be typical. You can calculate pitch angle based on the propeller measurements in inches using the formula for helix angle. If you do, remember propeller pitch is specified at 75% of the diameter of the blade, rather than 100% as in the math textbooks).
$endgroup$
$begingroup$
Good work. A glider burns altitude as fuel to create kinetic energy. The wing uses this to more efficiently create lift. From a given altitude and mass, wing efficiency and drag determine how far you glide. The engine being turned does not affect the glide, the drag from the prop does. Not much difference there (the spinning one may even have a little less). But any loss in wing efficiency from prop turbulence will directly translate into loss of glide distance.
$endgroup$
– Robert DiGiovanni
May 17 at 22:15
add a comment |
$begingroup$
The drag is significantly more for a windmilling propeller.
Both aerodynamic drag and energy lost in the engine contribute. I estimate you will sink at least 200 FPM faster if you let the prop windmill.
For aerodynamic drag, it's impossible to convert this into a feet per minute estimate because it varies so much with the design of the propeller and the overall drag of the airplane. But you can see here:
Aerodynamics for Naval Aviators, 1965
(page 149 in the page numbers, or 167 in the PDF) that the drag can increase significantly.
A typical fixed-pitch prop has a pitch of around 15 degrees (more details at bottom). A constant-speed prop which has lost oil pressure, and is not automatically feathering, is probably more like 5 degrees. (Feathering props are used on multi-engine planes to reduce drag if one engine fails. Non-feathering props are used on single-engine planes so if the pitch control fails but the engine still works, you don't lose all your power). Overall, the actual propeller parasitic (simple aerodynamic) drag increases by up to a factor of 3. Not orders of magnitude, but it's significant. Since there's no way for me to estimate how much of the total drag is due to the propeller, all I can say is that this is probably noticeable. However, if you have a cruise prop, or an adjustable prop set to high pitch, it's possible that it works out close to even, as above 22 degrees, the windmilling prop actually has less drag.
But then there's the extra factor of the drag created by the engine, which is probably much more significant. It's possible to come up with a reasonable ballpark figure. Estimation and highschool physics are required.
An airplane without power loses potential energy, in the form of altitude, to drag. Since the airplane's speed doesn't change, its kinetic energy doesn't either and only potential energy need be considered. We calculate how quickly energy is drained out of the airplane by the spinning engine.
Work is the amount of energy that is transferred from one place to another, and power is the amount of work over time. The formula for work (in a rotational system, such as an engine) is torque * theta, where theta is the total angular distance rotated. Power (watts) is expressed in joules per second, although here I'll figure power in joules/minute because our other time units are also in minutes. The joule, of course, is the unit of both work and energy.
Assume an airplane weighing 1000kg flying at 1500 meters AGL. Its potential energy is:
1000 kg * 1500 meters * 9.8 (gravity) = 14,700,000 J (14.7 mJ)
Assuming a propeller windmilling at 200 RPM, the angular velocity is:
2pi radians / revolution * 200 revolutions / minute = ~1260 radians / minute
I estimate the torque, given in newton-meters, is somewhere between 50 and 500 Nm, tending toward the high side. 50 is from my personal experience turning a propeller at slow speeds by hand, it's about that much force; but in the air I think this is extremely optimistic. 500 is a higher estimate, justified as follows.
Single-engine planes such as the Cessna 172 frequently have a 180HP engine. The propeller normally has enough air-grabbing ability to transfer that 180HP into the air at engine redline of ~2700 RPM.
Converting HP to joules / minute (1 watt = 1 joule/second):
180 HP * (746 watts / HP) * (60 seconds / minute) = 8057 kJ / minute
Assuming the propeller efficiency is relatively constant with RPM, you can convert propeller power delivery capability linearly with RPM:
8057 kJ / minute * (200 RPM / 2700 RPM) = 596 kJ / minute
So the propeller should be able to transfer about 600 kJ / minute back into the engine. This is in the ballpark of my estimate of 500. However, as not all the normal engine power goes into the propeller (due to mechanical losses and engine powered accessories) the estimate of 500 seems to be pretty close, and I'm sticking with it for sake of simpler math. This estimate is pretty seat of the pants - lots of error sources, like variations in propeller efficiency with RPM and being driven in reverse - are ignored. But if the propeller is less efficient, it dissipates more power - so even my high estimate might be too low.
Back to the engine failure. The power dissipated by the engine is therefore:
1260 * (50 to 500 or you pick) = 63 kJ to 630 kJ per minute
A Cessna 152 has a sink rate of 725 fpm when flying at best glide with stopped propeller (best glide speeds are normally specified with stopped prop); The Cessna 172 is closer to the mass I am using, and has similar glide performance, so I'll just use that same number. This is an estimated calculation, anyway. At 725 fpm descent rate (221 meters per minute) it normally takes 6.78 minutes to bleed off that 1500 meters of altitude you started with. Dividing potential energy by time:
14,700,000 / 6.78 = 2.168 MJ/min energy loss
At the low estimate (probably reasonable only for an engine that suffered total compression loss but no other damage), losing an additional 63 kJ/min only increases your sink rate by
(2.168 + .063) / 2.168 = 1.029
about 3%, or from 725 fpm to 746 fpm. You might not even notice this on the instruments, although if you snag on a power line at the last second as a result, you'll certainly notice that. However, at the high estimate, losing an additional 630 kJ/min would increase your sink rate by:
(2.168 + .630) / 2.168 = 1.29
29%, or from 725 fpm to 935 fpm. That's very significant. And this does not even include the extra aerodynamic drag from the spinning prop. It is only due to the energy lost in the engine.
So, in conclusion: If power fails, stop the prop.
There is, however, one final point. If you lost power because of a mechanical failure, it's very possible that the propeller will stop all on its own due to whatever damage caused the power loss. However, running out of fuel is the most common cause of in-flight power loss. If you run out of fuel, the prop will probably keep spinning unless you stop it yourself.
- Pitch angle in degrees is different from the way pitch is normally described, which is measured in inches, where something like 76"x60" would be typical. You can calculate pitch angle based on the propeller measurements in inches using the formula for helix angle. If you do, remember propeller pitch is specified at 75% of the diameter of the blade, rather than 100% as in the math textbooks).
$endgroup$
The drag is significantly more for a windmilling propeller.
Both aerodynamic drag and energy lost in the engine contribute. I estimate you will sink at least 200 FPM faster if you let the prop windmill.
For aerodynamic drag, it's impossible to convert this into a feet per minute estimate because it varies so much with the design of the propeller and the overall drag of the airplane. But you can see here:
Aerodynamics for Naval Aviators, 1965
(page 149 in the page numbers, or 167 in the PDF) that the drag can increase significantly.
A typical fixed-pitch prop has a pitch of around 15 degrees (more details at bottom). A constant-speed prop which has lost oil pressure, and is not automatically feathering, is probably more like 5 degrees. (Feathering props are used on multi-engine planes to reduce drag if one engine fails. Non-feathering props are used on single-engine planes so if the pitch control fails but the engine still works, you don't lose all your power). Overall, the actual propeller parasitic (simple aerodynamic) drag increases by up to a factor of 3. Not orders of magnitude, but it's significant. Since there's no way for me to estimate how much of the total drag is due to the propeller, all I can say is that this is probably noticeable. However, if you have a cruise prop, or an adjustable prop set to high pitch, it's possible that it works out close to even, as above 22 degrees, the windmilling prop actually has less drag.
But then there's the extra factor of the drag created by the engine, which is probably much more significant. It's possible to come up with a reasonable ballpark figure. Estimation and highschool physics are required.
An airplane without power loses potential energy, in the form of altitude, to drag. Since the airplane's speed doesn't change, its kinetic energy doesn't either and only potential energy need be considered. We calculate how quickly energy is drained out of the airplane by the spinning engine.
Work is the amount of energy that is transferred from one place to another, and power is the amount of work over time. The formula for work (in a rotational system, such as an engine) is torque * theta, where theta is the total angular distance rotated. Power (watts) is expressed in joules per second, although here I'll figure power in joules/minute because our other time units are also in minutes. The joule, of course, is the unit of both work and energy.
Assume an airplane weighing 1000kg flying at 1500 meters AGL. Its potential energy is:
1000 kg * 1500 meters * 9.8 (gravity) = 14,700,000 J (14.7 mJ)
Assuming a propeller windmilling at 200 RPM, the angular velocity is:
2pi radians / revolution * 200 revolutions / minute = ~1260 radians / minute
I estimate the torque, given in newton-meters, is somewhere between 50 and 500 Nm, tending toward the high side. 50 is from my personal experience turning a propeller at slow speeds by hand, it's about that much force; but in the air I think this is extremely optimistic. 500 is a higher estimate, justified as follows.
Single-engine planes such as the Cessna 172 frequently have a 180HP engine. The propeller normally has enough air-grabbing ability to transfer that 180HP into the air at engine redline of ~2700 RPM.
Converting HP to joules / minute (1 watt = 1 joule/second):
180 HP * (746 watts / HP) * (60 seconds / minute) = 8057 kJ / minute
Assuming the propeller efficiency is relatively constant with RPM, you can convert propeller power delivery capability linearly with RPM:
8057 kJ / minute * (200 RPM / 2700 RPM) = 596 kJ / minute
So the propeller should be able to transfer about 600 kJ / minute back into the engine. This is in the ballpark of my estimate of 500. However, as not all the normal engine power goes into the propeller (due to mechanical losses and engine powered accessories) the estimate of 500 seems to be pretty close, and I'm sticking with it for sake of simpler math. This estimate is pretty seat of the pants - lots of error sources, like variations in propeller efficiency with RPM and being driven in reverse - are ignored. But if the propeller is less efficient, it dissipates more power - so even my high estimate might be too low.
Back to the engine failure. The power dissipated by the engine is therefore:
1260 * (50 to 500 or you pick) = 63 kJ to 630 kJ per minute
A Cessna 152 has a sink rate of 725 fpm when flying at best glide with stopped propeller (best glide speeds are normally specified with stopped prop); The Cessna 172 is closer to the mass I am using, and has similar glide performance, so I'll just use that same number. This is an estimated calculation, anyway. At 725 fpm descent rate (221 meters per minute) it normally takes 6.78 minutes to bleed off that 1500 meters of altitude you started with. Dividing potential energy by time:
14,700,000 / 6.78 = 2.168 MJ/min energy loss
At the low estimate (probably reasonable only for an engine that suffered total compression loss but no other damage), losing an additional 63 kJ/min only increases your sink rate by
(2.168 + .063) / 2.168 = 1.029
about 3%, or from 725 fpm to 746 fpm. You might not even notice this on the instruments, although if you snag on a power line at the last second as a result, you'll certainly notice that. However, at the high estimate, losing an additional 630 kJ/min would increase your sink rate by:
(2.168 + .630) / 2.168 = 1.29
29%, or from 725 fpm to 935 fpm. That's very significant. And this does not even include the extra aerodynamic drag from the spinning prop. It is only due to the energy lost in the engine.
So, in conclusion: If power fails, stop the prop.
There is, however, one final point. If you lost power because of a mechanical failure, it's very possible that the propeller will stop all on its own due to whatever damage caused the power loss. However, running out of fuel is the most common cause of in-flight power loss. If you run out of fuel, the prop will probably keep spinning unless you stop it yourself.
- Pitch angle in degrees is different from the way pitch is normally described, which is measured in inches, where something like 76"x60" would be typical. You can calculate pitch angle based on the propeller measurements in inches using the formula for helix angle. If you do, remember propeller pitch is specified at 75% of the diameter of the blade, rather than 100% as in the math textbooks).
edited May 17 at 13:27
answered May 17 at 13:20
fluffysheapfluffysheap
1,06076
1,06076
$begingroup$
Good work. A glider burns altitude as fuel to create kinetic energy. The wing uses this to more efficiently create lift. From a given altitude and mass, wing efficiency and drag determine how far you glide. The engine being turned does not affect the glide, the drag from the prop does. Not much difference there (the spinning one may even have a little less). But any loss in wing efficiency from prop turbulence will directly translate into loss of glide distance.
$endgroup$
– Robert DiGiovanni
May 17 at 22:15
add a comment |
$begingroup$
Good work. A glider burns altitude as fuel to create kinetic energy. The wing uses this to more efficiently create lift. From a given altitude and mass, wing efficiency and drag determine how far you glide. The engine being turned does not affect the glide, the drag from the prop does. Not much difference there (the spinning one may even have a little less). But any loss in wing efficiency from prop turbulence will directly translate into loss of glide distance.
$endgroup$
– Robert DiGiovanni
May 17 at 22:15
$begingroup$
Good work. A glider burns altitude as fuel to create kinetic energy. The wing uses this to more efficiently create lift. From a given altitude and mass, wing efficiency and drag determine how far you glide. The engine being turned does not affect the glide, the drag from the prop does. Not much difference there (the spinning one may even have a little less). But any loss in wing efficiency from prop turbulence will directly translate into loss of glide distance.
$endgroup$
– Robert DiGiovanni
May 17 at 22:15
$begingroup$
Good work. A glider burns altitude as fuel to create kinetic energy. The wing uses this to more efficiently create lift. From a given altitude and mass, wing efficiency and drag determine how far you glide. The engine being turned does not affect the glide, the drag from the prop does. Not much difference there (the spinning one may even have a little less). But any loss in wing efficiency from prop turbulence will directly translate into loss of glide distance.
$endgroup$
– Robert DiGiovanni
May 17 at 22:15
add a comment |
$begingroup$
This paper provided by Erbureth provides empirical evidence to answer the question. The short answer is that sometimes a stopped propeller provided less drag and sometimes a windmilling one provided less drag. This actually makes a lot of sense to me as the drag should be related to the location of the stagnation pressure line on the prop.
A few observations from other answers:
- One of the things I always hear when this question is asked is that a rotating propeller turns into a disk and has more area. This is clearly wrong as the area of a propeller blade is always the same whether it is rotating or not.
- When a prop is feathered the prop stops windmilling and the drag is considerably less. This create the perception that the stopped propeller has much less drag but in reality it is due to the fact that the feathered prop has much less form drag. The fact that the prop is stopped is not the main reason.
$endgroup$
$begingroup$
It's worth noting that paper is on model airplanes and their wind tunnel tests are significantly below the normal flight speed. It's findings may still hold true, but I'd say to take it with a grain of salt.
$endgroup$
– TemporalWolf
May 17 at 17:26
$begingroup$
Work = force x distance, and a spinning prop goes much farther, so to speak, then a non-rotating one for the same velocity of aircraft. So while the blade area is the same, the spinning makes a big difference in the physics of the problem.
$endgroup$
– MikeY
May 18 at 12:22
$begingroup$
The clue is in the paper: they let the spinning prop freewheel without any resistance. An autorotating helicopter is still providing lift, and chopping away to push that air down.
$endgroup$
– Koyovis
May 21 at 8:09
$begingroup$
In other words: torque is the differentiator. Rotation * torque = energy extracted. No torque, no energy required.
$endgroup$
– Koyovis
May 26 at 20:03
add a comment |
$begingroup$
This paper provided by Erbureth provides empirical evidence to answer the question. The short answer is that sometimes a stopped propeller provided less drag and sometimes a windmilling one provided less drag. This actually makes a lot of sense to me as the drag should be related to the location of the stagnation pressure line on the prop.
A few observations from other answers:
- One of the things I always hear when this question is asked is that a rotating propeller turns into a disk and has more area. This is clearly wrong as the area of a propeller blade is always the same whether it is rotating or not.
- When a prop is feathered the prop stops windmilling and the drag is considerably less. This create the perception that the stopped propeller has much less drag but in reality it is due to the fact that the feathered prop has much less form drag. The fact that the prop is stopped is not the main reason.
$endgroup$
$begingroup$
It's worth noting that paper is on model airplanes and their wind tunnel tests are significantly below the normal flight speed. It's findings may still hold true, but I'd say to take it with a grain of salt.
$endgroup$
– TemporalWolf
May 17 at 17:26
$begingroup$
Work = force x distance, and a spinning prop goes much farther, so to speak, then a non-rotating one for the same velocity of aircraft. So while the blade area is the same, the spinning makes a big difference in the physics of the problem.
$endgroup$
– MikeY
May 18 at 12:22
$begingroup$
The clue is in the paper: they let the spinning prop freewheel without any resistance. An autorotating helicopter is still providing lift, and chopping away to push that air down.
$endgroup$
– Koyovis
May 21 at 8:09
$begingroup$
In other words: torque is the differentiator. Rotation * torque = energy extracted. No torque, no energy required.
$endgroup$
– Koyovis
May 26 at 20:03
add a comment |
$begingroup$
This paper provided by Erbureth provides empirical evidence to answer the question. The short answer is that sometimes a stopped propeller provided less drag and sometimes a windmilling one provided less drag. This actually makes a lot of sense to me as the drag should be related to the location of the stagnation pressure line on the prop.
A few observations from other answers:
- One of the things I always hear when this question is asked is that a rotating propeller turns into a disk and has more area. This is clearly wrong as the area of a propeller blade is always the same whether it is rotating or not.
- When a prop is feathered the prop stops windmilling and the drag is considerably less. This create the perception that the stopped propeller has much less drag but in reality it is due to the fact that the feathered prop has much less form drag. The fact that the prop is stopped is not the main reason.
$endgroup$
This paper provided by Erbureth provides empirical evidence to answer the question. The short answer is that sometimes a stopped propeller provided less drag and sometimes a windmilling one provided less drag. This actually makes a lot of sense to me as the drag should be related to the location of the stagnation pressure line on the prop.
A few observations from other answers:
- One of the things I always hear when this question is asked is that a rotating propeller turns into a disk and has more area. This is clearly wrong as the area of a propeller blade is always the same whether it is rotating or not.
- When a prop is feathered the prop stops windmilling and the drag is considerably less. This create the perception that the stopped propeller has much less drag but in reality it is due to the fact that the feathered prop has much less form drag. The fact that the prop is stopped is not the main reason.
answered May 17 at 16:33
DLHDLH
3,0661034
3,0661034
$begingroup$
It's worth noting that paper is on model airplanes and their wind tunnel tests are significantly below the normal flight speed. It's findings may still hold true, but I'd say to take it with a grain of salt.
$endgroup$
– TemporalWolf
May 17 at 17:26
$begingroup$
Work = force x distance, and a spinning prop goes much farther, so to speak, then a non-rotating one for the same velocity of aircraft. So while the blade area is the same, the spinning makes a big difference in the physics of the problem.
$endgroup$
– MikeY
May 18 at 12:22
$begingroup$
The clue is in the paper: they let the spinning prop freewheel without any resistance. An autorotating helicopter is still providing lift, and chopping away to push that air down.
$endgroup$
– Koyovis
May 21 at 8:09
$begingroup$
In other words: torque is the differentiator. Rotation * torque = energy extracted. No torque, no energy required.
$endgroup$
– Koyovis
May 26 at 20:03
add a comment |
$begingroup$
It's worth noting that paper is on model airplanes and their wind tunnel tests are significantly below the normal flight speed. It's findings may still hold true, but I'd say to take it with a grain of salt.
$endgroup$
– TemporalWolf
May 17 at 17:26
$begingroup$
Work = force x distance, and a spinning prop goes much farther, so to speak, then a non-rotating one for the same velocity of aircraft. So while the blade area is the same, the spinning makes a big difference in the physics of the problem.
$endgroup$
– MikeY
May 18 at 12:22
$begingroup$
The clue is in the paper: they let the spinning prop freewheel without any resistance. An autorotating helicopter is still providing lift, and chopping away to push that air down.
$endgroup$
– Koyovis
May 21 at 8:09
$begingroup$
In other words: torque is the differentiator. Rotation * torque = energy extracted. No torque, no energy required.
$endgroup$
– Koyovis
May 26 at 20:03
$begingroup$
It's worth noting that paper is on model airplanes and their wind tunnel tests are significantly below the normal flight speed. It's findings may still hold true, but I'd say to take it with a grain of salt.
$endgroup$
– TemporalWolf
May 17 at 17:26
$begingroup$
It's worth noting that paper is on model airplanes and their wind tunnel tests are significantly below the normal flight speed. It's findings may still hold true, but I'd say to take it with a grain of salt.
$endgroup$
– TemporalWolf
May 17 at 17:26
$begingroup$
Work = force x distance, and a spinning prop goes much farther, so to speak, then a non-rotating one for the same velocity of aircraft. So while the blade area is the same, the spinning makes a big difference in the physics of the problem.
$endgroup$
– MikeY
May 18 at 12:22
$begingroup$
Work = force x distance, and a spinning prop goes much farther, so to speak, then a non-rotating one for the same velocity of aircraft. So while the blade area is the same, the spinning makes a big difference in the physics of the problem.
$endgroup$
– MikeY
May 18 at 12:22
$begingroup$
The clue is in the paper: they let the spinning prop freewheel without any resistance. An autorotating helicopter is still providing lift, and chopping away to push that air down.
$endgroup$
– Koyovis
May 21 at 8:09
$begingroup$
The clue is in the paper: they let the spinning prop freewheel without any resistance. An autorotating helicopter is still providing lift, and chopping away to push that air down.
$endgroup$
– Koyovis
May 21 at 8:09
$begingroup$
In other words: torque is the differentiator. Rotation * torque = energy extracted. No torque, no energy required.
$endgroup$
– Koyovis
May 26 at 20:03
$begingroup$
In other words: torque is the differentiator. Rotation * torque = energy extracted. No torque, no energy required.
$endgroup$
– Koyovis
May 26 at 20:03
add a comment |
$begingroup$
The argument that the windmilling prop is slowing the plane down by extracting energy to turn a dead engine ignores the fact that a frozen prop tries to turn the whole plane. The control inputs to keep the plane level are probably very close, and the turning airfoil may actually be slightly less draggy, so what is going on here?
It is well known that props are airfoils, and turbulence created by one blade affects the other.
In the windmilling case, the turbulence created by the propellor has a greater affect on that other airfoil, the wing.
This is mostly likely the major factor in loss of gliding distance. Important to realize the air that the plane is gliding through has no kinetic energy to extract, it's all in the kinetic and potential energy of the plane. But the windmilling prop does lower the efficiency of the wing in using the planes energy by creating more turbulence.
$endgroup$
1
$begingroup$
First sentence: it tries but doesn't succeed, so it's not doing any work on the plane.
$endgroup$
– hobbs
May 18 at 1:57
$begingroup$
It (unmoving) produces drag, a force on the plane. So does the moving one. WRT forces affecting the glide, that is what matters. Turning the engine is work by definition (net movement of engine from force) but the movement of the engine does not affect glide. The turbulence created by the rotating prop (which we COULD say is energy extracted from the glide forces) does.
$endgroup$
– Robert DiGiovanni
May 18 at 3:42
add a comment |
$begingroup$
The argument that the windmilling prop is slowing the plane down by extracting energy to turn a dead engine ignores the fact that a frozen prop tries to turn the whole plane. The control inputs to keep the plane level are probably very close, and the turning airfoil may actually be slightly less draggy, so what is going on here?
It is well known that props are airfoils, and turbulence created by one blade affects the other.
In the windmilling case, the turbulence created by the propellor has a greater affect on that other airfoil, the wing.
This is mostly likely the major factor in loss of gliding distance. Important to realize the air that the plane is gliding through has no kinetic energy to extract, it's all in the kinetic and potential energy of the plane. But the windmilling prop does lower the efficiency of the wing in using the planes energy by creating more turbulence.
$endgroup$
1
$begingroup$
First sentence: it tries but doesn't succeed, so it's not doing any work on the plane.
$endgroup$
– hobbs
May 18 at 1:57
$begingroup$
It (unmoving) produces drag, a force on the plane. So does the moving one. WRT forces affecting the glide, that is what matters. Turning the engine is work by definition (net movement of engine from force) but the movement of the engine does not affect glide. The turbulence created by the rotating prop (which we COULD say is energy extracted from the glide forces) does.
$endgroup$
– Robert DiGiovanni
May 18 at 3:42
add a comment |
$begingroup$
The argument that the windmilling prop is slowing the plane down by extracting energy to turn a dead engine ignores the fact that a frozen prop tries to turn the whole plane. The control inputs to keep the plane level are probably very close, and the turning airfoil may actually be slightly less draggy, so what is going on here?
It is well known that props are airfoils, and turbulence created by one blade affects the other.
In the windmilling case, the turbulence created by the propellor has a greater affect on that other airfoil, the wing.
This is mostly likely the major factor in loss of gliding distance. Important to realize the air that the plane is gliding through has no kinetic energy to extract, it's all in the kinetic and potential energy of the plane. But the windmilling prop does lower the efficiency of the wing in using the planes energy by creating more turbulence.
$endgroup$
The argument that the windmilling prop is slowing the plane down by extracting energy to turn a dead engine ignores the fact that a frozen prop tries to turn the whole plane. The control inputs to keep the plane level are probably very close, and the turning airfoil may actually be slightly less draggy, so what is going on here?
It is well known that props are airfoils, and turbulence created by one blade affects the other.
In the windmilling case, the turbulence created by the propellor has a greater affect on that other airfoil, the wing.
This is mostly likely the major factor in loss of gliding distance. Important to realize the air that the plane is gliding through has no kinetic energy to extract, it's all in the kinetic and potential energy of the plane. But the windmilling prop does lower the efficiency of the wing in using the planes energy by creating more turbulence.
answered May 17 at 19:47
Robert DiGiovanniRobert DiGiovanni
3,5191317
3,5191317
1
$begingroup$
First sentence: it tries but doesn't succeed, so it's not doing any work on the plane.
$endgroup$
– hobbs
May 18 at 1:57
$begingroup$
It (unmoving) produces drag, a force on the plane. So does the moving one. WRT forces affecting the glide, that is what matters. Turning the engine is work by definition (net movement of engine from force) but the movement of the engine does not affect glide. The turbulence created by the rotating prop (which we COULD say is energy extracted from the glide forces) does.
$endgroup$
– Robert DiGiovanni
May 18 at 3:42
add a comment |
1
$begingroup$
First sentence: it tries but doesn't succeed, so it's not doing any work on the plane.
$endgroup$
– hobbs
May 18 at 1:57
$begingroup$
It (unmoving) produces drag, a force on the plane. So does the moving one. WRT forces affecting the glide, that is what matters. Turning the engine is work by definition (net movement of engine from force) but the movement of the engine does not affect glide. The turbulence created by the rotating prop (which we COULD say is energy extracted from the glide forces) does.
$endgroup$
– Robert DiGiovanni
May 18 at 3:42
1
1
$begingroup$
First sentence: it tries but doesn't succeed, so it's not doing any work on the plane.
$endgroup$
– hobbs
May 18 at 1:57
$begingroup$
First sentence: it tries but doesn't succeed, so it's not doing any work on the plane.
$endgroup$
– hobbs
May 18 at 1:57
$begingroup$
It (unmoving) produces drag, a force on the plane. So does the moving one. WRT forces affecting the glide, that is what matters. Turning the engine is work by definition (net movement of engine from force) but the movement of the engine does not affect glide. The turbulence created by the rotating prop (which we COULD say is energy extracted from the glide forces) does.
$endgroup$
– Robert DiGiovanni
May 18 at 3:42
$begingroup$
It (unmoving) produces drag, a force on the plane. So does the moving one. WRT forces affecting the glide, that is what matters. Turning the engine is work by definition (net movement of engine from force) but the movement of the engine does not affect glide. The turbulence created by the rotating prop (which we COULD say is energy extracted from the glide forces) does.
$endgroup$
– Robert DiGiovanni
May 18 at 3:42
add a comment |
$begingroup$
I have tested this multiple times in a C152. Starting at 10,000 feet and cutting off the fuel to the engine -applying nose up to hold altitude as long as possible (thereby slowing my forward speed) until stopping the propeller. Then gliding with the propeller stopped for quite a distance, passing over multiple airports in the process. A windmilling propeller left me short by a significant distance.
I know I was weird in my younger days, but I was flying!
$endgroup$
$begingroup$
It is not completely clear to me which method the answerer is saying allowed the longer glide. This answer could benefit greatly from a little re-wording. I am reading it to say that the prop stopped resulted in the poorer glide ratio but I'm not sure that's what the answerer really meant to say.
$endgroup$
– quiet flyer
May 25 at 6:34
add a comment |
$begingroup$
I have tested this multiple times in a C152. Starting at 10,000 feet and cutting off the fuel to the engine -applying nose up to hold altitude as long as possible (thereby slowing my forward speed) until stopping the propeller. Then gliding with the propeller stopped for quite a distance, passing over multiple airports in the process. A windmilling propeller left me short by a significant distance.
I know I was weird in my younger days, but I was flying!
$endgroup$
$begingroup$
It is not completely clear to me which method the answerer is saying allowed the longer glide. This answer could benefit greatly from a little re-wording. I am reading it to say that the prop stopped resulted in the poorer glide ratio but I'm not sure that's what the answerer really meant to say.
$endgroup$
– quiet flyer
May 25 at 6:34
add a comment |
$begingroup$
I have tested this multiple times in a C152. Starting at 10,000 feet and cutting off the fuel to the engine -applying nose up to hold altitude as long as possible (thereby slowing my forward speed) until stopping the propeller. Then gliding with the propeller stopped for quite a distance, passing over multiple airports in the process. A windmilling propeller left me short by a significant distance.
I know I was weird in my younger days, but I was flying!
$endgroup$
I have tested this multiple times in a C152. Starting at 10,000 feet and cutting off the fuel to the engine -applying nose up to hold altitude as long as possible (thereby slowing my forward speed) until stopping the propeller. Then gliding with the propeller stopped for quite a distance, passing over multiple airports in the process. A windmilling propeller left me short by a significant distance.
I know I was weird in my younger days, but I was flying!
edited May 25 at 18:33
answered May 25 at 5:58
Mike BrassMike Brass
4831210
4831210
$begingroup$
It is not completely clear to me which method the answerer is saying allowed the longer glide. This answer could benefit greatly from a little re-wording. I am reading it to say that the prop stopped resulted in the poorer glide ratio but I'm not sure that's what the answerer really meant to say.
$endgroup$
– quiet flyer
May 25 at 6:34
add a comment |
$begingroup$
It is not completely clear to me which method the answerer is saying allowed the longer glide. This answer could benefit greatly from a little re-wording. I am reading it to say that the prop stopped resulted in the poorer glide ratio but I'm not sure that's what the answerer really meant to say.
$endgroup$
– quiet flyer
May 25 at 6:34
$begingroup$
It is not completely clear to me which method the answerer is saying allowed the longer glide. This answer could benefit greatly from a little re-wording. I am reading it to say that the prop stopped resulted in the poorer glide ratio but I'm not sure that's what the answerer really meant to say.
$endgroup$
– quiet flyer
May 25 at 6:34
$begingroup$
It is not completely clear to me which method the answerer is saying allowed the longer glide. This answer could benefit greatly from a little re-wording. I am reading it to say that the prop stopped resulted in the poorer glide ratio but I'm not sure that's what the answerer really meant to say.
$endgroup$
– quiet flyer
May 25 at 6:34
add a comment |
$begingroup$
A windmilling prop is allowing the slipstream to push it around. A stopped one is fighting the slipstream - pushing/deflecting it into a spiral. The reaction from that is what tries to turn the plane, as Robert DiGiovanni says. And it is doing work, because it's applying a force to the air, which moves as a result of it.
So I'd expect less drag from windmilling. Its like freewheeling on a bike versus having a locked-up wheel.
I'm assuming same AoA in both cases, i.e that stopped does not imply feathered. Some people appear to have assumed the opposite, to which I'm curious: how would you feather a fixed pitch prop, which is what is stated in OP.
$endgroup$
$begingroup$
Have removed the -1.
$endgroup$
– Koyovis
May 21 at 3:28
add a comment |
$begingroup$
A windmilling prop is allowing the slipstream to push it around. A stopped one is fighting the slipstream - pushing/deflecting it into a spiral. The reaction from that is what tries to turn the plane, as Robert DiGiovanni says. And it is doing work, because it's applying a force to the air, which moves as a result of it.
So I'd expect less drag from windmilling. Its like freewheeling on a bike versus having a locked-up wheel.
I'm assuming same AoA in both cases, i.e that stopped does not imply feathered. Some people appear to have assumed the opposite, to which I'm curious: how would you feather a fixed pitch prop, which is what is stated in OP.
$endgroup$
$begingroup$
Have removed the -1.
$endgroup$
– Koyovis
May 21 at 3:28
add a comment |
$begingroup$
A windmilling prop is allowing the slipstream to push it around. A stopped one is fighting the slipstream - pushing/deflecting it into a spiral. The reaction from that is what tries to turn the plane, as Robert DiGiovanni says. And it is doing work, because it's applying a force to the air, which moves as a result of it.
So I'd expect less drag from windmilling. Its like freewheeling on a bike versus having a locked-up wheel.
I'm assuming same AoA in both cases, i.e that stopped does not imply feathered. Some people appear to have assumed the opposite, to which I'm curious: how would you feather a fixed pitch prop, which is what is stated in OP.
$endgroup$
A windmilling prop is allowing the slipstream to push it around. A stopped one is fighting the slipstream - pushing/deflecting it into a spiral. The reaction from that is what tries to turn the plane, as Robert DiGiovanni says. And it is doing work, because it's applying a force to the air, which moves as a result of it.
So I'd expect less drag from windmilling. Its like freewheeling on a bike versus having a locked-up wheel.
I'm assuming same AoA in both cases, i.e that stopped does not imply feathered. Some people appear to have assumed the opposite, to which I'm curious: how would you feather a fixed pitch prop, which is what is stated in OP.
edited May 21 at 3:27
Koyovis
29.5k679159
29.5k679159
answered May 19 at 18:03
BlokeDownThePubBlokeDownThePub
111
111
$begingroup$
Have removed the -1.
$endgroup$
– Koyovis
May 21 at 3:28
add a comment |
$begingroup$
Have removed the -1.
$endgroup$
– Koyovis
May 21 at 3:28
$begingroup$
Have removed the -1.
$endgroup$
– Koyovis
May 21 at 3:28
$begingroup$
Have removed the -1.
$endgroup$
– Koyovis
May 21 at 3:28
add a comment |
Thanks for contributing an answer to Aviation Stack Exchange!
- Please be sure to answer the question. Provide details and share your research!
But avoid …
- Asking for help, clarification, or responding to other answers.
- Making statements based on opinion; back them up with references or personal experience.
Use MathJax to format equations. MathJax reference.
To learn more, see our tips on writing great answers.
Sign up or log in
StackExchange.ready(function ()
StackExchange.helpers.onClickDraftSave('#login-link');
);
Sign up using Google
Sign up using Facebook
Sign up using Email and Password
Post as a guest
Required, but never shown
StackExchange.ready(
function ()
StackExchange.openid.initPostLogin('.new-post-login', 'https%3a%2f%2faviation.stackexchange.com%2fquestions%2f64394%2fdoes-a-windmilling-propeller-create-more-drag-than-a-stopped-propeller-in-an-eng%23new-answer', 'question_page');
);
Post as a guest
Required, but never shown
Sign up or log in
StackExchange.ready(function ()
StackExchange.helpers.onClickDraftSave('#login-link');
);
Sign up using Google
Sign up using Facebook
Sign up using Email and Password
Post as a guest
Required, but never shown
Sign up or log in
StackExchange.ready(function ()
StackExchange.helpers.onClickDraftSave('#login-link');
);
Sign up using Google
Sign up using Facebook
Sign up using Email and Password
Post as a guest
Required, but never shown
Sign up or log in
StackExchange.ready(function ()
StackExchange.helpers.onClickDraftSave('#login-link');
);
Sign up using Google
Sign up using Facebook
Sign up using Email and Password
Sign up using Google
Sign up using Facebook
Sign up using Email and Password
Post as a guest
Required, but never shown
Required, but never shown
Required, but never shown
Required, but never shown
Required, but never shown
Required, but never shown
Required, but never shown
Required, but never shown
Required, but never shown
hiU90ITt7Ob3uA0EDHI7 6qBMGKCkH gvWsq69 A6zs MZ1P9n9UQVOj2MR I7sqE
2
$begingroup$
I would be surprised if something like a 172 would windmill the prop at all, especially where the air is thinner at 10,000 feet. A lot of times engine failure means the engine locks up. Fuel starvation (more common) can let the prop spin, but there is a lot of force needed to spin a prop. I think a spinning prop is a lot more common on aircraft that don't have direct drive, like a turbo prop than it is for direct driven propellers.
$endgroup$
– Ron Beyer
May 16 at 20:25
1
$begingroup$
There are some situations such as model airplanes/ sailplanes with brushless electric motors where the answer is not cut-and-dried and depends on many variables.
$endgroup$
– quiet flyer
May 16 at 21:51
4
$begingroup$
Yes a Cessna 172 can definitely keep the prop windmilling. You have to slow to near stall speed to stop it. After that you can speed up and it won't windmill till you get going rather fast. I'm sure the drag is less with the prop stopped in that case.
$endgroup$
– quiet flyer
May 16 at 21:52
1
$begingroup$
Air density probably doesn't matter, if we are talking about the tendency of the prop to windmill at any given IAS.
$endgroup$
– quiet flyer
May 16 at 21:54
1
$begingroup$
Windmilling propeller can even have less drag: peter2000.co.uk/aviation/misc/prop.pdf
$endgroup$
– Erbureth
May 17 at 14:53