How to forge a multi-part weapon? [closed]How would weapons and armour be affected if metal weight was negligible?How to subtly identify a weapon as powerfully magical?What alloy could replace brass in most applications?Going from Magic to TechnologyHow does a modern military defend against a guerrilla Army of wizardsHow to integrate magic with nature, avoid the “our world with magic tacked on” problem?How can this more technologically-advanced army efficiently fight against a less developed mixed human/undead foe?Help designing which metals are associated with specific magical powers in my magic systemWhat would prevent living skin from being a good conductor for magic?No Iron for your fair-folk maiden? (Part 1: alkaline)
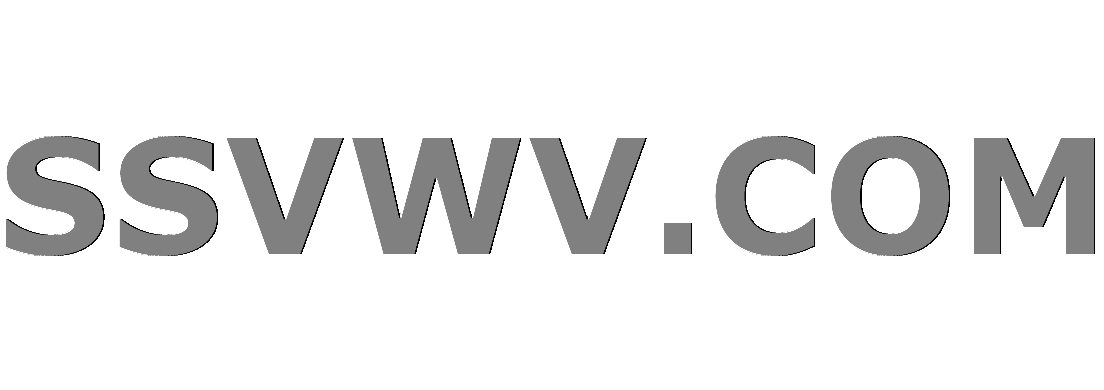
Multi tool use
How would modern naval warfare have to have developed differently for battleships to still be relevant in the 21st century?
Why does Linux list NVMe drives as /dev/nvme0 instead of /dev/sda?
How large would a mega structure have to be to host 1 billion people indefinitely?
How long would it take to cross the Channel in 1890's?
How many people are necessary to maintain modern civilisation?
How did Gollum enter Moria?
Heavily limited premature compiler translates text into excecutable python code
Why is it easier to balance a non-moving bike standing up than sitting down?
How does DC work with natural 20?
Why does the Saturn V have standalone inter-stage rings?
"Correct me if I'm wrong"
Prime sieve in Python
How to make clear to people I don't want to answer their "Where are you from?" question?
`-` in tar xzf -
Will generated tokens be progressively stronger when using Cathar's Crusade and Sorin, Grim Nemesis?
How do I farm creepers for XP without them exploding?
Cut the gold chain
career in signal processing
LWC - Local Dev - How can I run the local server on HTTPS?
Did the CIA blow up a Siberian pipeline in 1982?
Designing a magic-compatible polearm
Is it illegal to withhold someone's passport and green card in California?
Why don't countries like Japan just print more money?
Hit the Bulls Eye with T in the Center
How to forge a multi-part weapon? [closed]
How would weapons and armour be affected if metal weight was negligible?How to subtly identify a weapon as powerfully magical?What alloy could replace brass in most applications?Going from Magic to TechnologyHow does a modern military defend against a guerrilla Army of wizardsHow to integrate magic with nature, avoid the “our world with magic tacked on” problem?How can this more technologically-advanced army efficiently fight against a less developed mixed human/undead foe?Help designing which metals are associated with specific magical powers in my magic systemWhat would prevent living skin from being a good conductor for magic?No Iron for your fair-folk maiden? (Part 1: alkaline)
.everyoneloves__top-leaderboard:empty,.everyoneloves__mid-leaderboard:empty,.everyoneloves__bot-mid-leaderboard:empty margin-bottom:0;
$begingroup$
So, I'm trying to forge a magic sword. Naturally, this requires magic metal.
Luckily, I have access to just such a thing: Spectral metal. Spectral metals are ordinary metals which have been infused with and transformed by otherworldly energy, and each different metal has a different effect; Spectral iron, for instance, burns fairies (and is exceptionally easy to enchant with other qualities), spectral silver is toxic (and particularly effective against lycanthropes), spectral copper will build up an electric charge over time, et cetera.
Spectral metal also has varying potency, depending on the spectrocity index (that is, the percentage of "spectral-ness" compared to the theoretical maximum). Higher spectrocity metal has greater effects: 0% spectrocity is mundane metal, while 100% is metal that is completely saturated with otherworldly power. Mixing spectral metal with mundane metal will lower the spectrocity index intuitively (that is, mixing 50% spectrocity metal with an equal mass of mundane metal will result in a 25% spectrocity metal, and so on).
The abilities and qualities of spectral metal vary wildly, and spectral alloys often have effects that aren't found in any of the component metals. I haven't even come close to discovering all the different effects of different metals and combinations. However, they all have one thing in common: Spectral metal is always physically weaker than its mundane counterpart. Specifically, spectral metal is more brittle than mundane metal and can withstand less stress of all types. The higher the spectrocity index, the more fragile the resulting metal. This can actually get pretty extreme; at around 70 to 90% spectrocity, most metals will start to sublimate (each spectral metal has a more specific sublimation point).
Naturally, this leaves me with a problem. I want my sword to have as much magical potency as I can muster, but I also don't want it to break easily. How can I overcome this dilemma?
My current idea is to make the sword mostly out of mundane metal, with only the edges being spectral; this way, the sword retains the structural strength of conventional steel, while retaining potent magical properties. However, I'm not super experienced with metallurgy, so I'm not sure how to do this without significantly mixing the two alloys. What forging techniques allow me to seamlessly mold two different alloys into a single form without mixing them too much, and what technology is prerequisite to achieve this?
Alternatively, what other viable methods are there to attach spectral blades to a mundane sword without making it more prone to failure, or dramatically increasing the required maintenance?
I tend to travel a lot, so I'm interested in hearing both primitive and high-tech solutions to the problem at hand.
magic engineering metalworking
$endgroup$
closed as off-topic by sphennings, Don Qualm, JBH, Morris The Cat, ltmauve Jun 5 at 20:12
This question appears to be off-topic. The users who voted to close gave this specific reason:
- "This question does not appear to be about worldbuilding, within the scope defined in the help center." – sphennings, Don Qualm, JBH
add a comment |
$begingroup$
So, I'm trying to forge a magic sword. Naturally, this requires magic metal.
Luckily, I have access to just such a thing: Spectral metal. Spectral metals are ordinary metals which have been infused with and transformed by otherworldly energy, and each different metal has a different effect; Spectral iron, for instance, burns fairies (and is exceptionally easy to enchant with other qualities), spectral silver is toxic (and particularly effective against lycanthropes), spectral copper will build up an electric charge over time, et cetera.
Spectral metal also has varying potency, depending on the spectrocity index (that is, the percentage of "spectral-ness" compared to the theoretical maximum). Higher spectrocity metal has greater effects: 0% spectrocity is mundane metal, while 100% is metal that is completely saturated with otherworldly power. Mixing spectral metal with mundane metal will lower the spectrocity index intuitively (that is, mixing 50% spectrocity metal with an equal mass of mundane metal will result in a 25% spectrocity metal, and so on).
The abilities and qualities of spectral metal vary wildly, and spectral alloys often have effects that aren't found in any of the component metals. I haven't even come close to discovering all the different effects of different metals and combinations. However, they all have one thing in common: Spectral metal is always physically weaker than its mundane counterpart. Specifically, spectral metal is more brittle than mundane metal and can withstand less stress of all types. The higher the spectrocity index, the more fragile the resulting metal. This can actually get pretty extreme; at around 70 to 90% spectrocity, most metals will start to sublimate (each spectral metal has a more specific sublimation point).
Naturally, this leaves me with a problem. I want my sword to have as much magical potency as I can muster, but I also don't want it to break easily. How can I overcome this dilemma?
My current idea is to make the sword mostly out of mundane metal, with only the edges being spectral; this way, the sword retains the structural strength of conventional steel, while retaining potent magical properties. However, I'm not super experienced with metallurgy, so I'm not sure how to do this without significantly mixing the two alloys. What forging techniques allow me to seamlessly mold two different alloys into a single form without mixing them too much, and what technology is prerequisite to achieve this?
Alternatively, what other viable methods are there to attach spectral blades to a mundane sword without making it more prone to failure, or dramatically increasing the required maintenance?
I tend to travel a lot, so I'm interested in hearing both primitive and high-tech solutions to the problem at hand.
magic engineering metalworking
$endgroup$
closed as off-topic by sphennings, Don Qualm, JBH, Morris The Cat, ltmauve Jun 5 at 20:12
This question appears to be off-topic. The users who voted to close gave this specific reason:
- "This question does not appear to be about worldbuilding, within the scope defined in the help center." – sphennings, Don Qualm, JBH
$begingroup$
Comments are not for extended discussion; this conversation has been moved to chat.
$endgroup$
– James♦
Jun 4 at 20:47
$begingroup$
The help center states, "To prevent your question from being flagged and possibly removed, avoid asking subjective questions where … your answer is provided along with the question, and you expect more answers." SE is not a discussion forum. SE's Q&A model is one-specific-question/one-best-answer. To answer the fundamental Q we would need to know where your metal falls in the periodic table (to deal with allowing/annealing) and your magic system. Can you edit this to meet all these expectations?
$endgroup$
– JBH
Jun 5 at 19:32
$begingroup$
If (for instance) said sword could build electric energy would it ever actually hit anything or could it just shoot a bolt of electricity, leaving the blade unharmed?
$endgroup$
– A Writer
Jun 5 at 19:33
add a comment |
$begingroup$
So, I'm trying to forge a magic sword. Naturally, this requires magic metal.
Luckily, I have access to just such a thing: Spectral metal. Spectral metals are ordinary metals which have been infused with and transformed by otherworldly energy, and each different metal has a different effect; Spectral iron, for instance, burns fairies (and is exceptionally easy to enchant with other qualities), spectral silver is toxic (and particularly effective against lycanthropes), spectral copper will build up an electric charge over time, et cetera.
Spectral metal also has varying potency, depending on the spectrocity index (that is, the percentage of "spectral-ness" compared to the theoretical maximum). Higher spectrocity metal has greater effects: 0% spectrocity is mundane metal, while 100% is metal that is completely saturated with otherworldly power. Mixing spectral metal with mundane metal will lower the spectrocity index intuitively (that is, mixing 50% spectrocity metal with an equal mass of mundane metal will result in a 25% spectrocity metal, and so on).
The abilities and qualities of spectral metal vary wildly, and spectral alloys often have effects that aren't found in any of the component metals. I haven't even come close to discovering all the different effects of different metals and combinations. However, they all have one thing in common: Spectral metal is always physically weaker than its mundane counterpart. Specifically, spectral metal is more brittle than mundane metal and can withstand less stress of all types. The higher the spectrocity index, the more fragile the resulting metal. This can actually get pretty extreme; at around 70 to 90% spectrocity, most metals will start to sublimate (each spectral metal has a more specific sublimation point).
Naturally, this leaves me with a problem. I want my sword to have as much magical potency as I can muster, but I also don't want it to break easily. How can I overcome this dilemma?
My current idea is to make the sword mostly out of mundane metal, with only the edges being spectral; this way, the sword retains the structural strength of conventional steel, while retaining potent magical properties. However, I'm not super experienced with metallurgy, so I'm not sure how to do this without significantly mixing the two alloys. What forging techniques allow me to seamlessly mold two different alloys into a single form without mixing them too much, and what technology is prerequisite to achieve this?
Alternatively, what other viable methods are there to attach spectral blades to a mundane sword without making it more prone to failure, or dramatically increasing the required maintenance?
I tend to travel a lot, so I'm interested in hearing both primitive and high-tech solutions to the problem at hand.
magic engineering metalworking
$endgroup$
So, I'm trying to forge a magic sword. Naturally, this requires magic metal.
Luckily, I have access to just such a thing: Spectral metal. Spectral metals are ordinary metals which have been infused with and transformed by otherworldly energy, and each different metal has a different effect; Spectral iron, for instance, burns fairies (and is exceptionally easy to enchant with other qualities), spectral silver is toxic (and particularly effective against lycanthropes), spectral copper will build up an electric charge over time, et cetera.
Spectral metal also has varying potency, depending on the spectrocity index (that is, the percentage of "spectral-ness" compared to the theoretical maximum). Higher spectrocity metal has greater effects: 0% spectrocity is mundane metal, while 100% is metal that is completely saturated with otherworldly power. Mixing spectral metal with mundane metal will lower the spectrocity index intuitively (that is, mixing 50% spectrocity metal with an equal mass of mundane metal will result in a 25% spectrocity metal, and so on).
The abilities and qualities of spectral metal vary wildly, and spectral alloys often have effects that aren't found in any of the component metals. I haven't even come close to discovering all the different effects of different metals and combinations. However, they all have one thing in common: Spectral metal is always physically weaker than its mundane counterpart. Specifically, spectral metal is more brittle than mundane metal and can withstand less stress of all types. The higher the spectrocity index, the more fragile the resulting metal. This can actually get pretty extreme; at around 70 to 90% spectrocity, most metals will start to sublimate (each spectral metal has a more specific sublimation point).
Naturally, this leaves me with a problem. I want my sword to have as much magical potency as I can muster, but I also don't want it to break easily. How can I overcome this dilemma?
My current idea is to make the sword mostly out of mundane metal, with only the edges being spectral; this way, the sword retains the structural strength of conventional steel, while retaining potent magical properties. However, I'm not super experienced with metallurgy, so I'm not sure how to do this without significantly mixing the two alloys. What forging techniques allow me to seamlessly mold two different alloys into a single form without mixing them too much, and what technology is prerequisite to achieve this?
Alternatively, what other viable methods are there to attach spectral blades to a mundane sword without making it more prone to failure, or dramatically increasing the required maintenance?
I tend to travel a lot, so I'm interested in hearing both primitive and high-tech solutions to the problem at hand.
magic engineering metalworking
magic engineering metalworking
edited Jun 4 at 6:35
Globin347
asked Jun 4 at 5:03


Globin347Globin347
13118
13118
closed as off-topic by sphennings, Don Qualm, JBH, Morris The Cat, ltmauve Jun 5 at 20:12
This question appears to be off-topic. The users who voted to close gave this specific reason:
- "This question does not appear to be about worldbuilding, within the scope defined in the help center." – sphennings, Don Qualm, JBH
closed as off-topic by sphennings, Don Qualm, JBH, Morris The Cat, ltmauve Jun 5 at 20:12
This question appears to be off-topic. The users who voted to close gave this specific reason:
- "This question does not appear to be about worldbuilding, within the scope defined in the help center." – sphennings, Don Qualm, JBH
$begingroup$
Comments are not for extended discussion; this conversation has been moved to chat.
$endgroup$
– James♦
Jun 4 at 20:47
$begingroup$
The help center states, "To prevent your question from being flagged and possibly removed, avoid asking subjective questions where … your answer is provided along with the question, and you expect more answers." SE is not a discussion forum. SE's Q&A model is one-specific-question/one-best-answer. To answer the fundamental Q we would need to know where your metal falls in the periodic table (to deal with allowing/annealing) and your magic system. Can you edit this to meet all these expectations?
$endgroup$
– JBH
Jun 5 at 19:32
$begingroup$
If (for instance) said sword could build electric energy would it ever actually hit anything or could it just shoot a bolt of electricity, leaving the blade unharmed?
$endgroup$
– A Writer
Jun 5 at 19:33
add a comment |
$begingroup$
Comments are not for extended discussion; this conversation has been moved to chat.
$endgroup$
– James♦
Jun 4 at 20:47
$begingroup$
The help center states, "To prevent your question from being flagged and possibly removed, avoid asking subjective questions where … your answer is provided along with the question, and you expect more answers." SE is not a discussion forum. SE's Q&A model is one-specific-question/one-best-answer. To answer the fundamental Q we would need to know where your metal falls in the periodic table (to deal with allowing/annealing) and your magic system. Can you edit this to meet all these expectations?
$endgroup$
– JBH
Jun 5 at 19:32
$begingroup$
If (for instance) said sword could build electric energy would it ever actually hit anything or could it just shoot a bolt of electricity, leaving the blade unharmed?
$endgroup$
– A Writer
Jun 5 at 19:33
$begingroup$
Comments are not for extended discussion; this conversation has been moved to chat.
$endgroup$
– James♦
Jun 4 at 20:47
$begingroup$
Comments are not for extended discussion; this conversation has been moved to chat.
$endgroup$
– James♦
Jun 4 at 20:47
$begingroup$
The help center states, "To prevent your question from being flagged and possibly removed, avoid asking subjective questions where … your answer is provided along with the question, and you expect more answers." SE is not a discussion forum. SE's Q&A model is one-specific-question/one-best-answer. To answer the fundamental Q we would need to know where your metal falls in the periodic table (to deal with allowing/annealing) and your magic system. Can you edit this to meet all these expectations?
$endgroup$
– JBH
Jun 5 at 19:32
$begingroup$
The help center states, "To prevent your question from being flagged and possibly removed, avoid asking subjective questions where … your answer is provided along with the question, and you expect more answers." SE is not a discussion forum. SE's Q&A model is one-specific-question/one-best-answer. To answer the fundamental Q we would need to know where your metal falls in the periodic table (to deal with allowing/annealing) and your magic system. Can you edit this to meet all these expectations?
$endgroup$
– JBH
Jun 5 at 19:32
$begingroup$
If (for instance) said sword could build electric energy would it ever actually hit anything or could it just shoot a bolt of electricity, leaving the blade unharmed?
$endgroup$
– A Writer
Jun 5 at 19:33
$begingroup$
If (for instance) said sword could build electric energy would it ever actually hit anything or could it just shoot a bolt of electricity, leaving the blade unharmed?
$endgroup$
– A Writer
Jun 5 at 19:33
add a comment |
7 Answers
7
active
oldest
votes
$begingroup$
You may wish to look at inlays. Instead of alloying the materials, merely have a pocket cut out where you put the spectral metals.
In the real world, we have variable tempered blades. These are blades which are tempered such that the edge of the blade is very hard (and brittle), while the body of the sword is more flexible. This allows a blade to flex while still holding a very sharp edge.
However, you specifically mention that these spectral metals can take less stress than their mundane equivalents in every way. In the above example of variable tempers, the edge is hard, capable of taking great stress before chipping away. If the edge crumbles at lower stresses, it will never be an effective sword. The first time you use the blade, you'll end up damaging it.
So as an alternative, consider inlaying a small section of the edge with the spectral metals of choice. When fighting normally, you simply avoid using that particular section of the blade. When you need its particular behaviors, then you use it.
Also consider that some of your spectral metals don't even need to be on the edge. While the edge does the cutting, the sides of the blade do touch the target. If you attacked a faerie with a sword which was all steel except for a thin ridge 1/4" from the edge made of inlaid spectral iron, you'd certainly set them on fire, but you wouldn't have to sacrifice the hardness of your edge to do so. Spectral copper might be inlaid in circles near the back side of the blade, generating electric charges from there which flow through the steel.
$endgroup$
8
$begingroup$
I think there's a lot of room for creative answers. one is definitely forge welding them, which is a tremendously skillful technique which fuses one metal to another at the molecular level (I never did get a forge weld successfully). Another option may be to heat the sword up so that it grows a bit, inlay the material, and then let it shrink. Or, depending on the spectral metal itself, you might be able to physically pound it into position like we do with rivets.
$endgroup$
– Cort Ammon
Jun 4 at 6:14
7
$begingroup$
When it comes to weaponry, the answers really are endless. The Chinese have a broad sword that has nine rings attached to it. They use those rings for many things, such as capturing the opponent's weapons. Each of those rings could be spectral.
$endgroup$
– Cort Ammon
Jun 4 at 6:20
2
$begingroup$
For many combinations you could cut a groove in mundane steel and melt the spectral metal in there. Spectral steel could be brazed onto mundane. Perhaps a two-edged sword would be in order: mundane on one edge, spectral on the back
$endgroup$
– Chris H
Jun 4 at 15:13
2
$begingroup$
Forge welding is really hard work...and I wouldn't recommend trying to forge weld two vastly different metals...the heat required to forge weld steel is white hot...or like...1600 degrees, copper at that temp is liquefied and vaporized.
$endgroup$
– James♦
Jun 4 at 20:50
1
$begingroup$
@ChrisH -- this sort of thing reminds me of how carbide tools are made, with a cemented-carbide tip brazed to a steel backer...
$endgroup$
– Shalvenay
Jun 5 at 11:43
|
show 3 more comments
$begingroup$
Pattern welding
You start with three (or more) rods of different metals. You lay them side by side, with the softest in the middle and the hardest, most brittle on the outside; then heat them, fold them into a spiral and beat them flat. Heat, fold, and beat again; repeat until the metals blend together.
This method was used by the Vikings (among others) to make swords with a hard, sharp (but brittle) edge and a soft, elastic core, with a gradual transition from hard to soft.
Here is a tutorial about how to make a pattern welded sword.
$endgroup$
5
$begingroup$
This is what I came here to suggest, pattern welds can be made with surprisingly dissimilar metals as well, see Mokume-gane.
$endgroup$
– Ash
Jun 4 at 13:52
$begingroup$
I believe when metal is folded repeatedly like this, the different layers exist all through the metal, and so the inside and outside have similar properties. To get an elastic core and a harder outer, you'd need to forge weld the inner to the outer –typically just along the blade, with no folding.
$endgroup$
– Dan W
Jun 5 at 13:23
$begingroup$
@DanW: According to Wikipedia, "By the 6th and 7th centuries, pattern welding had reached a level where thin layers of patterned steel were being overlaid onto a soft iron core, making the swords far better as the iron gave them a flexible and springy core that would take any shock from sword blows to stop the blade bending or snapping."
$endgroup$
– Klaus Æ. Mogensen
Jun 6 at 7:33
$begingroup$
@KlausÆ.Mogensen - but it’s the overlaying, not the pattern welding, which gives the flexible core and hard outer. You can do the same by overlaying with tool steel.
$endgroup$
– Dan W
Jun 6 at 7:36
$begingroup$
@DanW: The article and sentence are specifically about pattern welding, so I will stand by my answer.
$endgroup$
– Klaus Æ. Mogensen
Jun 6 at 8:02
add a comment |
$begingroup$
It's actually remarkably simple to join two pieces of metal together for these purposes.
You place the metal parts together and hit them with a hammer until they join.
You're joking, it can't be that simple!
These days we have fancy names like cold pressure welding, and use machines that do it more efficiently, but in practice it's what blacksmiths have been doing for centuries. You can heat it up first which makes it easier, certainly since you're dealing with iron you'll want to heat it first for forge welding, but then you hit it with a hammer until it welds.
If you're wondering about availability of forge welding, any blacksmith would be able to do it. It's a fundamental aspect of their craft.
$endgroup$
$begingroup$
Its still alot of really hard work to do by hand.
$endgroup$
– James♦
Jun 4 at 20:51
2
$begingroup$
@James: If we're talking swords, we're talking medieval, and if we're talking medieval, apprentices are almost literally a a dime a dozen. Manpower is just not a problem.
$endgroup$
– Williham Totland
Jun 4 at 21:06
1
$begingroup$
It's hard work to do by hand in the 21st century mentality, where you swipe a credit card for food. Back then, if you don't wake up at 5 am in the morning to farm, you're not eating.
$endgroup$
– Nelson
Jun 5 at 1:21
1
$begingroup$
@Nelson, even in period it's a hard, skilled, job. I make light of it here, but the blacksmith was one of the wealthiest and most important people in the village.
$endgroup$
– Separatrix
Jun 5 at 7:04
$begingroup$
Just hitting a piece of metal will not cause it to pressure weld nor are cold welds very strong. More importantly hammering cold steel is a great way to destroy a sword not weld it.
$endgroup$
– John
Jun 5 at 10:32
|
show 4 more comments
$begingroup$
The solution would appear to be Electrolysis.
Electrolysis is a common process for plating metal objects with a more valuable metal. For example, Electroplating is a common way of putting gold, silver or nickel over the top of another metal. More recently, there appears to be a process which allows for this to be done with Iron.
If you use this process on your sword, there are two distinct advantages;
1) The bulk of your sword gets the benefit of mundane strength without reducing the efficacy of spectral contact on the blade
2) As the plate metal wears, you can always add more through a reapplication of the electroplating process.
You literally get the best of both worlds; you get a sword with all the strength of conventional metal but you also get all the spectral benefits that contact with the blade would imbue. And, you can always freshen up the blade between battles.
$endgroup$
$begingroup$
Huh... neat. I'll look into it. Still for the sake of convenience, may I ask what level of technological infrastructure is required to do this?
$endgroup$
– Globin347
Jun 4 at 5:44
1
$begingroup$
@Globin347 From the linked article, it was released in 1991... You could probably push it a couple decades earlier, but it might not work unless you can have the metal in an Ion form (and you are already using alloys).
$endgroup$
– Shadowzee
Jun 4 at 5:47
2
$begingroup$
@Globin347 Well, the first ever case of it was documented in 1785, nearly 100 years before the Maxwell equations integrated magnetism and electricity as a single fundamental force. So, I'd imagine that you could almost do it with medieval tech but I'd need to do more research to confirm
$endgroup$
– Tim B II
Jun 4 at 5:48
1
$begingroup$
I should probably mention- As far as I know, an alloy is just melting down two metals and mixing them together. Like I said, I'm not great with metallurgy.
$endgroup$
– Globin347
Jun 4 at 5:50
3
$begingroup$
@Globin347 you already have a source of electricity from your spectral copper which would made things like electroplating viable on a much earlier tech base
$endgroup$
– mgh42
Jun 4 at 23:08
|
show 1 more comment
$begingroup$
Differential Spectrality
In bladesmithing, there is a technique called differential hardening. This simply means that different parts of the blade are cooled at different rates. This creates different types of steel with different properties.
The Japanese achieved this by coating parts of their katana blades with clay before tempering them. This meant that the edge cooled slower, making it harder and more suitable for holding an edge, where as the back cooled quicker and was softer, meaning if the edge chipped (as the edge is very hard and prone to damage), a crack wouldn’t form across the whole blade and cause it to break in two. (As a side note, this is why the katana curves, the back cooling faster than the edge means the steel is pulled back. If you wanted your blade to be straight, you would make it curved forwards before tempering so, when it bent back, it would be straight.)
Applying this to your question, your swords may undergo ‘differential spectrality’ where the edge of the blade is made to be more spectral than the back of the blade. The entire blade might initially be made of the same metal, such as steel, but you coat the back of the blade in, lets say, clay. This mean when you make the metal spectral, only the edge is spectral, the back of it is still very mundane as the clay prevented the spectral energy infusing the metal underneath it. Once it has finished undergoing the process, you would have a blade with a mundane steel back with a spectral steel edge.
$endgroup$
2
$begingroup$
This is a neat idea... unfortunately, It's extremely difficult to "make" the metal spectral. Typically, spectral metal is found, not made. It can be diluted by melting it with conventional metal, however, and if I find a way to spectralize metal, I'll keep this in mind.
$endgroup$
– Globin347
Jun 4 at 14:37
$begingroup$
@Globin347 Ah well, never mind then. Still, as you say, its something you can keep in mind if your scientists ever discover a way to artificially recreate spectral metal. (Perhaps artificial spectral metal has slightly different properties than its true counterpart? Though thats another question for another time).
$endgroup$
– Liam Morris
Jun 4 at 16:20
add a comment |
$begingroup$
One technique you could use is a bastardization of the San Mai technique.
Simply, San Mai is a technique that builds off forge welding - heat multiple pieces of metal up and apply pressure (hammer) until they become one solid piece. This is how one makes damascus or pattern-welded steel - Forge weld several layers of different steels together, cut in in half or fold it or twist it (whatever) and keep doing that a few times to get a really interesting pattern.
San Mai is a variation on that that's more simple to grasp - you effectively take one steel, fold it into a taco shape, and inset another steel as the "meat" of the taco. Then proceed to forge weld those two pieces together (but you don't add extra steps - no folding, twisting, etc). Typically that'd be used to have a hard steel edge and core, with a much softer steel case to better absorb the shocks (the softer steel is literally less harden-able, so you don't have to worry about differential heating as much, just get the whole piece to heat and quench the whole thing).
What I'd imagine as your "masterwork" case would be some variation on this. Where you first make a billet that has the spectral properties you want, and then do a San Mai on it to strengthen it. An example:
You want a sword to be good against both fairies and werewolves, so you want both spectral iron and silver; but it should still be effective against people so we still need a hard steel edge. We start with three mostly-flat billets (one of each). Stack them Spectral - Steel - Spectral; and forge weld that. So now we have a single sandwich billet where the core is hard steel and each side is the less-strong spectral metals. Flatten that enough to be the blade. Then we make our taco out of softer steel (to better absorb the blows), and inlay the other billet such that it still sticks out a fair amount. Forge weld that together, and grind down the blade and harden/temper the construction.
You now have a blade where the cutting edge is hard steel, and flanking that are your two varieties of spectral metals. On a solid chop or a stab, you'd get contact on all 3 metals; but most of initial impact shock should be absorbed by the hard steel and the soft shell. Super effective if you don't need the spectral metal to be the one material penetrating.
If you do need that, you could still use the san mai technique, but rather than forging one sandwich, you could instead use different metals at different chunks of the edge. I.e. forge weld a few billets end-to-end so you have a very long billet that's e.g. Spectral silver for the first 6 inches followed by 2 feet of steel. Put that right in the soft taco. Forge as needed, and you end up with a blade that has 6 inches (either at the tip or the base) that's less durable, but super-effective. May work especially well for forging axes - a few inches in the beard inset for werewolf-killing, but the main belly of the chopping edge in hardened steel.
$endgroup$
$begingroup$
Came here to say a san mai would be the approach I would go for. Leaves the core 'magical' metal in one piece with the edge exposed, but allowing the strength of the 'normal' metal
$endgroup$
– Randomhero
Jun 5 at 10:20
add a comment |
$begingroup$
Don't make a sword.
Make a bludgeoning weapon instead, like a mace or a banded wooden club. Brittleness will be less of an issue.
If you really want a sword, there are those whose blade are heavy and not really sharp at all. They're designed to break armor; I refer to them as "aerodynamic clubs." Again, brittleness isn't an issue.
If you want to get really fancy, make one edge sharp (for nonmagical opponents) and the other non-sharp (for fairy werewolves). You need special fighting techniques for this, or at least be able to flip your grip in a hurry.
$endgroup$
$begingroup$
I like your last suggestion of one sharp edge and one special edge
$endgroup$
– Cullub
Jun 5 at 11:22
add a comment |
7 Answers
7
active
oldest
votes
7 Answers
7
active
oldest
votes
active
oldest
votes
active
oldest
votes
$begingroup$
You may wish to look at inlays. Instead of alloying the materials, merely have a pocket cut out where you put the spectral metals.
In the real world, we have variable tempered blades. These are blades which are tempered such that the edge of the blade is very hard (and brittle), while the body of the sword is more flexible. This allows a blade to flex while still holding a very sharp edge.
However, you specifically mention that these spectral metals can take less stress than their mundane equivalents in every way. In the above example of variable tempers, the edge is hard, capable of taking great stress before chipping away. If the edge crumbles at lower stresses, it will never be an effective sword. The first time you use the blade, you'll end up damaging it.
So as an alternative, consider inlaying a small section of the edge with the spectral metals of choice. When fighting normally, you simply avoid using that particular section of the blade. When you need its particular behaviors, then you use it.
Also consider that some of your spectral metals don't even need to be on the edge. While the edge does the cutting, the sides of the blade do touch the target. If you attacked a faerie with a sword which was all steel except for a thin ridge 1/4" from the edge made of inlaid spectral iron, you'd certainly set them on fire, but you wouldn't have to sacrifice the hardness of your edge to do so. Spectral copper might be inlaid in circles near the back side of the blade, generating electric charges from there which flow through the steel.
$endgroup$
8
$begingroup$
I think there's a lot of room for creative answers. one is definitely forge welding them, which is a tremendously skillful technique which fuses one metal to another at the molecular level (I never did get a forge weld successfully). Another option may be to heat the sword up so that it grows a bit, inlay the material, and then let it shrink. Or, depending on the spectral metal itself, you might be able to physically pound it into position like we do with rivets.
$endgroup$
– Cort Ammon
Jun 4 at 6:14
7
$begingroup$
When it comes to weaponry, the answers really are endless. The Chinese have a broad sword that has nine rings attached to it. They use those rings for many things, such as capturing the opponent's weapons. Each of those rings could be spectral.
$endgroup$
– Cort Ammon
Jun 4 at 6:20
2
$begingroup$
For many combinations you could cut a groove in mundane steel and melt the spectral metal in there. Spectral steel could be brazed onto mundane. Perhaps a two-edged sword would be in order: mundane on one edge, spectral on the back
$endgroup$
– Chris H
Jun 4 at 15:13
2
$begingroup$
Forge welding is really hard work...and I wouldn't recommend trying to forge weld two vastly different metals...the heat required to forge weld steel is white hot...or like...1600 degrees, copper at that temp is liquefied and vaporized.
$endgroup$
– James♦
Jun 4 at 20:50
1
$begingroup$
@ChrisH -- this sort of thing reminds me of how carbide tools are made, with a cemented-carbide tip brazed to a steel backer...
$endgroup$
– Shalvenay
Jun 5 at 11:43
|
show 3 more comments
$begingroup$
You may wish to look at inlays. Instead of alloying the materials, merely have a pocket cut out where you put the spectral metals.
In the real world, we have variable tempered blades. These are blades which are tempered such that the edge of the blade is very hard (and brittle), while the body of the sword is more flexible. This allows a blade to flex while still holding a very sharp edge.
However, you specifically mention that these spectral metals can take less stress than their mundane equivalents in every way. In the above example of variable tempers, the edge is hard, capable of taking great stress before chipping away. If the edge crumbles at lower stresses, it will never be an effective sword. The first time you use the blade, you'll end up damaging it.
So as an alternative, consider inlaying a small section of the edge with the spectral metals of choice. When fighting normally, you simply avoid using that particular section of the blade. When you need its particular behaviors, then you use it.
Also consider that some of your spectral metals don't even need to be on the edge. While the edge does the cutting, the sides of the blade do touch the target. If you attacked a faerie with a sword which was all steel except for a thin ridge 1/4" from the edge made of inlaid spectral iron, you'd certainly set them on fire, but you wouldn't have to sacrifice the hardness of your edge to do so. Spectral copper might be inlaid in circles near the back side of the blade, generating electric charges from there which flow through the steel.
$endgroup$
8
$begingroup$
I think there's a lot of room for creative answers. one is definitely forge welding them, which is a tremendously skillful technique which fuses one metal to another at the molecular level (I never did get a forge weld successfully). Another option may be to heat the sword up so that it grows a bit, inlay the material, and then let it shrink. Or, depending on the spectral metal itself, you might be able to physically pound it into position like we do with rivets.
$endgroup$
– Cort Ammon
Jun 4 at 6:14
7
$begingroup$
When it comes to weaponry, the answers really are endless. The Chinese have a broad sword that has nine rings attached to it. They use those rings for many things, such as capturing the opponent's weapons. Each of those rings could be spectral.
$endgroup$
– Cort Ammon
Jun 4 at 6:20
2
$begingroup$
For many combinations you could cut a groove in mundane steel and melt the spectral metal in there. Spectral steel could be brazed onto mundane. Perhaps a two-edged sword would be in order: mundane on one edge, spectral on the back
$endgroup$
– Chris H
Jun 4 at 15:13
2
$begingroup$
Forge welding is really hard work...and I wouldn't recommend trying to forge weld two vastly different metals...the heat required to forge weld steel is white hot...or like...1600 degrees, copper at that temp is liquefied and vaporized.
$endgroup$
– James♦
Jun 4 at 20:50
1
$begingroup$
@ChrisH -- this sort of thing reminds me of how carbide tools are made, with a cemented-carbide tip brazed to a steel backer...
$endgroup$
– Shalvenay
Jun 5 at 11:43
|
show 3 more comments
$begingroup$
You may wish to look at inlays. Instead of alloying the materials, merely have a pocket cut out where you put the spectral metals.
In the real world, we have variable tempered blades. These are blades which are tempered such that the edge of the blade is very hard (and brittle), while the body of the sword is more flexible. This allows a blade to flex while still holding a very sharp edge.
However, you specifically mention that these spectral metals can take less stress than their mundane equivalents in every way. In the above example of variable tempers, the edge is hard, capable of taking great stress before chipping away. If the edge crumbles at lower stresses, it will never be an effective sword. The first time you use the blade, you'll end up damaging it.
So as an alternative, consider inlaying a small section of the edge with the spectral metals of choice. When fighting normally, you simply avoid using that particular section of the blade. When you need its particular behaviors, then you use it.
Also consider that some of your spectral metals don't even need to be on the edge. While the edge does the cutting, the sides of the blade do touch the target. If you attacked a faerie with a sword which was all steel except for a thin ridge 1/4" from the edge made of inlaid spectral iron, you'd certainly set them on fire, but you wouldn't have to sacrifice the hardness of your edge to do so. Spectral copper might be inlaid in circles near the back side of the blade, generating electric charges from there which flow through the steel.
$endgroup$
You may wish to look at inlays. Instead of alloying the materials, merely have a pocket cut out where you put the spectral metals.
In the real world, we have variable tempered blades. These are blades which are tempered such that the edge of the blade is very hard (and brittle), while the body of the sword is more flexible. This allows a blade to flex while still holding a very sharp edge.
However, you specifically mention that these spectral metals can take less stress than their mundane equivalents in every way. In the above example of variable tempers, the edge is hard, capable of taking great stress before chipping away. If the edge crumbles at lower stresses, it will never be an effective sword. The first time you use the blade, you'll end up damaging it.
So as an alternative, consider inlaying a small section of the edge with the spectral metals of choice. When fighting normally, you simply avoid using that particular section of the blade. When you need its particular behaviors, then you use it.
Also consider that some of your spectral metals don't even need to be on the edge. While the edge does the cutting, the sides of the blade do touch the target. If you attacked a faerie with a sword which was all steel except for a thin ridge 1/4" from the edge made of inlaid spectral iron, you'd certainly set them on fire, but you wouldn't have to sacrifice the hardness of your edge to do so. Spectral copper might be inlaid in circles near the back side of the blade, generating electric charges from there which flow through the steel.
answered Jun 4 at 6:09


Cort AmmonCort Ammon
113k18204397
113k18204397
8
$begingroup$
I think there's a lot of room for creative answers. one is definitely forge welding them, which is a tremendously skillful technique which fuses one metal to another at the molecular level (I never did get a forge weld successfully). Another option may be to heat the sword up so that it grows a bit, inlay the material, and then let it shrink. Or, depending on the spectral metal itself, you might be able to physically pound it into position like we do with rivets.
$endgroup$
– Cort Ammon
Jun 4 at 6:14
7
$begingroup$
When it comes to weaponry, the answers really are endless. The Chinese have a broad sword that has nine rings attached to it. They use those rings for many things, such as capturing the opponent's weapons. Each of those rings could be spectral.
$endgroup$
– Cort Ammon
Jun 4 at 6:20
2
$begingroup$
For many combinations you could cut a groove in mundane steel and melt the spectral metal in there. Spectral steel could be brazed onto mundane. Perhaps a two-edged sword would be in order: mundane on one edge, spectral on the back
$endgroup$
– Chris H
Jun 4 at 15:13
2
$begingroup$
Forge welding is really hard work...and I wouldn't recommend trying to forge weld two vastly different metals...the heat required to forge weld steel is white hot...or like...1600 degrees, copper at that temp is liquefied and vaporized.
$endgroup$
– James♦
Jun 4 at 20:50
1
$begingroup$
@ChrisH -- this sort of thing reminds me of how carbide tools are made, with a cemented-carbide tip brazed to a steel backer...
$endgroup$
– Shalvenay
Jun 5 at 11:43
|
show 3 more comments
8
$begingroup$
I think there's a lot of room for creative answers. one is definitely forge welding them, which is a tremendously skillful technique which fuses one metal to another at the molecular level (I never did get a forge weld successfully). Another option may be to heat the sword up so that it grows a bit, inlay the material, and then let it shrink. Or, depending on the spectral metal itself, you might be able to physically pound it into position like we do with rivets.
$endgroup$
– Cort Ammon
Jun 4 at 6:14
7
$begingroup$
When it comes to weaponry, the answers really are endless. The Chinese have a broad sword that has nine rings attached to it. They use those rings for many things, such as capturing the opponent's weapons. Each of those rings could be spectral.
$endgroup$
– Cort Ammon
Jun 4 at 6:20
2
$begingroup$
For many combinations you could cut a groove in mundane steel and melt the spectral metal in there. Spectral steel could be brazed onto mundane. Perhaps a two-edged sword would be in order: mundane on one edge, spectral on the back
$endgroup$
– Chris H
Jun 4 at 15:13
2
$begingroup$
Forge welding is really hard work...and I wouldn't recommend trying to forge weld two vastly different metals...the heat required to forge weld steel is white hot...or like...1600 degrees, copper at that temp is liquefied and vaporized.
$endgroup$
– James♦
Jun 4 at 20:50
1
$begingroup$
@ChrisH -- this sort of thing reminds me of how carbide tools are made, with a cemented-carbide tip brazed to a steel backer...
$endgroup$
– Shalvenay
Jun 5 at 11:43
8
8
$begingroup$
I think there's a lot of room for creative answers. one is definitely forge welding them, which is a tremendously skillful technique which fuses one metal to another at the molecular level (I never did get a forge weld successfully). Another option may be to heat the sword up so that it grows a bit, inlay the material, and then let it shrink. Or, depending on the spectral metal itself, you might be able to physically pound it into position like we do with rivets.
$endgroup$
– Cort Ammon
Jun 4 at 6:14
$begingroup$
I think there's a lot of room for creative answers. one is definitely forge welding them, which is a tremendously skillful technique which fuses one metal to another at the molecular level (I never did get a forge weld successfully). Another option may be to heat the sword up so that it grows a bit, inlay the material, and then let it shrink. Or, depending on the spectral metal itself, you might be able to physically pound it into position like we do with rivets.
$endgroup$
– Cort Ammon
Jun 4 at 6:14
7
7
$begingroup$
When it comes to weaponry, the answers really are endless. The Chinese have a broad sword that has nine rings attached to it. They use those rings for many things, such as capturing the opponent's weapons. Each of those rings could be spectral.
$endgroup$
– Cort Ammon
Jun 4 at 6:20
$begingroup$
When it comes to weaponry, the answers really are endless. The Chinese have a broad sword that has nine rings attached to it. They use those rings for many things, such as capturing the opponent's weapons. Each of those rings could be spectral.
$endgroup$
– Cort Ammon
Jun 4 at 6:20
2
2
$begingroup$
For many combinations you could cut a groove in mundane steel and melt the spectral metal in there. Spectral steel could be brazed onto mundane. Perhaps a two-edged sword would be in order: mundane on one edge, spectral on the back
$endgroup$
– Chris H
Jun 4 at 15:13
$begingroup$
For many combinations you could cut a groove in mundane steel and melt the spectral metal in there. Spectral steel could be brazed onto mundane. Perhaps a two-edged sword would be in order: mundane on one edge, spectral on the back
$endgroup$
– Chris H
Jun 4 at 15:13
2
2
$begingroup$
Forge welding is really hard work...and I wouldn't recommend trying to forge weld two vastly different metals...the heat required to forge weld steel is white hot...or like...1600 degrees, copper at that temp is liquefied and vaporized.
$endgroup$
– James♦
Jun 4 at 20:50
$begingroup$
Forge welding is really hard work...and I wouldn't recommend trying to forge weld two vastly different metals...the heat required to forge weld steel is white hot...or like...1600 degrees, copper at that temp is liquefied and vaporized.
$endgroup$
– James♦
Jun 4 at 20:50
1
1
$begingroup$
@ChrisH -- this sort of thing reminds me of how carbide tools are made, with a cemented-carbide tip brazed to a steel backer...
$endgroup$
– Shalvenay
Jun 5 at 11:43
$begingroup$
@ChrisH -- this sort of thing reminds me of how carbide tools are made, with a cemented-carbide tip brazed to a steel backer...
$endgroup$
– Shalvenay
Jun 5 at 11:43
|
show 3 more comments
$begingroup$
Pattern welding
You start with three (or more) rods of different metals. You lay them side by side, with the softest in the middle and the hardest, most brittle on the outside; then heat them, fold them into a spiral and beat them flat. Heat, fold, and beat again; repeat until the metals blend together.
This method was used by the Vikings (among others) to make swords with a hard, sharp (but brittle) edge and a soft, elastic core, with a gradual transition from hard to soft.
Here is a tutorial about how to make a pattern welded sword.
$endgroup$
5
$begingroup$
This is what I came here to suggest, pattern welds can be made with surprisingly dissimilar metals as well, see Mokume-gane.
$endgroup$
– Ash
Jun 4 at 13:52
$begingroup$
I believe when metal is folded repeatedly like this, the different layers exist all through the metal, and so the inside and outside have similar properties. To get an elastic core and a harder outer, you'd need to forge weld the inner to the outer –typically just along the blade, with no folding.
$endgroup$
– Dan W
Jun 5 at 13:23
$begingroup$
@DanW: According to Wikipedia, "By the 6th and 7th centuries, pattern welding had reached a level where thin layers of patterned steel were being overlaid onto a soft iron core, making the swords far better as the iron gave them a flexible and springy core that would take any shock from sword blows to stop the blade bending or snapping."
$endgroup$
– Klaus Æ. Mogensen
Jun 6 at 7:33
$begingroup$
@KlausÆ.Mogensen - but it’s the overlaying, not the pattern welding, which gives the flexible core and hard outer. You can do the same by overlaying with tool steel.
$endgroup$
– Dan W
Jun 6 at 7:36
$begingroup$
@DanW: The article and sentence are specifically about pattern welding, so I will stand by my answer.
$endgroup$
– Klaus Æ. Mogensen
Jun 6 at 8:02
add a comment |
$begingroup$
Pattern welding
You start with three (or more) rods of different metals. You lay them side by side, with the softest in the middle and the hardest, most brittle on the outside; then heat them, fold them into a spiral and beat them flat. Heat, fold, and beat again; repeat until the metals blend together.
This method was used by the Vikings (among others) to make swords with a hard, sharp (but brittle) edge and a soft, elastic core, with a gradual transition from hard to soft.
Here is a tutorial about how to make a pattern welded sword.
$endgroup$
5
$begingroup$
This is what I came here to suggest, pattern welds can be made with surprisingly dissimilar metals as well, see Mokume-gane.
$endgroup$
– Ash
Jun 4 at 13:52
$begingroup$
I believe when metal is folded repeatedly like this, the different layers exist all through the metal, and so the inside and outside have similar properties. To get an elastic core and a harder outer, you'd need to forge weld the inner to the outer –typically just along the blade, with no folding.
$endgroup$
– Dan W
Jun 5 at 13:23
$begingroup$
@DanW: According to Wikipedia, "By the 6th and 7th centuries, pattern welding had reached a level where thin layers of patterned steel were being overlaid onto a soft iron core, making the swords far better as the iron gave them a flexible and springy core that would take any shock from sword blows to stop the blade bending or snapping."
$endgroup$
– Klaus Æ. Mogensen
Jun 6 at 7:33
$begingroup$
@KlausÆ.Mogensen - but it’s the overlaying, not the pattern welding, which gives the flexible core and hard outer. You can do the same by overlaying with tool steel.
$endgroup$
– Dan W
Jun 6 at 7:36
$begingroup$
@DanW: The article and sentence are specifically about pattern welding, so I will stand by my answer.
$endgroup$
– Klaus Æ. Mogensen
Jun 6 at 8:02
add a comment |
$begingroup$
Pattern welding
You start with three (or more) rods of different metals. You lay them side by side, with the softest in the middle and the hardest, most brittle on the outside; then heat them, fold them into a spiral and beat them flat. Heat, fold, and beat again; repeat until the metals blend together.
This method was used by the Vikings (among others) to make swords with a hard, sharp (but brittle) edge and a soft, elastic core, with a gradual transition from hard to soft.
Here is a tutorial about how to make a pattern welded sword.
$endgroup$
Pattern welding
You start with three (or more) rods of different metals. You lay them side by side, with the softest in the middle and the hardest, most brittle on the outside; then heat them, fold them into a spiral and beat them flat. Heat, fold, and beat again; repeat until the metals blend together.
This method was used by the Vikings (among others) to make swords with a hard, sharp (but brittle) edge and a soft, elastic core, with a gradual transition from hard to soft.
Here is a tutorial about how to make a pattern welded sword.
answered Jun 4 at 7:51


Klaus Æ. MogensenKlaus Æ. Mogensen
4,0711718
4,0711718
5
$begingroup$
This is what I came here to suggest, pattern welds can be made with surprisingly dissimilar metals as well, see Mokume-gane.
$endgroup$
– Ash
Jun 4 at 13:52
$begingroup$
I believe when metal is folded repeatedly like this, the different layers exist all through the metal, and so the inside and outside have similar properties. To get an elastic core and a harder outer, you'd need to forge weld the inner to the outer –typically just along the blade, with no folding.
$endgroup$
– Dan W
Jun 5 at 13:23
$begingroup$
@DanW: According to Wikipedia, "By the 6th and 7th centuries, pattern welding had reached a level where thin layers of patterned steel were being overlaid onto a soft iron core, making the swords far better as the iron gave them a flexible and springy core that would take any shock from sword blows to stop the blade bending or snapping."
$endgroup$
– Klaus Æ. Mogensen
Jun 6 at 7:33
$begingroup$
@KlausÆ.Mogensen - but it’s the overlaying, not the pattern welding, which gives the flexible core and hard outer. You can do the same by overlaying with tool steel.
$endgroup$
– Dan W
Jun 6 at 7:36
$begingroup$
@DanW: The article and sentence are specifically about pattern welding, so I will stand by my answer.
$endgroup$
– Klaus Æ. Mogensen
Jun 6 at 8:02
add a comment |
5
$begingroup$
This is what I came here to suggest, pattern welds can be made with surprisingly dissimilar metals as well, see Mokume-gane.
$endgroup$
– Ash
Jun 4 at 13:52
$begingroup$
I believe when metal is folded repeatedly like this, the different layers exist all through the metal, and so the inside and outside have similar properties. To get an elastic core and a harder outer, you'd need to forge weld the inner to the outer –typically just along the blade, with no folding.
$endgroup$
– Dan W
Jun 5 at 13:23
$begingroup$
@DanW: According to Wikipedia, "By the 6th and 7th centuries, pattern welding had reached a level where thin layers of patterned steel were being overlaid onto a soft iron core, making the swords far better as the iron gave them a flexible and springy core that would take any shock from sword blows to stop the blade bending or snapping."
$endgroup$
– Klaus Æ. Mogensen
Jun 6 at 7:33
$begingroup$
@KlausÆ.Mogensen - but it’s the overlaying, not the pattern welding, which gives the flexible core and hard outer. You can do the same by overlaying with tool steel.
$endgroup$
– Dan W
Jun 6 at 7:36
$begingroup$
@DanW: The article and sentence are specifically about pattern welding, so I will stand by my answer.
$endgroup$
– Klaus Æ. Mogensen
Jun 6 at 8:02
5
5
$begingroup$
This is what I came here to suggest, pattern welds can be made with surprisingly dissimilar metals as well, see Mokume-gane.
$endgroup$
– Ash
Jun 4 at 13:52
$begingroup$
This is what I came here to suggest, pattern welds can be made with surprisingly dissimilar metals as well, see Mokume-gane.
$endgroup$
– Ash
Jun 4 at 13:52
$begingroup$
I believe when metal is folded repeatedly like this, the different layers exist all through the metal, and so the inside and outside have similar properties. To get an elastic core and a harder outer, you'd need to forge weld the inner to the outer –typically just along the blade, with no folding.
$endgroup$
– Dan W
Jun 5 at 13:23
$begingroup$
I believe when metal is folded repeatedly like this, the different layers exist all through the metal, and so the inside and outside have similar properties. To get an elastic core and a harder outer, you'd need to forge weld the inner to the outer –typically just along the blade, with no folding.
$endgroup$
– Dan W
Jun 5 at 13:23
$begingroup$
@DanW: According to Wikipedia, "By the 6th and 7th centuries, pattern welding had reached a level where thin layers of patterned steel were being overlaid onto a soft iron core, making the swords far better as the iron gave them a flexible and springy core that would take any shock from sword blows to stop the blade bending or snapping."
$endgroup$
– Klaus Æ. Mogensen
Jun 6 at 7:33
$begingroup$
@DanW: According to Wikipedia, "By the 6th and 7th centuries, pattern welding had reached a level where thin layers of patterned steel were being overlaid onto a soft iron core, making the swords far better as the iron gave them a flexible and springy core that would take any shock from sword blows to stop the blade bending or snapping."
$endgroup$
– Klaus Æ. Mogensen
Jun 6 at 7:33
$begingroup$
@KlausÆ.Mogensen - but it’s the overlaying, not the pattern welding, which gives the flexible core and hard outer. You can do the same by overlaying with tool steel.
$endgroup$
– Dan W
Jun 6 at 7:36
$begingroup$
@KlausÆ.Mogensen - but it’s the overlaying, not the pattern welding, which gives the flexible core and hard outer. You can do the same by overlaying with tool steel.
$endgroup$
– Dan W
Jun 6 at 7:36
$begingroup$
@DanW: The article and sentence are specifically about pattern welding, so I will stand by my answer.
$endgroup$
– Klaus Æ. Mogensen
Jun 6 at 8:02
$begingroup$
@DanW: The article and sentence are specifically about pattern welding, so I will stand by my answer.
$endgroup$
– Klaus Æ. Mogensen
Jun 6 at 8:02
add a comment |
$begingroup$
It's actually remarkably simple to join two pieces of metal together for these purposes.
You place the metal parts together and hit them with a hammer until they join.
You're joking, it can't be that simple!
These days we have fancy names like cold pressure welding, and use machines that do it more efficiently, but in practice it's what blacksmiths have been doing for centuries. You can heat it up first which makes it easier, certainly since you're dealing with iron you'll want to heat it first for forge welding, but then you hit it with a hammer until it welds.
If you're wondering about availability of forge welding, any blacksmith would be able to do it. It's a fundamental aspect of their craft.
$endgroup$
$begingroup$
Its still alot of really hard work to do by hand.
$endgroup$
– James♦
Jun 4 at 20:51
2
$begingroup$
@James: If we're talking swords, we're talking medieval, and if we're talking medieval, apprentices are almost literally a a dime a dozen. Manpower is just not a problem.
$endgroup$
– Williham Totland
Jun 4 at 21:06
1
$begingroup$
It's hard work to do by hand in the 21st century mentality, where you swipe a credit card for food. Back then, if you don't wake up at 5 am in the morning to farm, you're not eating.
$endgroup$
– Nelson
Jun 5 at 1:21
1
$begingroup$
@Nelson, even in period it's a hard, skilled, job. I make light of it here, but the blacksmith was one of the wealthiest and most important people in the village.
$endgroup$
– Separatrix
Jun 5 at 7:04
$begingroup$
Just hitting a piece of metal will not cause it to pressure weld nor are cold welds very strong. More importantly hammering cold steel is a great way to destroy a sword not weld it.
$endgroup$
– John
Jun 5 at 10:32
|
show 4 more comments
$begingroup$
It's actually remarkably simple to join two pieces of metal together for these purposes.
You place the metal parts together and hit them with a hammer until they join.
You're joking, it can't be that simple!
These days we have fancy names like cold pressure welding, and use machines that do it more efficiently, but in practice it's what blacksmiths have been doing for centuries. You can heat it up first which makes it easier, certainly since you're dealing with iron you'll want to heat it first for forge welding, but then you hit it with a hammer until it welds.
If you're wondering about availability of forge welding, any blacksmith would be able to do it. It's a fundamental aspect of their craft.
$endgroup$
$begingroup$
Its still alot of really hard work to do by hand.
$endgroup$
– James♦
Jun 4 at 20:51
2
$begingroup$
@James: If we're talking swords, we're talking medieval, and if we're talking medieval, apprentices are almost literally a a dime a dozen. Manpower is just not a problem.
$endgroup$
– Williham Totland
Jun 4 at 21:06
1
$begingroup$
It's hard work to do by hand in the 21st century mentality, where you swipe a credit card for food. Back then, if you don't wake up at 5 am in the morning to farm, you're not eating.
$endgroup$
– Nelson
Jun 5 at 1:21
1
$begingroup$
@Nelson, even in period it's a hard, skilled, job. I make light of it here, but the blacksmith was one of the wealthiest and most important people in the village.
$endgroup$
– Separatrix
Jun 5 at 7:04
$begingroup$
Just hitting a piece of metal will not cause it to pressure weld nor are cold welds very strong. More importantly hammering cold steel is a great way to destroy a sword not weld it.
$endgroup$
– John
Jun 5 at 10:32
|
show 4 more comments
$begingroup$
It's actually remarkably simple to join two pieces of metal together for these purposes.
You place the metal parts together and hit them with a hammer until they join.
You're joking, it can't be that simple!
These days we have fancy names like cold pressure welding, and use machines that do it more efficiently, but in practice it's what blacksmiths have been doing for centuries. You can heat it up first which makes it easier, certainly since you're dealing with iron you'll want to heat it first for forge welding, but then you hit it with a hammer until it welds.
If you're wondering about availability of forge welding, any blacksmith would be able to do it. It's a fundamental aspect of their craft.
$endgroup$
It's actually remarkably simple to join two pieces of metal together for these purposes.
You place the metal parts together and hit them with a hammer until they join.
You're joking, it can't be that simple!
These days we have fancy names like cold pressure welding, and use machines that do it more efficiently, but in practice it's what blacksmiths have been doing for centuries. You can heat it up first which makes it easier, certainly since you're dealing with iron you'll want to heat it first for forge welding, but then you hit it with a hammer until it welds.
If you're wondering about availability of forge welding, any blacksmith would be able to do it. It's a fundamental aspect of their craft.
edited Jun 4 at 12:54
answered Jun 4 at 7:03
SeparatrixSeparatrix
88.7k32206343
88.7k32206343
$begingroup$
Its still alot of really hard work to do by hand.
$endgroup$
– James♦
Jun 4 at 20:51
2
$begingroup$
@James: If we're talking swords, we're talking medieval, and if we're talking medieval, apprentices are almost literally a a dime a dozen. Manpower is just not a problem.
$endgroup$
– Williham Totland
Jun 4 at 21:06
1
$begingroup$
It's hard work to do by hand in the 21st century mentality, where you swipe a credit card for food. Back then, if you don't wake up at 5 am in the morning to farm, you're not eating.
$endgroup$
– Nelson
Jun 5 at 1:21
1
$begingroup$
@Nelson, even in period it's a hard, skilled, job. I make light of it here, but the blacksmith was one of the wealthiest and most important people in the village.
$endgroup$
– Separatrix
Jun 5 at 7:04
$begingroup$
Just hitting a piece of metal will not cause it to pressure weld nor are cold welds very strong. More importantly hammering cold steel is a great way to destroy a sword not weld it.
$endgroup$
– John
Jun 5 at 10:32
|
show 4 more comments
$begingroup$
Its still alot of really hard work to do by hand.
$endgroup$
– James♦
Jun 4 at 20:51
2
$begingroup$
@James: If we're talking swords, we're talking medieval, and if we're talking medieval, apprentices are almost literally a a dime a dozen. Manpower is just not a problem.
$endgroup$
– Williham Totland
Jun 4 at 21:06
1
$begingroup$
It's hard work to do by hand in the 21st century mentality, where you swipe a credit card for food. Back then, if you don't wake up at 5 am in the morning to farm, you're not eating.
$endgroup$
– Nelson
Jun 5 at 1:21
1
$begingroup$
@Nelson, even in period it's a hard, skilled, job. I make light of it here, but the blacksmith was one of the wealthiest and most important people in the village.
$endgroup$
– Separatrix
Jun 5 at 7:04
$begingroup$
Just hitting a piece of metal will not cause it to pressure weld nor are cold welds very strong. More importantly hammering cold steel is a great way to destroy a sword not weld it.
$endgroup$
– John
Jun 5 at 10:32
$begingroup$
Its still alot of really hard work to do by hand.
$endgroup$
– James♦
Jun 4 at 20:51
$begingroup$
Its still alot of really hard work to do by hand.
$endgroup$
– James♦
Jun 4 at 20:51
2
2
$begingroup$
@James: If we're talking swords, we're talking medieval, and if we're talking medieval, apprentices are almost literally a a dime a dozen. Manpower is just not a problem.
$endgroup$
– Williham Totland
Jun 4 at 21:06
$begingroup$
@James: If we're talking swords, we're talking medieval, and if we're talking medieval, apprentices are almost literally a a dime a dozen. Manpower is just not a problem.
$endgroup$
– Williham Totland
Jun 4 at 21:06
1
1
$begingroup$
It's hard work to do by hand in the 21st century mentality, where you swipe a credit card for food. Back then, if you don't wake up at 5 am in the morning to farm, you're not eating.
$endgroup$
– Nelson
Jun 5 at 1:21
$begingroup$
It's hard work to do by hand in the 21st century mentality, where you swipe a credit card for food. Back then, if you don't wake up at 5 am in the morning to farm, you're not eating.
$endgroup$
– Nelson
Jun 5 at 1:21
1
1
$begingroup$
@Nelson, even in period it's a hard, skilled, job. I make light of it here, but the blacksmith was one of the wealthiest and most important people in the village.
$endgroup$
– Separatrix
Jun 5 at 7:04
$begingroup$
@Nelson, even in period it's a hard, skilled, job. I make light of it here, but the blacksmith was one of the wealthiest and most important people in the village.
$endgroup$
– Separatrix
Jun 5 at 7:04
$begingroup$
Just hitting a piece of metal will not cause it to pressure weld nor are cold welds very strong. More importantly hammering cold steel is a great way to destroy a sword not weld it.
$endgroup$
– John
Jun 5 at 10:32
$begingroup$
Just hitting a piece of metal will not cause it to pressure weld nor are cold welds very strong. More importantly hammering cold steel is a great way to destroy a sword not weld it.
$endgroup$
– John
Jun 5 at 10:32
|
show 4 more comments
$begingroup$
The solution would appear to be Electrolysis.
Electrolysis is a common process for plating metal objects with a more valuable metal. For example, Electroplating is a common way of putting gold, silver or nickel over the top of another metal. More recently, there appears to be a process which allows for this to be done with Iron.
If you use this process on your sword, there are two distinct advantages;
1) The bulk of your sword gets the benefit of mundane strength without reducing the efficacy of spectral contact on the blade
2) As the plate metal wears, you can always add more through a reapplication of the electroplating process.
You literally get the best of both worlds; you get a sword with all the strength of conventional metal but you also get all the spectral benefits that contact with the blade would imbue. And, you can always freshen up the blade between battles.
$endgroup$
$begingroup$
Huh... neat. I'll look into it. Still for the sake of convenience, may I ask what level of technological infrastructure is required to do this?
$endgroup$
– Globin347
Jun 4 at 5:44
1
$begingroup$
@Globin347 From the linked article, it was released in 1991... You could probably push it a couple decades earlier, but it might not work unless you can have the metal in an Ion form (and you are already using alloys).
$endgroup$
– Shadowzee
Jun 4 at 5:47
2
$begingroup$
@Globin347 Well, the first ever case of it was documented in 1785, nearly 100 years before the Maxwell equations integrated magnetism and electricity as a single fundamental force. So, I'd imagine that you could almost do it with medieval tech but I'd need to do more research to confirm
$endgroup$
– Tim B II
Jun 4 at 5:48
1
$begingroup$
I should probably mention- As far as I know, an alloy is just melting down two metals and mixing them together. Like I said, I'm not great with metallurgy.
$endgroup$
– Globin347
Jun 4 at 5:50
3
$begingroup$
@Globin347 you already have a source of electricity from your spectral copper which would made things like electroplating viable on a much earlier tech base
$endgroup$
– mgh42
Jun 4 at 23:08
|
show 1 more comment
$begingroup$
The solution would appear to be Electrolysis.
Electrolysis is a common process for plating metal objects with a more valuable metal. For example, Electroplating is a common way of putting gold, silver or nickel over the top of another metal. More recently, there appears to be a process which allows for this to be done with Iron.
If you use this process on your sword, there are two distinct advantages;
1) The bulk of your sword gets the benefit of mundane strength without reducing the efficacy of spectral contact on the blade
2) As the plate metal wears, you can always add more through a reapplication of the electroplating process.
You literally get the best of both worlds; you get a sword with all the strength of conventional metal but you also get all the spectral benefits that contact with the blade would imbue. And, you can always freshen up the blade between battles.
$endgroup$
$begingroup$
Huh... neat. I'll look into it. Still for the sake of convenience, may I ask what level of technological infrastructure is required to do this?
$endgroup$
– Globin347
Jun 4 at 5:44
1
$begingroup$
@Globin347 From the linked article, it was released in 1991... You could probably push it a couple decades earlier, but it might not work unless you can have the metal in an Ion form (and you are already using alloys).
$endgroup$
– Shadowzee
Jun 4 at 5:47
2
$begingroup$
@Globin347 Well, the first ever case of it was documented in 1785, nearly 100 years before the Maxwell equations integrated magnetism and electricity as a single fundamental force. So, I'd imagine that you could almost do it with medieval tech but I'd need to do more research to confirm
$endgroup$
– Tim B II
Jun 4 at 5:48
1
$begingroup$
I should probably mention- As far as I know, an alloy is just melting down two metals and mixing them together. Like I said, I'm not great with metallurgy.
$endgroup$
– Globin347
Jun 4 at 5:50
3
$begingroup$
@Globin347 you already have a source of electricity from your spectral copper which would made things like electroplating viable on a much earlier tech base
$endgroup$
– mgh42
Jun 4 at 23:08
|
show 1 more comment
$begingroup$
The solution would appear to be Electrolysis.
Electrolysis is a common process for plating metal objects with a more valuable metal. For example, Electroplating is a common way of putting gold, silver or nickel over the top of another metal. More recently, there appears to be a process which allows for this to be done with Iron.
If you use this process on your sword, there are two distinct advantages;
1) The bulk of your sword gets the benefit of mundane strength without reducing the efficacy of spectral contact on the blade
2) As the plate metal wears, you can always add more through a reapplication of the electroplating process.
You literally get the best of both worlds; you get a sword with all the strength of conventional metal but you also get all the spectral benefits that contact with the blade would imbue. And, you can always freshen up the blade between battles.
$endgroup$
The solution would appear to be Electrolysis.
Electrolysis is a common process for plating metal objects with a more valuable metal. For example, Electroplating is a common way of putting gold, silver or nickel over the top of another metal. More recently, there appears to be a process which allows for this to be done with Iron.
If you use this process on your sword, there are two distinct advantages;
1) The bulk of your sword gets the benefit of mundane strength without reducing the efficacy of spectral contact on the blade
2) As the plate metal wears, you can always add more through a reapplication of the electroplating process.
You literally get the best of both worlds; you get a sword with all the strength of conventional metal but you also get all the spectral benefits that contact with the blade would imbue. And, you can always freshen up the blade between battles.
answered Jun 4 at 5:42
Tim B IITim B II
36.3k679141
36.3k679141
$begingroup$
Huh... neat. I'll look into it. Still for the sake of convenience, may I ask what level of technological infrastructure is required to do this?
$endgroup$
– Globin347
Jun 4 at 5:44
1
$begingroup$
@Globin347 From the linked article, it was released in 1991... You could probably push it a couple decades earlier, but it might not work unless you can have the metal in an Ion form (and you are already using alloys).
$endgroup$
– Shadowzee
Jun 4 at 5:47
2
$begingroup$
@Globin347 Well, the first ever case of it was documented in 1785, nearly 100 years before the Maxwell equations integrated magnetism and electricity as a single fundamental force. So, I'd imagine that you could almost do it with medieval tech but I'd need to do more research to confirm
$endgroup$
– Tim B II
Jun 4 at 5:48
1
$begingroup$
I should probably mention- As far as I know, an alloy is just melting down two metals and mixing them together. Like I said, I'm not great with metallurgy.
$endgroup$
– Globin347
Jun 4 at 5:50
3
$begingroup$
@Globin347 you already have a source of electricity from your spectral copper which would made things like electroplating viable on a much earlier tech base
$endgroup$
– mgh42
Jun 4 at 23:08
|
show 1 more comment
$begingroup$
Huh... neat. I'll look into it. Still for the sake of convenience, may I ask what level of technological infrastructure is required to do this?
$endgroup$
– Globin347
Jun 4 at 5:44
1
$begingroup$
@Globin347 From the linked article, it was released in 1991... You could probably push it a couple decades earlier, but it might not work unless you can have the metal in an Ion form (and you are already using alloys).
$endgroup$
– Shadowzee
Jun 4 at 5:47
2
$begingroup$
@Globin347 Well, the first ever case of it was documented in 1785, nearly 100 years before the Maxwell equations integrated magnetism and electricity as a single fundamental force. So, I'd imagine that you could almost do it with medieval tech but I'd need to do more research to confirm
$endgroup$
– Tim B II
Jun 4 at 5:48
1
$begingroup$
I should probably mention- As far as I know, an alloy is just melting down two metals and mixing them together. Like I said, I'm not great with metallurgy.
$endgroup$
– Globin347
Jun 4 at 5:50
3
$begingroup$
@Globin347 you already have a source of electricity from your spectral copper which would made things like electroplating viable on a much earlier tech base
$endgroup$
– mgh42
Jun 4 at 23:08
$begingroup$
Huh... neat. I'll look into it. Still for the sake of convenience, may I ask what level of technological infrastructure is required to do this?
$endgroup$
– Globin347
Jun 4 at 5:44
$begingroup$
Huh... neat. I'll look into it. Still for the sake of convenience, may I ask what level of technological infrastructure is required to do this?
$endgroup$
– Globin347
Jun 4 at 5:44
1
1
$begingroup$
@Globin347 From the linked article, it was released in 1991... You could probably push it a couple decades earlier, but it might not work unless you can have the metal in an Ion form (and you are already using alloys).
$endgroup$
– Shadowzee
Jun 4 at 5:47
$begingroup$
@Globin347 From the linked article, it was released in 1991... You could probably push it a couple decades earlier, but it might not work unless you can have the metal in an Ion form (and you are already using alloys).
$endgroup$
– Shadowzee
Jun 4 at 5:47
2
2
$begingroup$
@Globin347 Well, the first ever case of it was documented in 1785, nearly 100 years before the Maxwell equations integrated magnetism and electricity as a single fundamental force. So, I'd imagine that you could almost do it with medieval tech but I'd need to do more research to confirm
$endgroup$
– Tim B II
Jun 4 at 5:48
$begingroup$
@Globin347 Well, the first ever case of it was documented in 1785, nearly 100 years before the Maxwell equations integrated magnetism and electricity as a single fundamental force. So, I'd imagine that you could almost do it with medieval tech but I'd need to do more research to confirm
$endgroup$
– Tim B II
Jun 4 at 5:48
1
1
$begingroup$
I should probably mention- As far as I know, an alloy is just melting down two metals and mixing them together. Like I said, I'm not great with metallurgy.
$endgroup$
– Globin347
Jun 4 at 5:50
$begingroup$
I should probably mention- As far as I know, an alloy is just melting down two metals and mixing them together. Like I said, I'm not great with metallurgy.
$endgroup$
– Globin347
Jun 4 at 5:50
3
3
$begingroup$
@Globin347 you already have a source of electricity from your spectral copper which would made things like electroplating viable on a much earlier tech base
$endgroup$
– mgh42
Jun 4 at 23:08
$begingroup$
@Globin347 you already have a source of electricity from your spectral copper which would made things like electroplating viable on a much earlier tech base
$endgroup$
– mgh42
Jun 4 at 23:08
|
show 1 more comment
$begingroup$
Differential Spectrality
In bladesmithing, there is a technique called differential hardening. This simply means that different parts of the blade are cooled at different rates. This creates different types of steel with different properties.
The Japanese achieved this by coating parts of their katana blades with clay before tempering them. This meant that the edge cooled slower, making it harder and more suitable for holding an edge, where as the back cooled quicker and was softer, meaning if the edge chipped (as the edge is very hard and prone to damage), a crack wouldn’t form across the whole blade and cause it to break in two. (As a side note, this is why the katana curves, the back cooling faster than the edge means the steel is pulled back. If you wanted your blade to be straight, you would make it curved forwards before tempering so, when it bent back, it would be straight.)
Applying this to your question, your swords may undergo ‘differential spectrality’ where the edge of the blade is made to be more spectral than the back of the blade. The entire blade might initially be made of the same metal, such as steel, but you coat the back of the blade in, lets say, clay. This mean when you make the metal spectral, only the edge is spectral, the back of it is still very mundane as the clay prevented the spectral energy infusing the metal underneath it. Once it has finished undergoing the process, you would have a blade with a mundane steel back with a spectral steel edge.
$endgroup$
2
$begingroup$
This is a neat idea... unfortunately, It's extremely difficult to "make" the metal spectral. Typically, spectral metal is found, not made. It can be diluted by melting it with conventional metal, however, and if I find a way to spectralize metal, I'll keep this in mind.
$endgroup$
– Globin347
Jun 4 at 14:37
$begingroup$
@Globin347 Ah well, never mind then. Still, as you say, its something you can keep in mind if your scientists ever discover a way to artificially recreate spectral metal. (Perhaps artificial spectral metal has slightly different properties than its true counterpart? Though thats another question for another time).
$endgroup$
– Liam Morris
Jun 4 at 16:20
add a comment |
$begingroup$
Differential Spectrality
In bladesmithing, there is a technique called differential hardening. This simply means that different parts of the blade are cooled at different rates. This creates different types of steel with different properties.
The Japanese achieved this by coating parts of their katana blades with clay before tempering them. This meant that the edge cooled slower, making it harder and more suitable for holding an edge, where as the back cooled quicker and was softer, meaning if the edge chipped (as the edge is very hard and prone to damage), a crack wouldn’t form across the whole blade and cause it to break in two. (As a side note, this is why the katana curves, the back cooling faster than the edge means the steel is pulled back. If you wanted your blade to be straight, you would make it curved forwards before tempering so, when it bent back, it would be straight.)
Applying this to your question, your swords may undergo ‘differential spectrality’ where the edge of the blade is made to be more spectral than the back of the blade. The entire blade might initially be made of the same metal, such as steel, but you coat the back of the blade in, lets say, clay. This mean when you make the metal spectral, only the edge is spectral, the back of it is still very mundane as the clay prevented the spectral energy infusing the metal underneath it. Once it has finished undergoing the process, you would have a blade with a mundane steel back with a spectral steel edge.
$endgroup$
2
$begingroup$
This is a neat idea... unfortunately, It's extremely difficult to "make" the metal spectral. Typically, spectral metal is found, not made. It can be diluted by melting it with conventional metal, however, and if I find a way to spectralize metal, I'll keep this in mind.
$endgroup$
– Globin347
Jun 4 at 14:37
$begingroup$
@Globin347 Ah well, never mind then. Still, as you say, its something you can keep in mind if your scientists ever discover a way to artificially recreate spectral metal. (Perhaps artificial spectral metal has slightly different properties than its true counterpart? Though thats another question for another time).
$endgroup$
– Liam Morris
Jun 4 at 16:20
add a comment |
$begingroup$
Differential Spectrality
In bladesmithing, there is a technique called differential hardening. This simply means that different parts of the blade are cooled at different rates. This creates different types of steel with different properties.
The Japanese achieved this by coating parts of their katana blades with clay before tempering them. This meant that the edge cooled slower, making it harder and more suitable for holding an edge, where as the back cooled quicker and was softer, meaning if the edge chipped (as the edge is very hard and prone to damage), a crack wouldn’t form across the whole blade and cause it to break in two. (As a side note, this is why the katana curves, the back cooling faster than the edge means the steel is pulled back. If you wanted your blade to be straight, you would make it curved forwards before tempering so, when it bent back, it would be straight.)
Applying this to your question, your swords may undergo ‘differential spectrality’ where the edge of the blade is made to be more spectral than the back of the blade. The entire blade might initially be made of the same metal, such as steel, but you coat the back of the blade in, lets say, clay. This mean when you make the metal spectral, only the edge is spectral, the back of it is still very mundane as the clay prevented the spectral energy infusing the metal underneath it. Once it has finished undergoing the process, you would have a blade with a mundane steel back with a spectral steel edge.
$endgroup$
Differential Spectrality
In bladesmithing, there is a technique called differential hardening. This simply means that different parts of the blade are cooled at different rates. This creates different types of steel with different properties.
The Japanese achieved this by coating parts of their katana blades with clay before tempering them. This meant that the edge cooled slower, making it harder and more suitable for holding an edge, where as the back cooled quicker and was softer, meaning if the edge chipped (as the edge is very hard and prone to damage), a crack wouldn’t form across the whole blade and cause it to break in two. (As a side note, this is why the katana curves, the back cooling faster than the edge means the steel is pulled back. If you wanted your blade to be straight, you would make it curved forwards before tempering so, when it bent back, it would be straight.)
Applying this to your question, your swords may undergo ‘differential spectrality’ where the edge of the blade is made to be more spectral than the back of the blade. The entire blade might initially be made of the same metal, such as steel, but you coat the back of the blade in, lets say, clay. This mean when you make the metal spectral, only the edge is spectral, the back of it is still very mundane as the clay prevented the spectral energy infusing the metal underneath it. Once it has finished undergoing the process, you would have a blade with a mundane steel back with a spectral steel edge.
edited Jun 4 at 9:52
answered Jun 4 at 9:47


Liam MorrisLiam Morris
4,502642
4,502642
2
$begingroup$
This is a neat idea... unfortunately, It's extremely difficult to "make" the metal spectral. Typically, spectral metal is found, not made. It can be diluted by melting it with conventional metal, however, and if I find a way to spectralize metal, I'll keep this in mind.
$endgroup$
– Globin347
Jun 4 at 14:37
$begingroup$
@Globin347 Ah well, never mind then. Still, as you say, its something you can keep in mind if your scientists ever discover a way to artificially recreate spectral metal. (Perhaps artificial spectral metal has slightly different properties than its true counterpart? Though thats another question for another time).
$endgroup$
– Liam Morris
Jun 4 at 16:20
add a comment |
2
$begingroup$
This is a neat idea... unfortunately, It's extremely difficult to "make" the metal spectral. Typically, spectral metal is found, not made. It can be diluted by melting it with conventional metal, however, and if I find a way to spectralize metal, I'll keep this in mind.
$endgroup$
– Globin347
Jun 4 at 14:37
$begingroup$
@Globin347 Ah well, never mind then. Still, as you say, its something you can keep in mind if your scientists ever discover a way to artificially recreate spectral metal. (Perhaps artificial spectral metal has slightly different properties than its true counterpart? Though thats another question for another time).
$endgroup$
– Liam Morris
Jun 4 at 16:20
2
2
$begingroup$
This is a neat idea... unfortunately, It's extremely difficult to "make" the metal spectral. Typically, spectral metal is found, not made. It can be diluted by melting it with conventional metal, however, and if I find a way to spectralize metal, I'll keep this in mind.
$endgroup$
– Globin347
Jun 4 at 14:37
$begingroup$
This is a neat idea... unfortunately, It's extremely difficult to "make" the metal spectral. Typically, spectral metal is found, not made. It can be diluted by melting it with conventional metal, however, and if I find a way to spectralize metal, I'll keep this in mind.
$endgroup$
– Globin347
Jun 4 at 14:37
$begingroup$
@Globin347 Ah well, never mind then. Still, as you say, its something you can keep in mind if your scientists ever discover a way to artificially recreate spectral metal. (Perhaps artificial spectral metal has slightly different properties than its true counterpart? Though thats another question for another time).
$endgroup$
– Liam Morris
Jun 4 at 16:20
$begingroup$
@Globin347 Ah well, never mind then. Still, as you say, its something you can keep in mind if your scientists ever discover a way to artificially recreate spectral metal. (Perhaps artificial spectral metal has slightly different properties than its true counterpart? Though thats another question for another time).
$endgroup$
– Liam Morris
Jun 4 at 16:20
add a comment |
$begingroup$
One technique you could use is a bastardization of the San Mai technique.
Simply, San Mai is a technique that builds off forge welding - heat multiple pieces of metal up and apply pressure (hammer) until they become one solid piece. This is how one makes damascus or pattern-welded steel - Forge weld several layers of different steels together, cut in in half or fold it or twist it (whatever) and keep doing that a few times to get a really interesting pattern.
San Mai is a variation on that that's more simple to grasp - you effectively take one steel, fold it into a taco shape, and inset another steel as the "meat" of the taco. Then proceed to forge weld those two pieces together (but you don't add extra steps - no folding, twisting, etc). Typically that'd be used to have a hard steel edge and core, with a much softer steel case to better absorb the shocks (the softer steel is literally less harden-able, so you don't have to worry about differential heating as much, just get the whole piece to heat and quench the whole thing).
What I'd imagine as your "masterwork" case would be some variation on this. Where you first make a billet that has the spectral properties you want, and then do a San Mai on it to strengthen it. An example:
You want a sword to be good against both fairies and werewolves, so you want both spectral iron and silver; but it should still be effective against people so we still need a hard steel edge. We start with three mostly-flat billets (one of each). Stack them Spectral - Steel - Spectral; and forge weld that. So now we have a single sandwich billet where the core is hard steel and each side is the less-strong spectral metals. Flatten that enough to be the blade. Then we make our taco out of softer steel (to better absorb the blows), and inlay the other billet such that it still sticks out a fair amount. Forge weld that together, and grind down the blade and harden/temper the construction.
You now have a blade where the cutting edge is hard steel, and flanking that are your two varieties of spectral metals. On a solid chop or a stab, you'd get contact on all 3 metals; but most of initial impact shock should be absorbed by the hard steel and the soft shell. Super effective if you don't need the spectral metal to be the one material penetrating.
If you do need that, you could still use the san mai technique, but rather than forging one sandwich, you could instead use different metals at different chunks of the edge. I.e. forge weld a few billets end-to-end so you have a very long billet that's e.g. Spectral silver for the first 6 inches followed by 2 feet of steel. Put that right in the soft taco. Forge as needed, and you end up with a blade that has 6 inches (either at the tip or the base) that's less durable, but super-effective. May work especially well for forging axes - a few inches in the beard inset for werewolf-killing, but the main belly of the chopping edge in hardened steel.
$endgroup$
$begingroup$
Came here to say a san mai would be the approach I would go for. Leaves the core 'magical' metal in one piece with the edge exposed, but allowing the strength of the 'normal' metal
$endgroup$
– Randomhero
Jun 5 at 10:20
add a comment |
$begingroup$
One technique you could use is a bastardization of the San Mai technique.
Simply, San Mai is a technique that builds off forge welding - heat multiple pieces of metal up and apply pressure (hammer) until they become one solid piece. This is how one makes damascus or pattern-welded steel - Forge weld several layers of different steels together, cut in in half or fold it or twist it (whatever) and keep doing that a few times to get a really interesting pattern.
San Mai is a variation on that that's more simple to grasp - you effectively take one steel, fold it into a taco shape, and inset another steel as the "meat" of the taco. Then proceed to forge weld those two pieces together (but you don't add extra steps - no folding, twisting, etc). Typically that'd be used to have a hard steel edge and core, with a much softer steel case to better absorb the shocks (the softer steel is literally less harden-able, so you don't have to worry about differential heating as much, just get the whole piece to heat and quench the whole thing).
What I'd imagine as your "masterwork" case would be some variation on this. Where you first make a billet that has the spectral properties you want, and then do a San Mai on it to strengthen it. An example:
You want a sword to be good against both fairies and werewolves, so you want both spectral iron and silver; but it should still be effective against people so we still need a hard steel edge. We start with three mostly-flat billets (one of each). Stack them Spectral - Steel - Spectral; and forge weld that. So now we have a single sandwich billet where the core is hard steel and each side is the less-strong spectral metals. Flatten that enough to be the blade. Then we make our taco out of softer steel (to better absorb the blows), and inlay the other billet such that it still sticks out a fair amount. Forge weld that together, and grind down the blade and harden/temper the construction.
You now have a blade where the cutting edge is hard steel, and flanking that are your two varieties of spectral metals. On a solid chop or a stab, you'd get contact on all 3 metals; but most of initial impact shock should be absorbed by the hard steel and the soft shell. Super effective if you don't need the spectral metal to be the one material penetrating.
If you do need that, you could still use the san mai technique, but rather than forging one sandwich, you could instead use different metals at different chunks of the edge. I.e. forge weld a few billets end-to-end so you have a very long billet that's e.g. Spectral silver for the first 6 inches followed by 2 feet of steel. Put that right in the soft taco. Forge as needed, and you end up with a blade that has 6 inches (either at the tip or the base) that's less durable, but super-effective. May work especially well for forging axes - a few inches in the beard inset for werewolf-killing, but the main belly of the chopping edge in hardened steel.
$endgroup$
$begingroup$
Came here to say a san mai would be the approach I would go for. Leaves the core 'magical' metal in one piece with the edge exposed, but allowing the strength of the 'normal' metal
$endgroup$
– Randomhero
Jun 5 at 10:20
add a comment |
$begingroup$
One technique you could use is a bastardization of the San Mai technique.
Simply, San Mai is a technique that builds off forge welding - heat multiple pieces of metal up and apply pressure (hammer) until they become one solid piece. This is how one makes damascus or pattern-welded steel - Forge weld several layers of different steels together, cut in in half or fold it or twist it (whatever) and keep doing that a few times to get a really interesting pattern.
San Mai is a variation on that that's more simple to grasp - you effectively take one steel, fold it into a taco shape, and inset another steel as the "meat" of the taco. Then proceed to forge weld those two pieces together (but you don't add extra steps - no folding, twisting, etc). Typically that'd be used to have a hard steel edge and core, with a much softer steel case to better absorb the shocks (the softer steel is literally less harden-able, so you don't have to worry about differential heating as much, just get the whole piece to heat and quench the whole thing).
What I'd imagine as your "masterwork" case would be some variation on this. Where you first make a billet that has the spectral properties you want, and then do a San Mai on it to strengthen it. An example:
You want a sword to be good against both fairies and werewolves, so you want both spectral iron and silver; but it should still be effective against people so we still need a hard steel edge. We start with three mostly-flat billets (one of each). Stack them Spectral - Steel - Spectral; and forge weld that. So now we have a single sandwich billet where the core is hard steel and each side is the less-strong spectral metals. Flatten that enough to be the blade. Then we make our taco out of softer steel (to better absorb the blows), and inlay the other billet such that it still sticks out a fair amount. Forge weld that together, and grind down the blade and harden/temper the construction.
You now have a blade where the cutting edge is hard steel, and flanking that are your two varieties of spectral metals. On a solid chop or a stab, you'd get contact on all 3 metals; but most of initial impact shock should be absorbed by the hard steel and the soft shell. Super effective if you don't need the spectral metal to be the one material penetrating.
If you do need that, you could still use the san mai technique, but rather than forging one sandwich, you could instead use different metals at different chunks of the edge. I.e. forge weld a few billets end-to-end so you have a very long billet that's e.g. Spectral silver for the first 6 inches followed by 2 feet of steel. Put that right in the soft taco. Forge as needed, and you end up with a blade that has 6 inches (either at the tip or the base) that's less durable, but super-effective. May work especially well for forging axes - a few inches in the beard inset for werewolf-killing, but the main belly of the chopping edge in hardened steel.
$endgroup$
One technique you could use is a bastardization of the San Mai technique.
Simply, San Mai is a technique that builds off forge welding - heat multiple pieces of metal up and apply pressure (hammer) until they become one solid piece. This is how one makes damascus or pattern-welded steel - Forge weld several layers of different steels together, cut in in half or fold it or twist it (whatever) and keep doing that a few times to get a really interesting pattern.
San Mai is a variation on that that's more simple to grasp - you effectively take one steel, fold it into a taco shape, and inset another steel as the "meat" of the taco. Then proceed to forge weld those two pieces together (but you don't add extra steps - no folding, twisting, etc). Typically that'd be used to have a hard steel edge and core, with a much softer steel case to better absorb the shocks (the softer steel is literally less harden-able, so you don't have to worry about differential heating as much, just get the whole piece to heat and quench the whole thing).
What I'd imagine as your "masterwork" case would be some variation on this. Where you first make a billet that has the spectral properties you want, and then do a San Mai on it to strengthen it. An example:
You want a sword to be good against both fairies and werewolves, so you want both spectral iron and silver; but it should still be effective against people so we still need a hard steel edge. We start with three mostly-flat billets (one of each). Stack them Spectral - Steel - Spectral; and forge weld that. So now we have a single sandwich billet where the core is hard steel and each side is the less-strong spectral metals. Flatten that enough to be the blade. Then we make our taco out of softer steel (to better absorb the blows), and inlay the other billet such that it still sticks out a fair amount. Forge weld that together, and grind down the blade and harden/temper the construction.
You now have a blade where the cutting edge is hard steel, and flanking that are your two varieties of spectral metals. On a solid chop or a stab, you'd get contact on all 3 metals; but most of initial impact shock should be absorbed by the hard steel and the soft shell. Super effective if you don't need the spectral metal to be the one material penetrating.
If you do need that, you could still use the san mai technique, but rather than forging one sandwich, you could instead use different metals at different chunks of the edge. I.e. forge weld a few billets end-to-end so you have a very long billet that's e.g. Spectral silver for the first 6 inches followed by 2 feet of steel. Put that right in the soft taco. Forge as needed, and you end up with a blade that has 6 inches (either at the tip or the base) that's less durable, but super-effective. May work especially well for forging axes - a few inches in the beard inset for werewolf-killing, but the main belly of the chopping edge in hardened steel.
answered Jun 4 at 18:15
DeliothDelioth
28317
28317
$begingroup$
Came here to say a san mai would be the approach I would go for. Leaves the core 'magical' metal in one piece with the edge exposed, but allowing the strength of the 'normal' metal
$endgroup$
– Randomhero
Jun 5 at 10:20
add a comment |
$begingroup$
Came here to say a san mai would be the approach I would go for. Leaves the core 'magical' metal in one piece with the edge exposed, but allowing the strength of the 'normal' metal
$endgroup$
– Randomhero
Jun 5 at 10:20
$begingroup$
Came here to say a san mai would be the approach I would go for. Leaves the core 'magical' metal in one piece with the edge exposed, but allowing the strength of the 'normal' metal
$endgroup$
– Randomhero
Jun 5 at 10:20
$begingroup$
Came here to say a san mai would be the approach I would go for. Leaves the core 'magical' metal in one piece with the edge exposed, but allowing the strength of the 'normal' metal
$endgroup$
– Randomhero
Jun 5 at 10:20
add a comment |
$begingroup$
Don't make a sword.
Make a bludgeoning weapon instead, like a mace or a banded wooden club. Brittleness will be less of an issue.
If you really want a sword, there are those whose blade are heavy and not really sharp at all. They're designed to break armor; I refer to them as "aerodynamic clubs." Again, brittleness isn't an issue.
If you want to get really fancy, make one edge sharp (for nonmagical opponents) and the other non-sharp (for fairy werewolves). You need special fighting techniques for this, or at least be able to flip your grip in a hurry.
$endgroup$
$begingroup$
I like your last suggestion of one sharp edge and one special edge
$endgroup$
– Cullub
Jun 5 at 11:22
add a comment |
$begingroup$
Don't make a sword.
Make a bludgeoning weapon instead, like a mace or a banded wooden club. Brittleness will be less of an issue.
If you really want a sword, there are those whose blade are heavy and not really sharp at all. They're designed to break armor; I refer to them as "aerodynamic clubs." Again, brittleness isn't an issue.
If you want to get really fancy, make one edge sharp (for nonmagical opponents) and the other non-sharp (for fairy werewolves). You need special fighting techniques for this, or at least be able to flip your grip in a hurry.
$endgroup$
$begingroup$
I like your last suggestion of one sharp edge and one special edge
$endgroup$
– Cullub
Jun 5 at 11:22
add a comment |
$begingroup$
Don't make a sword.
Make a bludgeoning weapon instead, like a mace or a banded wooden club. Brittleness will be less of an issue.
If you really want a sword, there are those whose blade are heavy and not really sharp at all. They're designed to break armor; I refer to them as "aerodynamic clubs." Again, brittleness isn't an issue.
If you want to get really fancy, make one edge sharp (for nonmagical opponents) and the other non-sharp (for fairy werewolves). You need special fighting techniques for this, or at least be able to flip your grip in a hurry.
$endgroup$
Don't make a sword.
Make a bludgeoning weapon instead, like a mace or a banded wooden club. Brittleness will be less of an issue.
If you really want a sword, there are those whose blade are heavy and not really sharp at all. They're designed to break armor; I refer to them as "aerodynamic clubs." Again, brittleness isn't an issue.
If you want to get really fancy, make one edge sharp (for nonmagical opponents) and the other non-sharp (for fairy werewolves). You need special fighting techniques for this, or at least be able to flip your grip in a hurry.
answered Jun 5 at 5:42


Shawn V. WilsonShawn V. Wilson
40528
40528
$begingroup$
I like your last suggestion of one sharp edge and one special edge
$endgroup$
– Cullub
Jun 5 at 11:22
add a comment |
$begingroup$
I like your last suggestion of one sharp edge and one special edge
$endgroup$
– Cullub
Jun 5 at 11:22
$begingroup$
I like your last suggestion of one sharp edge and one special edge
$endgroup$
– Cullub
Jun 5 at 11:22
$begingroup$
I like your last suggestion of one sharp edge and one special edge
$endgroup$
– Cullub
Jun 5 at 11:22
add a comment |
u4s97V kqn2Sv1UO8bA3V,Q,wa7fV n I1vW,g2 qabZC5yHIqvnp97iqn vMGqtVv6 hxRBCn1ZwN eQ,B hpRY,IF
$begingroup$
Comments are not for extended discussion; this conversation has been moved to chat.
$endgroup$
– James♦
Jun 4 at 20:47
$begingroup$
The help center states, "To prevent your question from being flagged and possibly removed, avoid asking subjective questions where … your answer is provided along with the question, and you expect more answers." SE is not a discussion forum. SE's Q&A model is one-specific-question/one-best-answer. To answer the fundamental Q we would need to know where your metal falls in the periodic table (to deal with allowing/annealing) and your magic system. Can you edit this to meet all these expectations?
$endgroup$
– JBH
Jun 5 at 19:32
$begingroup$
If (for instance) said sword could build electric energy would it ever actually hit anything or could it just shoot a bolt of electricity, leaving the blade unharmed?
$endgroup$
– A Writer
Jun 5 at 19:33